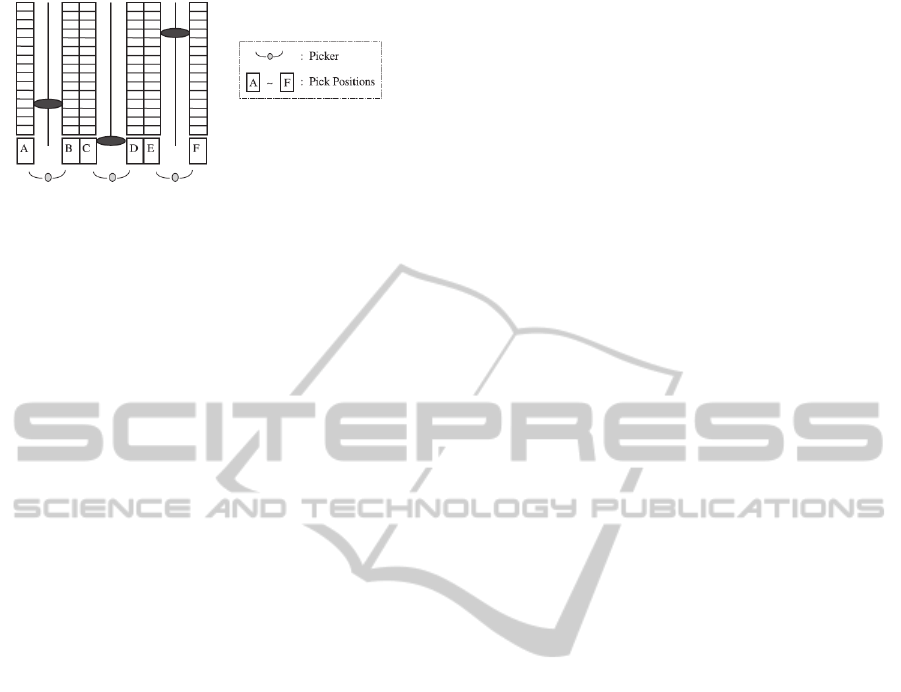
Figure 1: End-of-Aisle AS/RS order picking system
(Hwang et al., 2002).
They showed that significant reductions in S/R
machine travel time are achieved from turnover-
based storage rules such as a class-based storage
policy. Accordingly, Bozer and White (1984)
developed a continues rack configuration to
evaluate single and dual travel times for rectangular
racks and variety of I/O configurations.
Furthermore, Han et al., (1987) illustrated that by
sequencing the retrieval orders, the throughput
performance of the AS/RS can be improved. This
can thus reduce the interleaving travel time between
storage and retrieval locations in a dual command
cycle.
For simulation models in AS/RS, most of the
researchers only evaluated some of the physical
design aspects in combination with a limited
number of control policies. Meller and
Mungwattana (2005) applied simulation to evaluate
the benefits of different dwell point policies. The
results indicate that the position of dwell point
has an negligible effect on system respond time
when the AS/RS has high utilization. Randhawa and
Shroff (1995) examined the effect of different
sequencing rules on six layout configurations (with
varying I/O-point, item distribution over racks, rack
configuration and rack dimensions). Based on a
limited number of experiments they mentioned in
their study that the position of I/O point at the
middle of the rack results in a higher throughput.
Vanderberg et al., (2000) have developed a
simulation study and examined various aspects of
AS/RS control policies: storage location assignment
policies, request selection rules, open location
selection rules and urgency rules. Considering
randomized storage and class-based storage, they
concluded that using a FCFS sequence for the
retrievals by implementing urgency rules result in
better expected time. Randhawa et al., (1991) used
simulation to evaluate single and dual I/O point
configurations in a unit load AS/RS and their
model demonstrated that the dual dock layout
maximizes the throughput.
In an End-of-Aisle AS/RS, current retrieval
operation become next storage operation, since
loads are returned into the system after items have
been picked. A mathematical model to investigate
the performance of an EOA order picking systems
have been proposed by Bozer and White (1996).
They provided some approximate expressions for
the expected travel time for systems performing
under peak demand, and presented a design
algorithm in order to calculate the minimum
number of miniload aisles needed to meet a given
throughput requirement. Foley and Frazelle (1991)
have developed an exact solution for the S/R
machine travel time under the FCFS retrieval
policy in order to evaluate the throughput for the
miniload AS/RS. Hwang et al., (2002) proposed the
design of miniload AS/RSs in combination with
Automated Guided Vehicles. To recognize the
optimal number of loads transferred by each AGV
to machines, a non-linear model and heuristics have
been developed in their research.
To the best of our knowledge, there is no
simulation model for the End-of-Aisle system,
therefore in this study a multitude of physical design
aspects and control policies are simultaneously
included for the End-of-Aisle system.
3
SIMULATION MODELING
OF
THE SYSTEM
3.1 Assumptions
In the system analyzed, a crane serves a single aisle
with storage racks placed on one side of the aisle.
All storage locations are identical in size and each
location can hold one unit load. The total capacity
of the system is 100 unit loads. Each unit load
(e.g., pallet) contains a number of boxes of one
item type. Although the pallet sizes are constant,
the size of the boxes on the pallets are different for
different item types. The crane’s pick-up and
deposit time is calculated according to the size and
number of boxes inside the pallet; for pallets with a
higher number of boxes and larger boxes, the time
for pick- up and deposit is higher. Moreover, the
times for manual loading and unloading boxes from
pallets are calculated according to the boxes’
dimension.
The turnover of each itemtype is known in
advance and is the same for all scenarios tested.
The crane scheduling rule in this study is FCFS
(first come, first serve) for both storage and
retrieval operations. The capacity of the crane is
SimulationbasedPerformanceAnalysisofanEnd-of-AisleAutomatedStorageandRetrievalSystem
335