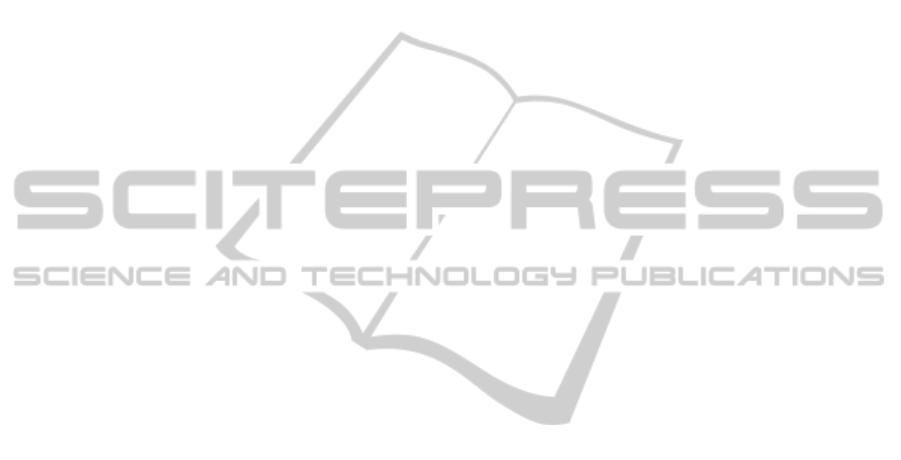
quantitative-filling quantity has much influence on
the filling accuracy, and reduce the
quantitative-filling quantity can significantly
improve the filling accuracy. The quantitative-filling
velocity has smaller influence on the filling accuracy,
but it can adjust the peak of filling error value.
Therefore reduce the quantitative-filling quantity can
reduce the maximum of filling error, so as to
improve the filling accuracy.
5 CONCLUSIONS
In terms of rocket propellant filling, this paper
analyzes the factors that affect the accuracy of the
propellant filling in the filling system of the
spaceflight launch site. It calculates the error value
of filling quantity caused by the different factors,
and carries through numerical calculation and
analysis for the actual filling accuracy of rocket
propellant. It is helpful to optimize filling model and
filling process, and provides theoretical basis and
data support for the research of improving the filling
accuracy. Through numerical analysis we can get
that the equipment performance has much influence
on the filling accuracy, in the case of definite
equipment performance, reduce the
quantitative-filling quantity and quantitative-filling
velocity can also improve the filling accuracy.
However, it does not consider the influence of
the gas-liquid two-phase flow and the propellant
temperature rise when calculating the actual filling
accuracy. The next research direction is to get the
error value of filling quantity caused by the
gas-liquid two-phase flow and the propellant
temperature rise through simulation calculation, to
perfect the factors that affect the accuracy of
propellant filling, put forward more effective
targeted measures, so as to further improve the
filling accuracy of rocket propellant.
REFERENCES
Deng Y, Qin G, Wang M, et al. Study on performance
degradation simulation and evaluation method for
pneumatic ball valve of Propellant Filling System[C].
Quality, Reliability, Risk, Maintenance, and Safety
Engineering (ICQR2MSE), 2012 International
Conference on. IEEE, 2012: 144-147.
Zhuang Ke. Design and implementation of the
conventional propellant filling factor range application
system. National University of Defense Technology,
2005.
Xiang Youhuan, Shi Jinfeng, Li Liqun, et al. Accuracy
Analysis on Measuring Model of Rocket Propellant
Filling Based on Weight Measurement[C]. IEEE
International Conference ICSPCC2014, 2014.8:
281-286.
Ma Jian, Tong Fei, Chen Zu-kui. Analysis on deviation
and measuring precision of tank volume[J]. Journal of
Rocket Propulsion. 2013 (1): 41-45.
Yang Zhi-qiang, Zhang Hong-jian, Huang Yong-mei.
Research on data value simulation of fluid field
characteristic of vortex flowmeter[J]. Process
Automation Instrumentation. 2004, 25(5):10-13.
Yan Xiao-qing, Li Zi-ran, Zhou Jin. Calculation of
bookbinding parameters and integrating method of the
software of liquid propellant utilizing system. Jourmal
of National University of Defense Technology. 2004,
26(6): 79-81.
Pan Yong-cheng, Wang Yong, Xie Yu-dong. Analysis of
Inner Flow Field Characteristics of a Control Valve
Based on CFD[J]. Machine Tool & Hydraulics. Vol.39
No.1 Jan.2011:5-7.
Ma Xiaolin, Chen Guoding. Dynamics and Leakage
Analysis of Padded Finger Seal Based on Equivalent
Model[J]. Acta Aeronautica et Astronautica Sinica.
Vol.29 No.5 Sept.2008:1356-1363.
Dong Yu-hua, Zhou Jing-en. Numerical Calculation of
Gas Leakage Rate in the Long-transport Pipeline. Oil
& Gas Storage and Transportation. Vol.21 No.8
2002:11-15.
Zou W, Yu K, Wan X. Research on the gas-leakage rate of
unsteady ventilated supercavity[J]. Journal of
Hydrodynamics, Ser. B, 2010, 22(5): 778-783.
Beirami M K, Nabavi S V, Chamani M R. Free overfall in
channels with different cross sections and sub-critical
flow[J]. Iranian Journal of Science & Technology,
Transaction B, Engineering, 2006, 30(B1).
Boonen E, Van Puyvelde P, Moldenaers P. Droplet
dynamics in sub-critical complex flows[J]. Rheologica
acta, 2009, 48(4): 359-371.
Cazauran X, Birembaut Y, Hahn R, et al. Gas Leakage
Correlation[C]//ASME 2009 Pressure Vessels and
Piping Conference. American Society of Mechanical
Engineers, 2009: 243-249.
Zhang S, Liu W, Zhang Y, et al. Gas leakage monitoring
with scanned-wavelength direct absorption
spectroscopy[J]. Chinese Optics Letters, 2010, 8(5):
443-446.
Ben-Mansour R, Habib M A, Khalifa A, et al.
Computational fluid dynamic simulation of small
leaks in water pipelines for direct leak pressure
transduction[J]. Computers & Fluids, 2012, 57:
110-123.
FillingAccuracyAnalysisoftheRocketPropellantbasedontheFlowmeterMeasuringModel
187