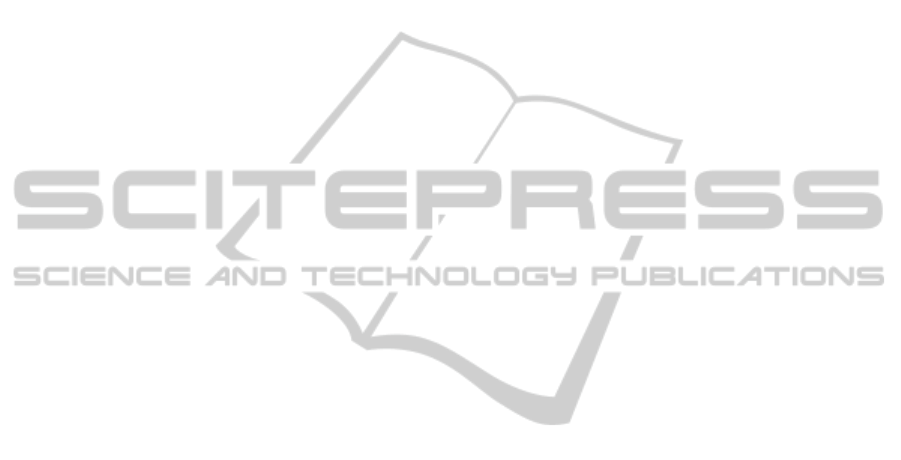
metal feed to the BOF is synchronous and without
wait. Also, timely arrival of hot metal from the iron-
making-unit needs to be ensured.
In the steel-melting-shop unit, the liquid steel
from the BOF is taken to the Caster where the liquid
steel is molded via secondary refining units
comprising of Ladle Refining Furnace (LRF) and/or
Vacuum Degassing (VD) units. The BOF should be
synchronized with the Casters such that the heat
sequences for different grades are maintained while
maximizing the utilization of the equipment to
ensure the highest throughput from hot-metal
charging to casting. It is always preferred to have
uninterrupted sequence during continuous casting to
achieve higher production and yield.
Our study was based on an integrated steel plant
having two BOFs, with one working and one
standby mode, one LRF, one Vacuum Degassing
unit and one three-strand Caster (operated with two
strands). The existing operations needed to be
studied and analyzed in detail and additional
facilities/ improvements in the system needed to be
proposed to utilize the Caster, LRF and BOF fully
and thereby increasing the overall throughput of the
system. It was also needed to suggest the number of
hot metal ladles and steel ladles in active circulation
required for the suggested production.
2 THE PROCESS AND
OPERATIONS
Hot metal in the Blast Furnace (BF) is cast as per BF
cast schedule into open top ladles placed in transfer
cars on railway tracks. The ladle transfer car is
carried to SMS or PIG Casting Machine (PCM) by
captive locomotive depending on the readiness of
the converter to accept the hot metal.
At SMS the full ladle is picked up from the
transfer car by an overhead crane and carried to the
sampling point. In case an empty ladle is ready for
return to BF, the full ladle is picked and kept on the
pit, the empty ladle placed on the transfer car and
then the full ladle is picked up again by the overhead
crane. Once the sampling is complete, the ladle is
carried to the BOF. In the mean time scrap is
charged to the BOF by scrap charging crane. On
completion, the hot metal is charged to the BOF and
blowing starts. Near the end of the blowing cycle,
temperature is measured and samples are taken for
analysis. After pouring of the hot metal to the BOF,
the ladle is carried to the pit by overhead crane for
sending back to the BF.
Steel ladle on steel transfer car gets under the
BOF vessel and steel is tapped into the ladle through
the tap hole. Once tapping is complete, slag pot car
gets under the BOF vessel and slag is poured into
the slag pot through the BOF vessel mouth.
After processing of 8 heats in the BOF,
maintenance operations, also known as dozing and
mouth jam cleaning are carried out. After 15 heats of
BOF operation the maintenance operation of tap
hole changing is performed. And after 75 heats,
other maintenance works on the vessel are carried
out. The numbers are varied depending on the status
and completion of the casting sequence.
After tapping of steel into the steel ladle, it is
transported to the ladle refining aisle by the ladle
transfer car, picked up by overhead crane and placed
on the LRF transfer car. The purging lines are fixed
and the transfer car goes into the LRF. The steel is
further refined in the LRF by adding alloying
materials to give it special properties as required.
Once the LRF processing is complete, the ladle
transfer car brings out the ladle and the purging lines
are removed. The ladle is also moved to the VD unit
by overhead crane, and further treatment done.
The ladle is transported to the caster turret from
the LRF or VD by overhead cranes. The ladle sits in
a rotating turret at the casting machine. One ladle is
in the 'on-cast' position (feeding the casting
machine) while the other is made ready in the 'off-
cast' position, and is switched to the casting position
when the previous ladle is empty. Once casting of
one ladle is over, and the turret rotates, the empty
ladle is transported from the turret to the slag
dumping area and slag is dumped. After slag
dumping, the ladles are sent to the ladle preparation
area and placed back on the transfer car for the next
tapping from the BOF.
3 OVERALL THROUGHPUT
IMPROVEMENT
The process of steelmaking and casting, from BOF
to Caster, may be categorized into three distinct
stages, viz. primary steelmaking, secondary
steelmaking and casting. Primary steelmaking is
concerned with the production of liquid steel, which
is subsequently refined in terms of both its
composition and its cleanliness through a host of
secondary steelmaking processes. Molten steel with
desired composition, cleanliness and temperature is
finally transformed into solid products through
continuous casting. Figure 2 shows the categories of
the steelmaking process.
SIMULTECH2015-5thInternationalConferenceonSimulationandModelingMethodologies,Technologiesand
Applications
112