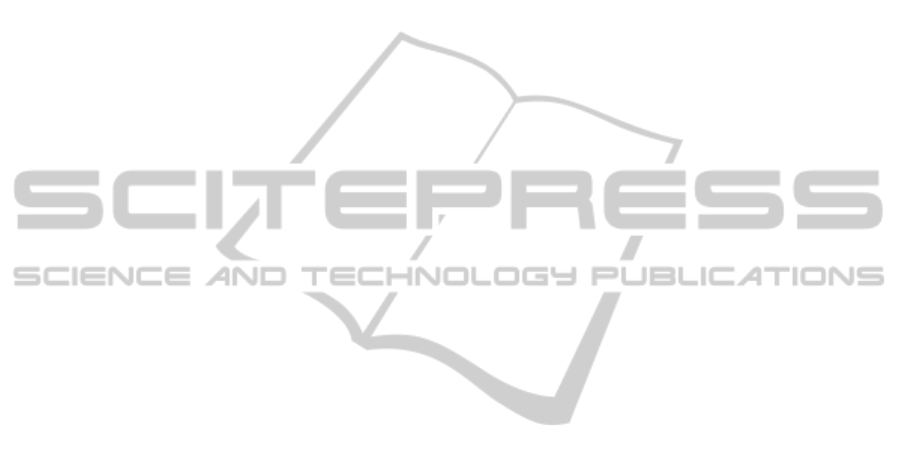
ACKNOWLEDGEMENT
This research was supported by Basic Science Re-
search Program through the National Research Foun-
dation of Korea(NRF) funded by the Ministry of
Education(NRF-2013R1A1A4A01012624).
REFERENCES
Balachandran, G. and Barnett, R. (2006). A 110 na volt-
age regulator system with dynamic bandwidth boost-
ing for rfid systems. Solid-State Circuits, IEEE Jour-
nal of, 41(9):2019–2028.
Ballan, H., Declercq, M., and Krummenacher, F. (1994).
Design and optimization of high voltage analog and
digital circuits built in a standard 5v cmos technology.
In IEEE Custom Integrated circuits Conference, pages
574–577.
Cha, H. K., Park, W. T., and Je, M. (2012). A cmos
rectifier with a cross-coupled latched comparator for
wireless power transfer in biomedical applications.
IEEE Transactions on Circuits and Systems-ll:Briefs,
59(7):409–413.
Chen, M. and Rincon-Mora, G. (2006). Accurate, com-
pact, and power-efficient li-ion battery charger circuit.
Circuits and Systems II: Express Briefs, IEEE Trans-
actions on, 53(11):1180–1184.
Do Valle, B., Wentz, C., and Sarpeshkar, R. (2011). An
area and power-efficient analog li-ion battery charger
circuit. Biomedical Circuits and Systems, IEEE Trans-
actions on, 5(2):131–137.
Garimella, A., Furth, P. M., Surkanti, P. R., and Thota, N. R.
(2011). Current buffer compensation topologies for
ldos with improved transient performance. Analog In-
tegr Circ Sig Process, 73(1):131–142.
Guo, S. and Lee, H. (2009). An effiency-enhanced
cmos rectifier with unbalanced-biased comparators
for transcutaneous-powered high-current implants.
IEEE Journal of solid-State Circuits, 44(6):1796–
1804.
Huang, P., Lin, H., and Lin, Y. T. (2006). A simple sub-
threshold cmos voltage reference circuit with channel-
length modulation compensation. IEEE Transactions
on Circuits and Systems II: Express Briefs, 53(9):882–
885.
Lee, H. M. and Ghovanloo, M. (2011). An integrated
power-efficient active rectifier with offset-controlled
high speed comparators for inductively powered ap-
plications. IEEE Transactions on Circuits and Systems
I: Regular Papers, 58(8):1749–1760.
Li, P. and Bashirullah, R. (2007). A wireless power in-
terface for rechargeable battery operated medical im-
plants. Circuits and Systems II: Express Briefs, IEEE
Transactions on, 54(10):912–916.
Li, Y. T., Chang, C. H., Chen, J. J. J., Wang, C. C., and
Liang, C. K. (2005). Development of implantable
wireless biomicrosystem for measuring electrode-
tissue impedance. Journal of Medical and Biological
Engineering,, 25(3):99–105.
Li, Y. T., Peng, C. W., Chen, L. T., Lin, W. S., Chu,
C. H., and Chen, J. J. J. (2013). Application of
implantable wireless biomicrosystem for monitoring
nerve impedance of rat after sciatic nerve injury. IEEE
Transactions on Neural Systems and Rehabilitation
Engineering, 1(21):121–128.
Mandal, S. and Sarpeshkar, R. (2007). Low-power cmos
rectifier design for rfid applications. IEEE Trans-
actions on Circuits and Systems I: Regular Papers,
54(6):1177–1188.
Mouna¨ım, F. and Sawan, M. (2011). Integrated high-
voltage inductive power and data-recovery front end
dedicated to implantable devices. IEEE Transactions
on Bio-Medical Circuits and Systems, 5(3):283–291.
Mounaim, F. and Sawan, M. (2012). Toward a fully in-
tegrated neurostimulator with inductive power recov-
ery front-end. Biomedical Circuits and Systems, IEEE
Transactions on, 6(4):309–318.
Nakamoto, H., Yamazaki, D., Yamamoto, T., Kurata, H.,
Yamada, S., Mukaida, K., Ninomiya, T., Ohkawa, T.,
Masui, S., and Gotoh, K. (2007). A passive uhf rf ide-
tification cmos tag ic using ferroelectric ram in 0.35-
um technology. IEEE Journal of solid-State Circuits,
42(1):101–110.
Nicolson, S. and Phang, K. (2004). Step-up versus step-
down dc/dc converters for rf-powered systems. In
Circuits and Systems, 2004. ISCAS ’04. Proceedings
of the 2004 International Symposium on, volume 5,
pages V–900–V–903 Vol.5.
Rincon-Mora, G. A. and Gabriel, A. (2009). Analog IC
Design With Low-dropout Regulators. McGraw-Hill.
Su, C., Islam, S. K., Zhu, K., and Zuo, L. (2012). A high-
temperature, high-voltage, fast response linear voltage
regulator. Analog Integr Circ Sig Process, 72:405–
417.
Thil, M. A., Gerard, B., Jarvis, J. C., Vince, V., Veraart, C.,
Colin, I. M., and Delbeke, J. (2004). Tissue-electrode
interface changes in the first week after spiral cuff im-
plantation: Preliminary results. In Annual Conference
of the International FES Society.
Tomita, K., Shinoda, R., Kuroda, T., and Ishikuro, H.
(2012). 1-w 3.3 -16.3-v boosting wireless power trans-
fer circuits with vector summing power controller.
IEEE Journal of solid-State Circuits, 47(11):2576–
2585.
Wang, G., Liu, W., Sivaprakasam, M., and Kendir, G. A.
(2005). Design and analysis of an adaptive transcuta-
neous power telemetry for biomedical implants. IEEE
Transactions on Cicuits and Systems-1, 52(10):2109–
2117.
Zou, V. and T, L. (2012). Modeling of substrate leakage
currents in a high-voltage cmos rectifier. Analog In-
tegr Circ Sig Process, 71:231–236.
BIODEVICES2015-InternationalConferenceonBiomedicalElectronicsandDevices
22