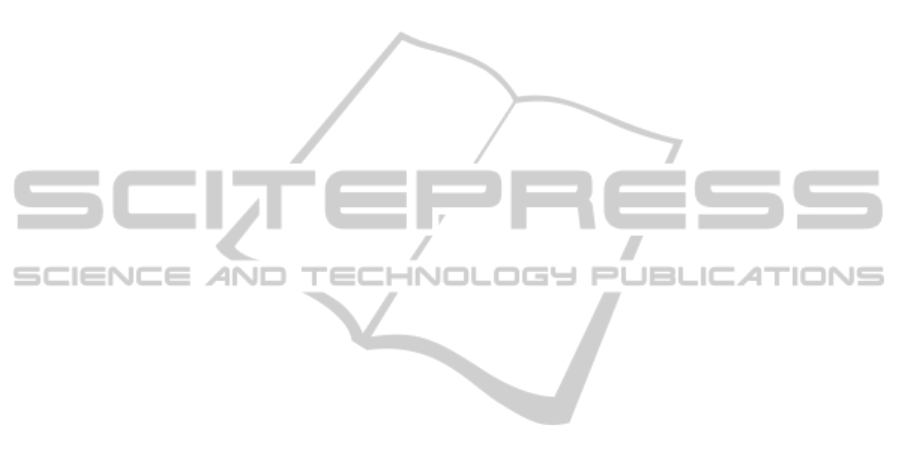
vibrations and can be used to check the vibration
transmissibility of manual wheelchair.
In further work, this test bench will be used to
investigate the vibration effect and the wheelchair
design (rigid frame, foldable, wheel camber) as well
as tires and cushion damping effects on the harmful
vibration magnitude.
ACKNOWLEDGEMENTS
This work was supported in part by MESRS
ministry under grant J0200220100018. The authors
wish to thank Mr H. Zerouali for his participation in
the prototype developing.
REFERENCES
Bovenzi, M., 2005, ‘Health effects of mechanical
vibration’, G. Ital. Med. Lav. Erg., vol.27, n°1, pp.58-
64.
Bovenzi, M., 2010, ‘A longitudinal study of low back pain
and daily vibration exposure in professional drivers’,
Industrial Health, vol.48, pp.584-595.
Burton, M., Fuss, F. K., and Subic A., 2010, ‘Sports
wheelchair technologies’. Sports Technology vol.3,
n°3, pp. 154–167.
Cooper, R. A., Teodorski, E. E., Sporner M. L., and
Collins, D. M., 2011, ‘Manual wheelchair propulsion
over cross-sloped surfaces: a literature review’.
Assistive Technology, vol.23, pp.42–51.
European Commission Directive ECD 2002/44/EC of the
European Parliament and of the Council, 2002. ‘on
the minimum health and safety requirements regarding
exposure of workers to the risks arising from physical
agents (vibration) ’, Official Journal of the European
Communities vol. L177, pp.13-19.
Garcia-Mendez, Y., Pearlman, J. L., Cooper, R. A.,
Boninger, M. L., 2012, ‘Dynamic stiffness and
transmissibility of commercially available wheelchair
cushions using a laboratory test method’, Journal of
Rehabilitation Research & Development, vol.49, n°1,
pp. 7-22.
International Organization for Standardization, 1997,
‘Mechanical vibration and shock Evaluation of human
exposure to whole-body vibration Part 1: General
requirements (ISO 2631-1)’.
Johanning, E., 2011, ‘Diagnosis of whole-body vibration
related health problems in occupational medicine’,
Journal of Low Frequency Noise, Vibration and
Active Control, vol.30, n°3, pp.207-220.
Kittusamy, N. K. and Buchholz, B., 2004, ‘Whole-body
vibration and postural stress among operators of
construction equipment: a literature review’, Journal
of Safety Research, vol.35, n°3, pp.255-261.
Maeda, S., Futatsuka, M., Yonesaki, J., Ikeda, M., 2003,
‘Relationship between questionnaire qurvey results of
vibration complaints of wheelchair users and vibration
transmissibility of manual wheelchair’, Environmental
Health and Preventative Medicine, vol.8, pp. 82-89.
Pearlman, J., Cooper, R., Duvall, J., Livingston, R., 2013,
‘Pedestrian pathway characteristics and their
implications on wheelchair users’, Assistive
Technology, vol.25, pp.230-239.
Rimell, A. N. and Mansfield, N. J., 2007, ‘Design of
digital filters for frequency weightings required for
risk assessments of workers exposed to vibration’,
Industrial Health, vol.45, n°4, pp.512–519.
Rispin, K., and Wee, J., 2013, ‘A paired outcomes study
comparing two pediatric wheelchairs for low resource
settings; the Regency pediatric wheelchair and a
similarly sized wheelchair made in Kenya’. Assistive
Technology, DOI: 10.1080/10400435. 2013.83784
Qiu, Y., Griffin, M. J., 2012, ‘Biodynamic response of the
seated human body to single-axis and dual-axis
vibration: effect of backrest and non-linearity’,
Industrial Health, vol.50, n°1, pp.37–51.
VanSickle, D. P., Cooper, R. A., Boninger, M. L.,
DiGiovine, C. P., 2001. ‘Analysis of vibrations
induced during wheelchair propulsion’, Journal of
Rehabilitation Research & Development, vol.38, n°4,
pp. 409-421.
Wolf, E. J., Pearlman, J., Cooper, R. A., Fitzgerald, S. G.,
Kelleher, A., Collins, D. M., Boninger, M. L., Cooper,
R., 2005, ‘Vibration exposure of individuals using
wheelchairs over sidewalk surfaces’. Disability &
Rehabilitation, vol.27, n°23, pp. 1443-1449.
Wolf, E., Cooper, R. A., Pearlman, J., Fitzgerald, S. G.,
Kelleher, A., 2007, ‘Longitudinal assessment of
vibrations during manual and power wheelchair
driving over select sidewalk surfaces’, Journal of
Rehabilitation Research & Development, vol.44, n°4,
pp. 573-580.
World Health Organization, World Bank, 2011, World
report on disability. Available from
http://whqlibdoc.who.int/hq/2011/WHO_NMH_VIP_
11.01_eng.pdf.
TestBenchforAnalysisofHarmfulVibrationsInducedtoWheelchairUsers
153