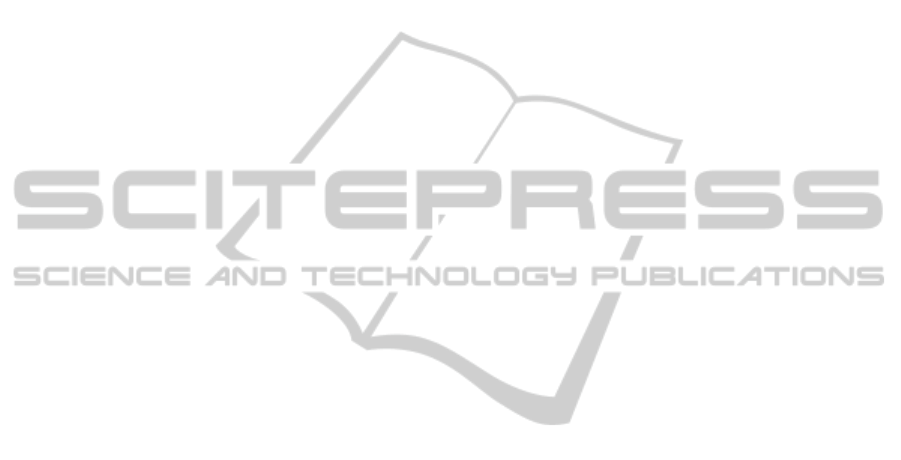
the maximum charging power (80W) was only
achieved when the ultracapacitors module voltage
reached 5.7V. The ultracapacitors module charging
was completed when its voltage reached 15.5V.
After that, the lead-acid battery charging proceeded.
A small disturbance is visible in the voltage and
current waveforms at the output of the energetically
optimized voltage regulator, considering a power of
12.5W. This is due to the starting of the step-up
converter. Until then, only the ultracapacitors
module was providing power to the load. Observing
the voltage and current waveforms in the
ultracapacitors module, it is possible to conclude
that the average current value tends to increase due
to the decreasing in the average voltage value, as
expected, because only then is it possible to maintain
a constant output power.
Regarding the practical implementation of the
two previous systems, printed circuit boards were
implemented using the Eagle Cadsoft 6.4 and digital
PI controllers were developed with Atmel Studio 6.1
and microcontrollers Atmel ATmega 328P.
The output voltage regulator is the last stage of
the power supply system. It is responsible for
supplying the suitable average voltage to the motors
of the mobile robot platform. Autonomy tests were
made and it was found that, if the mobile robot
platform is placed on a flat and horizontal surface at
maximum speed (about 60 cm/s), the average
autonomy is about 23 minutes and 13 seconds using
only the available energy in ultracapacitors module.
From that moment, which corresponded to an
ultracapacitors module voltage of 2.48V, the system
started to use the energy available in both sources
and achieved an autonomy of, approximately, 9
hours and 40 minutes. It was verified that the system
was able to extract almost all of the energy stored in
the ultracapacitors module, taking its voltage almost
to 0V. Regarding the practical implementation of
this last system, a printed circuit board was also
developed through the Eagle Cadsoft 6.4, and a
digital PID controller was implemented using the
Atmel software Studio 6.1 and the microcontroller
Atmel ATmega 1284P.
As a future development, it is suggested to
modify the circuits and the control systems in order
to allow energy interchange between the
ultracapacitors module and the batteries. This will
improve energy efficiency in the event that only a
fraction of the energy stored in the ultracapacitors
module is used.
ACKNOWLEDGEMENTS
This work has been supported by FCT – Fundação
para a Ciência e Tecnologia in the scope of the
project: PEst-UID/CEC/00319/2013.
REFERENCES
Arantes, C., Sepúlveda, J., Esteves, J., Costa, H., Soares,
F., Using Ultracapacitors as Energy-storing Devices
on a Mobile Robot Platform Power System for Ultra-
fast Charging; ICINCO 2014, 11th International
Conference on Informatics in Control, Automation and
Robotics, 2014, Page(s): 156 – 164, ISBN 978-989-
758-040-6. DOI: 10.5220/0005061801560164.
Awerbuch, J. J., Sullivan, C. R., Filter-based Power
Splitting in Ultracapacitor-Battery Hybrids for
Vehicular Applications; COMPEL 2010, Control and
Modeling for Power Electronics, 2010, Pages(s): 1 –
8. DOI: 10.1109/COMPEL.2010.5562429.
Bernholc, J., Ranjan, V., Zheng, X. H., Jiang, J., Lu, W.,
Abtew, T. A., Boguslawski, P., Nardelli, M. B.,
Meunier, V., Properties of High-Performance
Capacitor Materials and Nanoscale Electronic
Devices; HPCMP-UGC 2010, High Performance
Computing Modernization Program Users Group
Conference, 2010, Page(s): 195 – 200. DOI:
10.1109/HPCMP-UGC.2010.76.
Haifeng, Dai and Xueyu, Chang; A Study on Lead Acid
Battery and Ultra-capacitor Hybrid Energy Storage
System for Hybrid City Bus; ICOIP 2010,
International Conference on Optoelectronics and
Image Processing, 2010, Page(s): 154 – 159. DOI:
10.1109/ICOIP.2010.321.
Kularatna, N., Patel, A., Supercapacitors for Energy
Mangement in Autonomous Sensor Nodes; WAC,
World Automation Congress, 2014, Page(s): 604 –
609. DOI: 10.1109/WAC.2014.6936064.
Monteiro, J., Garrido, N., Fonseca, R., Efficient
Supercapacitor Energy Usage in Mobile Phones; ICCE
2011, 2011 International Conference on Consumer
Electronics – Berlin, 2011, Pages(s): 318 – 321. DOI:
10.1109/ICCE-Berlin.2011.6031796.
Muffoletto, D., Mandris, C., Olabisi, S., Burke, K.,
Zirnheld, J., Moore, H., Singh, H., Design and
Analysis of a Smart Power Management System for
Ultracapacitor-Powered Robotic Platform; IPMHVC,
Power Modulator and High Voltage Conference,
2010, Page(s): 643 – 646. DOI:
10.1109/IPMHVC.2010.5958441.
Musat, A. M., Carp, M., Borza, P., Musat, R., Sojref, D.,
Hybrid Storage Systems and Dynamic Adapting
Topologies for Vehiche Applications; OPTIM 2012,
2012 13th International Conference on Optimization
of Electrical and Electronic Equipment, 2012, Page(s):
1842 – 1566. DOI: 10.1109/OPTIM.2012.6231910.
Niemoeller, B. A. and Krein, P. T., Battery-Ultracapacitor
ICINCO2015-12thInternationalConferenceonInformaticsinControl,AutomationandRobotics
162