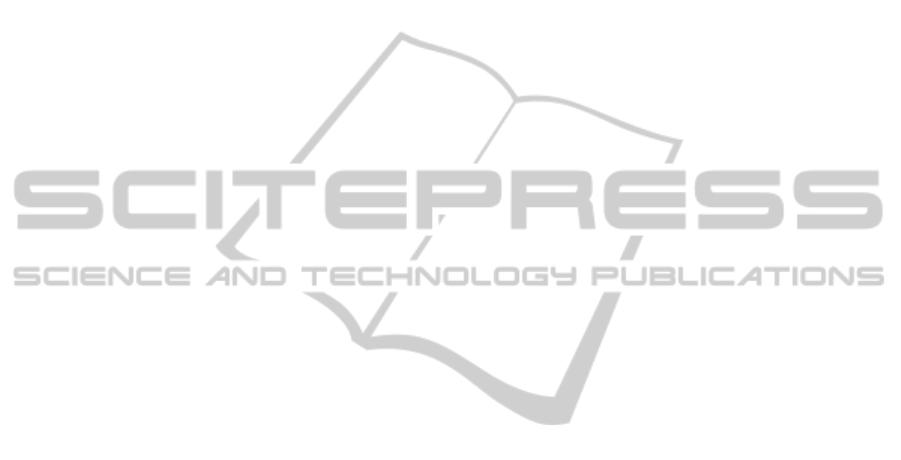
With delivery time of approximately three months,
Model*6.1 uses a total of 91 workers meaning 8.3%
above the number of workers specified by the
company. Although more workers are used in
simulation, this value is according to the company’s
expectation for the model’s performance without
considering resource flexibility.
4 CONCLUSIONS
The proposed model allowed the analysis of the
behaviour of the studied system. Although the model
represents all the production process with a
reasonable degree of detail, special emphasis was
given to workers allocation to tasks. Nevertheless it
is easy to change other parameters and test more
scenarios.
Individual production lines were studied and
analysed in greater detail by verifying worker and
resources utilization and completion time to ensure
they could be used for correct modelling of the
overall plant.
It is possible to establish that transport traveling
distance and priority logic have a significant
influence in the response of the model. But more
important, the model is very sensitive to changes in
worker capacity and worker distribution by the
several specialization profiles. This is due to the
demand of at least one worker to execute each task
from the productive process.
The model results agree with the data supplied
by the company for the individual production lines.
For the overall plant the results showed some
discrepancies, but the sensitivity analysis allowed an
identification of the most significant problems of the
original model version. By redesigning some of the
model assumptions and logic that were originally not
part of the supplied data, it was possible to improve
the model results to within 8.3% of error relative to
the real data values. This result was considered as
acceptable by the industrial partner under the
assumptions that were considered.
ACKNOWLEDGEMENTS
This work was supported by FCT, through IDMEC,
under LAETA Pest-OE/EME/LA0022 and partially
supported by the project R046, IDMEC.
REFERENCES
Altiok, T. & Melamed, B., 2007. Simulation Modeling and
Analysis with Arena. United States of America:
Elsevier Inc.
Banks, J., II, J. S. C., Nelson, B. L. & Nicol, D. M., Fourth
Edition. Discrete-Event System Simulation. New
Jersey: PRENTICHEA L-L lN TERNATIONAL
SERIEINS lN DUSTRIAL AND SYSTEMENSG
INEERING.
Brito, S. d. S., 2014. CRESESB. [Online] Available at:
http://www.cresesb.cepel.br/content.php?cid=tutorial_
eolica.
Chance, F., Robinson, J. & Fowler, J., 1996. Supporting
manufacturing with simulation: model design,
development, and deployment. San Diego, CA., IEEE.
Hemami, A., 2012. Wind Turbine Technology. 5 Maxwell
Drive, Clifton Park, NY 12065-2919, USA: Cengage
Learning.
Kelton, W. D., Smith, J. S. & Sturrock, D. T., 2013. Simio
and Simulation: Modeling, Analysis, Applications -
Third Edition. s.l.:Simio LLC.
Law, A. M. & Kelton, W. D., 2000. Simulation Modeling
and Analisys, Third Edition. s.l.:McGraw-Hill Book
Company.
McHaney, R., 2009. Understanding Computer Simulation.
s.l.:Roger McHaney & Ventus Publishing ApS.
Redes Energéticas Nacionais, R., 2013. Energia Eólica em
Portugal 2012.
TEGOPI, n.d. [Online] Available at: http://www.tegopi.pt/
?mod=pdinamicas_pag&id=2&_item=1.
SIMULTECH2014-4thInternationalConferenceonSimulationandModelingMethodologies,Technologiesand
Applications
732