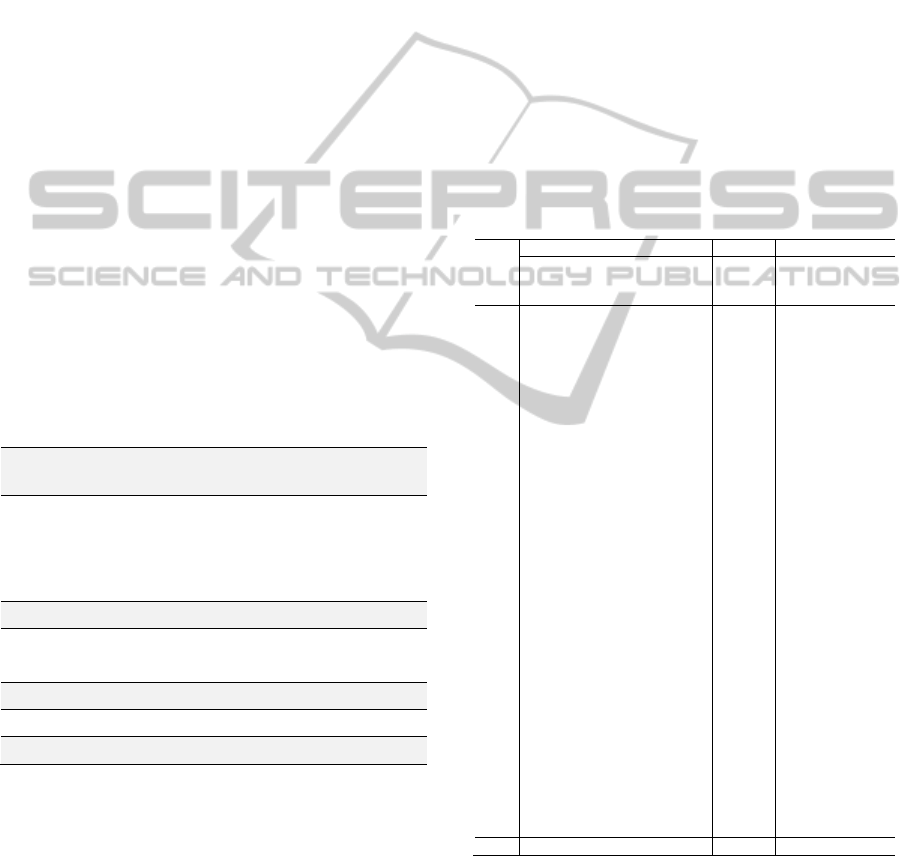
accountancy, and productivity of the integrated
process.
3.2 Material Balance
Dynamic material balance describes the amount of
feed, hold-up, and product in any process for every
batch operation. If accumulating the amounts of
received and departed material for a specific period,
an exact equilibrium material balance can be
obtained. Because the above operation procedure is
difficult to implement, an equilibrium material
balance tends to simplify the complicated operation
to the averaged one, i.e., every batch operation is
assumed to be the same. However, if we can build
an exact model through appropriate tools or
methodologies to reflect such tangled operation
requirement, the assumed equilibrium material
balance obtained from a flowsheet study can be
replaced with an exact material balance in an exact
model.
For comparison between equilibrium and
dynamic material balance, it is assumed that the
oxide reduction treats 10tHM per year, which
corresponds to 200 batch operations of process P2-1.
An equilibrium mass balance in process P2-1 is
shown in Table 1.
Table 1: Equilibrium material balance in P2-1.
Material via
stream
type SNF
mass(kg)
Salt
(LiCl, Li
2
O)
new salt feed - 824
pellet/fragment feed 11,331 -
recovered salt feed 5 350
regenerated salt feed 6 1,146
Sum of inputs 11,341 2,320
cathode product product 9,997 1,935
O
2
product 1,331 -
Sum of outputs 11,328 1,935
remaining salt hold-up 13 385
Sum of hold-up 13 385
Since the equilibrium material balance shows
accumulated results over numerous batch operations,
the difference of each batch is ignored. Process P2-1
has a total of 4 inputs and 2 outputs. The sums of the
inputs and outputs are not the same because process
P2-1 can hold a small amount of SNF in its bath.
Therefore, the sum of inputs exactly matches the
sum of outputs and hold-up. We cannot predict from
equilibrium material balance any transient behavior
affected by operation procedure described in section
3.1. Tables 2 and 3 show dynamic SNF and salt
balances, respectively, obtained from a discrete
event system (DES) model of oxide reduction. It
shows different results from every batch operation:
amount of inputs, outputs, and hold-up in process
P2-1 for every batch operation. In Table 2, every
batch operation of P2-1 receives 50kgHM/batch
fragment or pellet from the previous process
excluding O
2
weight. The 2
nd
column in Table 2
represents the minimum weight of oxide form of a
fragment or pellet. Excluding oxide, only the SNF
element weight becomes 50kgHM/batch. The weight
of oxide form can be more than the sum of 50kg and
O
2 weight measured at the output stream because
reduction yield ratios are not 100% about all SNF
oxide elements. The reduction yield ratio is one of
the parameters that significantly influence the
material balance at the out stream.
Table 2: SNF material balance in P2-1.
batch #
inputs hold-up outputs
fragment/
pellet(kg)
recovered
salt(kg)
egenerate
salt(kg)
remaining
salt(kg)
cathode
product
(kg)
O2(kg)
1 56.67 - - 0.28 49.72 6.67
2 56.67 - - 0.5
49.73 6.67
3 56.59 0.02 - 0.83 49.74 6.59
4 56.67 - - 1.08 49.75 6.67
5 56.59 - - 1.33 49.75 6.59
6 56.67 - - 1.57 49.76 6.67
7 56.59 0.05 - 1.85 49.77 6.59
8 56.67 - - 2.08 49.77 6.67
9 56.59 0.08 - 2.38 49.78 6.59
…………………
41 56.59 - - 10.25 49.97 6.59
42 56.67 - - 10.27 49.98 6.67
43 56.59 - - 10.3
49.97 6.59
44 56.67 - - 10.32 49.98 6.67
45 56.59 - - 10.35 49.97 6.59
46 56.67 - - 10.37 49.98 6.67
47 56.59 - - 10.4
49.97 6.59
…………………
81 56.59 - 0.08 11.03 49.99 6.59
82 56.67 - - 11.0
50.00 6.67
83 56.59 - 0.08 11.13 49.99 6.59
84 56.67 - - 11.13 50.00 6.67
85 56.59 - 0.08 11.21 49.99 6.59
86 56.67 - - 11.22 50.00 6.67
87 56.67 - 0.08 11.3
49.99 6.67
…………………
194 56.67 - - 13.3
50.05 6.67
195 56.67 - 0.11 13.37 50.04 6.67
196 56.67 - - 13.32 50.05 6.67
197 56.67 - 0.12 13.39 50.04 6.67
198 56.67 - - 13.3
50.05 6.67
199 56.67 - 0.12 13.41 50.04 6.67
200 56.67 - - 13.36 50.05 6.67
tota
11,331.06 4.55 5.66 13.36 9,996.85 1,331.06
For example, actinide elements are almost
reduced to metal form such that 99.5% of those
oxides convert into metal form but lanthanide
elements are rarely reduced such that only 30% of
those oxides convert into metal form. Generally, the
overall reaction for oxide reduction of an arbitrary
ModelingandSimulationofPyroprocessingOxideReduction
687