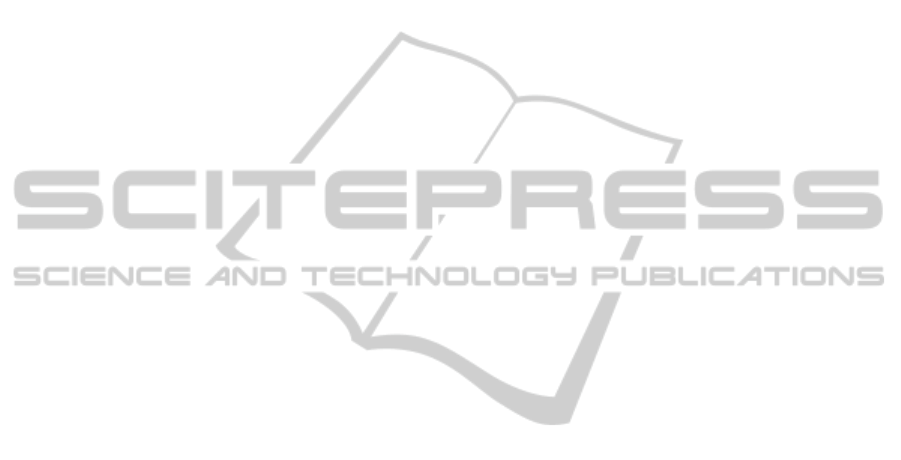
modes leak into the cladding producing the so-called
bending losses. Like explained in Padilla Michel, et
al (2012), when the refractive index of the coatings
is lower than that of the cladding, the leaky modes
go back to the core, due to refractive index
differences between layers; therefore, the fibre
seems to be insensitive to bending losses
independently of the E of the coating. However,
when the coating refractive index is higher than that
of the cladding, the leaky modes are trapped in the
coating producing a fibre which is very sensitive to
bending losses. In this condition, the E of the coating
plays an important role in the so-called bending
losses.
ACKNOWLEDGEMENTS
The authors would like to thank the AiF Projekt
GmbH (project number KF2014158NT3), the
Interne ZV-Cooperation Rome project, for the funds
granted, and Dr. Mohamad Zoheidi for providing the
fibre samples.
REFERENCES
Badar, A. H., Maclean, T. S. M., Ghafouri-Siraz, H.,
Gazey, B. K., 1991. Bent slab ray theory for power
distribution in core and cladding of bent multimode
optical fibres. IEE Proceedongs-J.
Badar, A. H., Maclean, T. S. M., 1991. Transition and
pure bending losses in multimode and single-mode
bent optical fibers. IEE Proceedings-J.
Boechat, A. A. P, Su, D., Hal, D. R., Jones, J. D. C., 1991.
Bending loss in large core multimode optical fiber
beam delivery systems. Appl. Opt.
Durana, G., Zubia, J., Arrue, J., Aldabaldetreku, G.,
Mateo, J., 2003. Dependence of bending losses on
cladding thickness in plastic optical fibers. Appl. Opt.
Faustini, L., Martini, G., 1997. Bend loss in single-mode
fibers. IEEE Journal of Lightwave Technology.
Gambling, W. A., Matsumura, H., Ragdale, C. M.,
Sammut, R. A., 1978. Measurement of radiation loss
in curved single-mode fibres. Microwaves optics and
acoustics.
Kovacevic, M. S., Nikezic, D., 2006. Influence of bending
on power distribution in step-index plastic optical
fibers and the calculation of bending loss. Appl. Opt.
Mitra, A., Kouzmina, I., Lopez, M., 2010. Thermal
stability of the CPC Fiber Coating System. Corning
Incorporated, WP4250.
Murakami, Y., Tsuchiya, H., 1978. Bending losses of
coated single-mode optical fibres. IEEE Journal of
Quantum Electronics.
Olson, H. G., 2002. Mechanical and Optical Behaviour of
A Novel Optical Fibre Crack Sensor and An
Interferometric Strain Sensor. PhD Thesis submitted
at the Massachusetts Institute of Technology.
Padilla Michel, Y., Zoheidi, M., Haynes, R., Olaya, J-C.,
2012. Applied stress on coated multimode optical
fibres: a different point of view to bending losses”.
Proc. SPIE 8450, Modern Technologies in Space- and
Ground-based Telescopes and Instrumentation II,
84503F.
Renner, H., 1992. Bending losses of coated single-mode
fibers: A simple approach. IEEE Journal of Lightwave
Technology.
Valiente, I., Vasallo, C., 1989. New formalism for bending
losses in coated single-mode optical fibres. Electronics
Letters.
Wang, Q., Farrell, G., Freir, T., 2005. Theoretical and
experimental investigations of macro-bend losses for
standard single mode fibers. Optics Express.
Wang, Q., Rajan, G., Wang, P., Farrell, G., 2007.
Polarization dependence of bend loss for a standard
single-mode fiber. Optics Express.
PHOTOPTICS2015-InternationalConferenceonPhotonics,OpticsandLaserTechnology
102