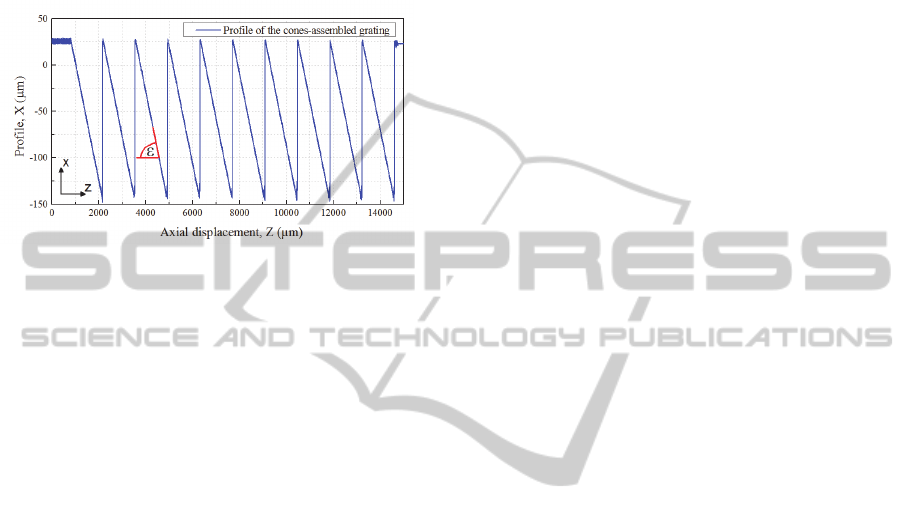
steps is 7.25°.
The average of the measured height is (196.2 ±
2.1 µm) for a theoretical height of 194 µm, the
average of the measured length is (1539.6 ± 4.1µm)
for a theoretical one of 1541.8 µm.
These results are very good for an initial
prototype.
Figure 15: Profile of the measured steps after fabrication.
7 CONCLUSIONS
This paper presents the design of an original fiber-
optic displacement sensor, which will be used to
measure the linear displacement of an axis
performing a helical movement.
First, the geometric model of the sensor principle
was presented in order to obtain the theoretical
geometric parameters. These parameters lead to the
optimal cones-assembled grating, masterpiece of the
long-range displacement measurement principle.
Then, a 10 steps grating prototype of the sensor
was fabricated using a high precision turning
machine with the help of a single crystal-diamond
tool on an aluminium alloy in order to obtain high
precision in the fabricated dimensions, as well as
high reflectivity which ensures good sensor
sensitivity and linearity.
The conical grating prototype was characterised
using Nanofocus
TM
µscan optical profilometer and
the measured parameters are close to the theoretical
ones.
In a near future, this grating will be used together
with two fiber-optic probes to measure on-line the
translation of an axis along several millimeters when
the measuring head of the spindle rotates at 360°
during the translation.
ACKNOWLEDGEMENTS
The Authors would like to thank Cetim (Centre
Technique des Industries Mécaniques) for the
support of this work.
The authors would like to thank B. Bosschaert,
N. Delias and P. E. Karcher, students in Univeristy
of technology of Compiègne, for their help in the
fabrication of the conical grating.
REFERENCES
T. Mukherjee, T.K. Bhattacharyaa, 2012. A Miniature,
High Sensitivity, Surface Micro-machined
Displacement Sensor with High Resolution. The 2012
IEEE/ASME International Conference on Advanced
Intelligent Mechatronics, Kaohsiung, Taiwan.
K.C. Fan, Z. F. Lai, P. Wu, Y. C. Chen, Y. Chen, G. Jager,
2007. A displacement spindle in a micro/nano level,
Measurement Science and Technology
doi :10.1088/0957-0233/18/6/S07.
A. D. Gaikwad, J. P. Gawande, A. K. Joshi, R. H. Chile,
2012. An Intensity-modulated optical fibre
displacement sensor with convex reflector,
International journal of advanced research in
electrical, electronics, and instrumentation
engineering, vol. 1, Issue 1.
Y.G. Lee, Y.Y. Kim, C.G. Kim, 2012. Fiber optic
displacement sensor with a large extendable
measurement range while maintaining equally high
sensitivity, linearity, and accuracy. Review of
Scientific Instruments 83, 045002(2012); doi:
10.1063/1.3698586.
Y. Zhao, P. Li, C. Wang , Z. Pu, 2000. A novel fiber-optic
sensor for small internal curved surface measurement.
Sensors and Actuators A, vol. 86, pp. 211-215.
S.S. Patil, A.D. Shaligram, 2011. Modeling and
experimental studies on retro-reflective fiber optic
micro-displacement sensor with variable geometrical
properties. Sensors and Actuators A, Vol. 172, pp.
428-433.
X. Bingshi, X. Wen , Y. Dong, 2008. A theoretical
analysis on parameters of fiber optic displacement
sensor. Proc. of SPIE, Vol. 7129, pp. 1-6.
F. E. Utou, J. Gryzagoridis, B. Sun, 2006. Parameters
affecting the performance of fiber optic displacement
sensors. Smart Mater. Struct. 15 (2006) S154–S157,
doi: 10.1088/0964-1726/15/1/025.
Y. Alayli, D. Wang, M. Bonis, 1998. Optical fiber
profilometer with submicronic accuracy. Proc. SPIE,
3509.
P.M.B.S. Girão, O.A. Postolache, J.A.B. Faria, J.M.C.D.
Pereira, 2001. An overview and a contribution to the
optical measurement of linear displacement, IEEE
Sens. J. pp. 322–331.
C. Prelle, F. Lamarque, P. Revel, 2006. Reflective optical
sensor for long-range and high-resolution
displacements. Sensors and Actuators A, vol. 127.
A. Khiat, F. Lamarque, C. Prelle, Ph. Pouille, M. Leester-
Schadel and S. Büttgenbach, 2010. Two-dimension
fiber optic sensor for high-resolution and long
PHOTOPTICS2015-InternationalConferenceonPhotonics,OpticsandLaserTechnology
154