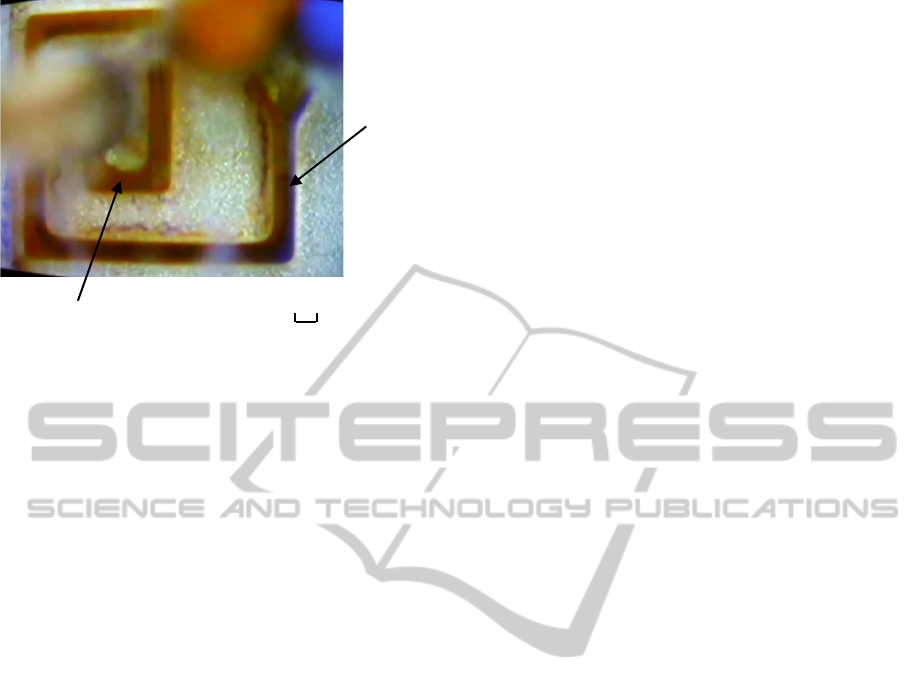
100µm
Separated
Mixed
Figure 15: Example of micro-mixing.
similarly were successfully mixed in a snail-shape
channel, as shown in Fig. 15. In this case, liquids
coloured in red and blue were used. Separated red
and blue flows were gradually mixed after they
passed corners. Accordingly, it is thought that the
liquids will be mixed if the shape of the channel is
improved. A lot of papers had been written on
micro-mixing in micro-fluidic devices (Jain, et al.,
2013) (Rahimi, M., et al., 2014). Considering the
reported remarks, vigorous research efforts should
be done hereafter.
6 CONCLUSIONS
A very simple and low-cost exposure tool was
developed, and applied to fabricate micro-fluidic
devices in which resist patterns were directly used as
flow paths. In spite of using such a simple and low-
cost tool, precise flow-paths with perpendicular
sidewalls were successfully fabricated, because a
blue filter was inserted to adjust the light absorption
of the thick resist film. Micro-fluidic device chips
made by the resist were embedded in the plastic
vessels, and capped by the lids. Although the lids
were simply bound with the vessels using small
bolts and nuts, injected fluids were flown without
leaks. The developed tool and the method to
fabricate micro-fluidic devices will be effective and
useful for economical small-volume production.
ACKNOWLEDGEMENTS
This work was partially supported by Research
Institute for Science and Technology of Tokyo
Denki University, Grant Number Q13T-02.
REFERENCES
Avram, M., Iliescu, C., Volmer, M., Avram, A., 2008.
Microfluidic device for magnetic separation in lab-on-
a-chip systems, Digest of Papers, Microprocesses and
Nanotechnology 2008, 21
st
International
Microprocesses and Nanotechnology Conference,
442-443.
Bouhadda, I., Sagazan, O., Bihan, F. L., 2012. Suspended
Gate Field Effect Transistor with an Integrated Micro-
Fluidic Channel Performed by Surface
Micromachining for Liquids Sensing, Procedia
Engineering 47, 754-757.
Campbel, K., McGrath, T., Sjölander, S., Hanson, T.,
Tidare, M., Jansson, Ö., Moberg, A., Mooney, M.,
Elliott, C., Buijs, J., 2011. Use of a novel micro-fluidic
device to create arrays for multiplex analysis of large
and small molecular weight compounds by surface
plasmon resonance, Biosensors and Bioelectronics 26,
3029-3036.
Chen, C. S., Chen, S. C., Liao, W. H., Chien, R. D., Lin, S.
H., 2010. Micro injection molding of a micro-fluidic
platform, International Communications in Heart and
Mass Transfer 37, 1290-1294.Jacobs, T., Kutzner, C.
Kropp, M., Brokmann, G., Lang, W., Steinke, A.,
Kienke, A., Hauptmann, P., 2009. Combination of a
novel perforated thermoelectric flow and impedimetric
sensor for monitoring chemical conversion in micro
fluidic channels, Procedia Chemistry 1, 1127-1130.
Curto, V. F., Fay, C., Coyle, S., Byrne, R., O’Toole, C.,
Barry, C., Hughes, S., Moyna, N., Diamond, D.,
Lopez, F. B., 2012. Real-time sweat pH monitoring
based on a wearable chemical barcode micro-fluidic
platform incorporating ionic liquids, Sensors and
Actuators B 171-172, 1327-1334.
Eun, D. S., Kong, D. Y., Chang, S. J., Yoo, J. H., Hong, Y.
M., Shin, J. K., Lee, J. H., 2008. Micro-PCR Chip
with Nanofluidic Heat-Sink for Faster Temperature
Changes, Digest of Papers, Microprocesses and
Nanotechnology 2008, 21
st
International
Microprocesses and Nanotechnology Conference ,
448-449.
Horiuchi, T., Watanabe, H., Hayashi, N., Kitamura, T.,
2010. Simply Fabricated Precise microfluidic Mixer
with Resist Flow Paths Sealed by an Acrylic Lid,
Proceedings of The third International Conference on
Biomedical Electronics and Devices, 82-87.
Jain, M., Nandakumar, K., 2013. Optimal patterning of
heterogeneous surface charge for improved
electrokinetic micromixing, Computers and Chemical
Engineering 49, 18-24.
Kashkary, L., Kemp, C., Shaw, K. J., Greenway, G. M.,
Haswell, S. J., 2012. Improved DNA extraction
efficiency from low level cell numbers using a silica
monolith based micro fluidic device, Analytica
BIODEVICES2014-InternationalConferenceonBiomedicalElectronicsandDevices
10