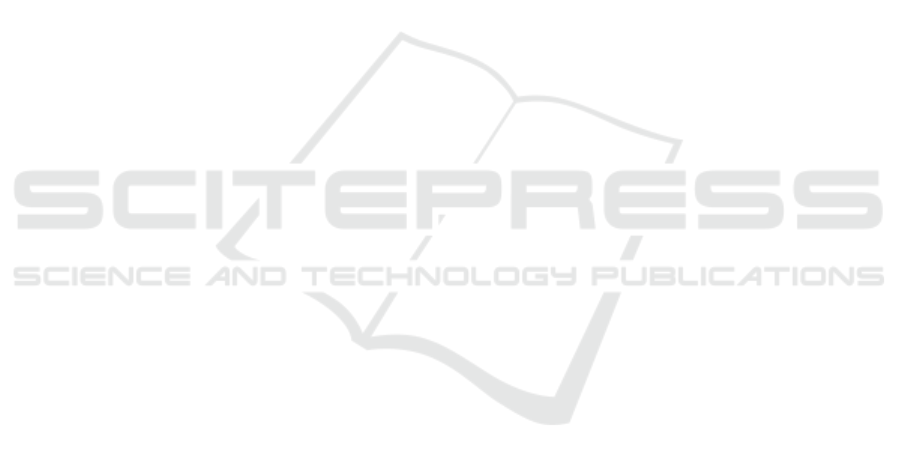
The remainder of this article is organized as fol-
lows: After the introduction and related works, we
present our overall approach as part of our ongoing
research. Afterwards, the field studies and the derived
classification method are described. This contribution
closes with evaluation results of the proposed method.
2 RELATED WORK
In the field of logistics, different statistical and
simulation-based approaches have been investigated
during the last years to understand the characteris-
tics of manual process steps and to identify the fac-
tors that affect the time consumption of these steps.
For instance, in (Krengel et al., 2010) the process
time is modeled with help of probability distributions.
Further works in this area address the measurement
of person specific performance metrics (Siepenkort,
2013) or the identification of factors that have impact
on the performance of a worker (Stinson et al., 2014).
A non-statistical approach is presented in
(G
¨
unthner and Steghafner, 2011) containing a
virtual-reality-based planing tool which utilizes a
simulation model of the planned system to estimate
order picking time. For that, a head-mounted display,
gloves with markers and a modified treadmill are
used. In this paper, we are looking at the problem
from a different perspective and try to gain insights
into the order picking process by reducing the effort
of measurements in existing systems. Consequently,
we want to automate the measurement procedure and
parts of the process analysis like the determination of
the travel time. Thus, we investigate the possibilities
of activity recognition and motion classification like
being already employed in other domains, e. g. in
medical science, sports or entertainment.
In medical science, sensor-based analysis of hu-
man movements and behavior is deployed especially
for the detection and treatment of diseases which im-
pact on the musculoskeletal system. This includes pa-
tients with strokes or neurodegenerations like Parkin-
son’s disease (Bidargaddi et al., 2007), (Dobkin et al.,
2011), (Zhu et al., 2012).
Another field of research related to the medical
context is Ambient Assisted Living (AAL). AAL aims
at the adaption of ICT-technologies helping elderly
people living by themselves performing their daily
activities and increasing their quality of life (Bravo
et al., 2012, p.34). Therefore, the environment and
the people are equipped with technical artifacts which
among others detect anomalies, e. g. medical emer-
gencies (Jeong et al., 2014), (Fern
´
andez-Llatas et al.,
2013). The recognition of behavior and activities in
AAL is summarized by the term Activities of Daily
Life Monitoring (Zouba et al., 2008). As the focus of
this application lies on the detection of anomalies, the
deployed methodologies are not promising candidates
for our goal, as we want to particularly understand the
complete order picking process.
Many popular applications for motion classifi-
cation and activity recognition were developed for
sports and fitness. In this case consumer electron-
ics devices like smartphones and wearables or even
clothes which are equipped with inertial sensors are
used to quantify the physical activities of a sub-
ject. This allows to monitor the health and train-
ing state (Long et al., 2009), (Toney et al., 2006),
(Linz et al., 2006). Especially for professional ath-
letes, sport-specific solutions are available to collect
this data from daily training (Auvinet et al., 2002),
(B
¨
achlin et al., 2008), (Hardegger et al., 2015).
Within the production domain, different activity
recognition approaches have been put forward to ana-
lyze manual manufacturing processes. For instance,
(Hartmann, 2011) introduces a concept to measure
and dissect the behavior of workers executing assem-
bling tasks. Optical markers, cameras, IMUs and a
multi-layer activity recognition are proposed there. A
different approach can be found in (Koskim
¨
aki et al.,
2013) and (Siirtola, 2015). Among others, the authors
address the distinction of different tools the worker
utilizes within the manufacturing process. While all
mentioned works in this field separate data acqui-
sition and data evaluation, (Stiefmeier, 2008) intro-
duces an approach supporting activity recognition in
real-time with the help of a string matching method.
In summary, in production different activity recogni-
tion and motion classification approaches exist which
address the special requirements of manual manu-
facturing tasks. As those tasks usually occur in a
bounded area and mostly consist of upper limb move-
ments, the existing methods do not meet the special
requirements of the order picking process which in-
cludes many context-dependent motions and activities
of the whole body (e. g. driving, walking).
3 APPROACH
To recognize human activities and motions in order
picking, different levels of detail can be identified.
These range from structured motions which are re-
peated periodically like walking or driving to more
complex activities like packing. Especially the pack-
ing of orders consists of multiple sub tasks: setting
up a shipping box, filling it, applying a shipping label
and finally closing the box.
Motion Classification for Analyzing the Order Picking Process using Mobile Sensors - General Concepts, Case Studies and Empirical
Evaluation
707