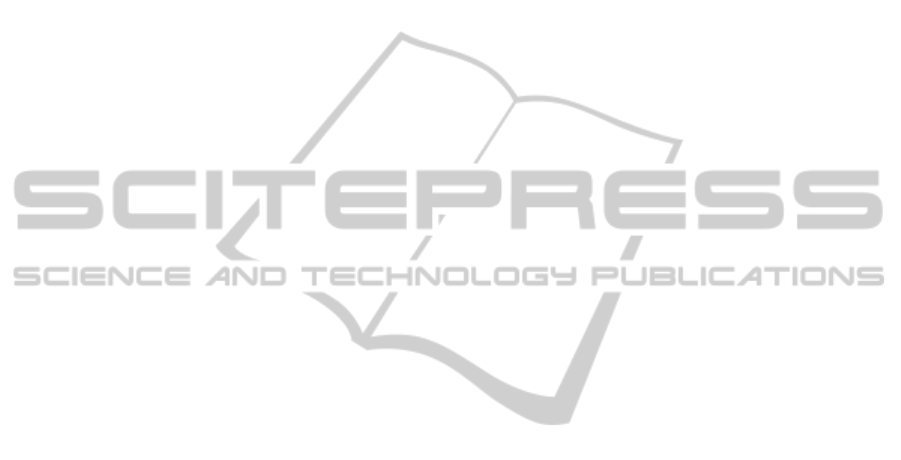
7 CONCLUSIONS
In practice supply chain network configuration
typically involves optimizing strategic decisions
without considering their impact on all the tactical
delivery planning and daily scheduling decisions. In
this paper we optimize not only strategic decisions
but also consider all tactical and operational
decisions in the mathematical model for the network
configuration. We specifically consider the
integrated network design problem dedicated to the
packaged gases distribution. The main goals for
solving the integrated network design problem
include determining the locations of the hubs and the
filling plants, the production capacity of the filling
plants, the primary and the secondary cylinders
flows and the inventory of both the filling plants and
the hubs. To solve it, we propose a mathematical
model which combines both the location-routing and
the location-inventory integrated models and
approximates the routing cost used in both the
integrated models. In order to solve real large-scale
problems, we propose approximate decomposition
based approach. We applied near-optimal and
approximate approaches on 3 real-life test cases
from packaged gases cylinder distribution. The
obtained solutions are within an acceptable
optimality gap from the optimal solutions. The
results indicate that mono-approach and two-steps
approaches are capable to generate good facility
location solutions in a reasonable time and are
comparable to near-optimal solutions on smaller test
cases. The difference between mono-product and
two-steps is that two-steps method provides a better
estimate of tactical and operational costs. For large-
scale test cases, it is hard to obtain near-optimal
solutions whereas two-steps approximation can
generate good solutions in an acceptable time.
Therefore, near-optimal approach is suitable for
smaller test cases and approximation approaches for
large-scale test cases.
In the future, further studies on improvements
relative to the computation time to solve the
complete model without using decomposition
approach can be envisioned. Also, further research
can be done to benchmark the approximate
approaches considered in this paper for large-scale
test cases. Even though we performed sensitivity
analysis for few input parameters, future work can
be focussed on developing and solving a robust
model for packaged gases network design.
REFERENCES
Adelman, D., 2003. A price-directed approach to
stochastic inventory/routing, Working Paper,
University of Chicago.
Balakrishnan, A., Ward, J. E., Wong, R. T., 1987.
Integrated facility location and vehicle routing models:
recent work and future prospects, American Journal of
Math. and Management Sciences, 7, 35-61.
Crainic, T. G., Laporte, G., 1997. Planning models for
freight transportation. European Journal of
Operations Research, 97, 409-438.
Daskin, M. S. and Owen, S. H., 1999. Location models in
transportation, in Handbook of Transportation Science
(Eds R. Hall), 311-360.
Erlebacher, S.J., Meller, R. D., 2000. The interaction of
location and inventory in designing distribution
systems. IIE Transactions, 32, 155-166.
Kleywegt, A., Nori, V. S., Savelsbergh, M. W. P., 2002.
The stochastic inventory routing problem with direct
deliveries. Transportation Science, 36, 94-118.
Klose, A., Drexl, A., 2005. Facility location models for
distribution system design. European Journal of
Operational Research, 162, 4–29.
Krarup, j., Pruzan, P. M., 1983. The simple plant location
problem-survey and synthesis. European Journal of
Operational Research, 2, 36-81.
Melo, M., Nickel, S., Saldanha-da-Gama, F., 2009.
Facility location and supply chain management – a
review. European Journal of Operations Research,
196 (2), 401–412.
ReVelle, C., Eiselt, H., 2005. Location analysis: a
Synthesis and survey. European Journal of
Operational Research, 165, 1–19.
Shen, Z. M., 2000. Approximation Algorithms for Various
Supply Chain Problems, PhD Thesis. Dept. of Ind.
Eng. and Mgmt. Sciences, Northwestern University.
IntegratedSupplyChainNetworkDesignforPackagedGases
381