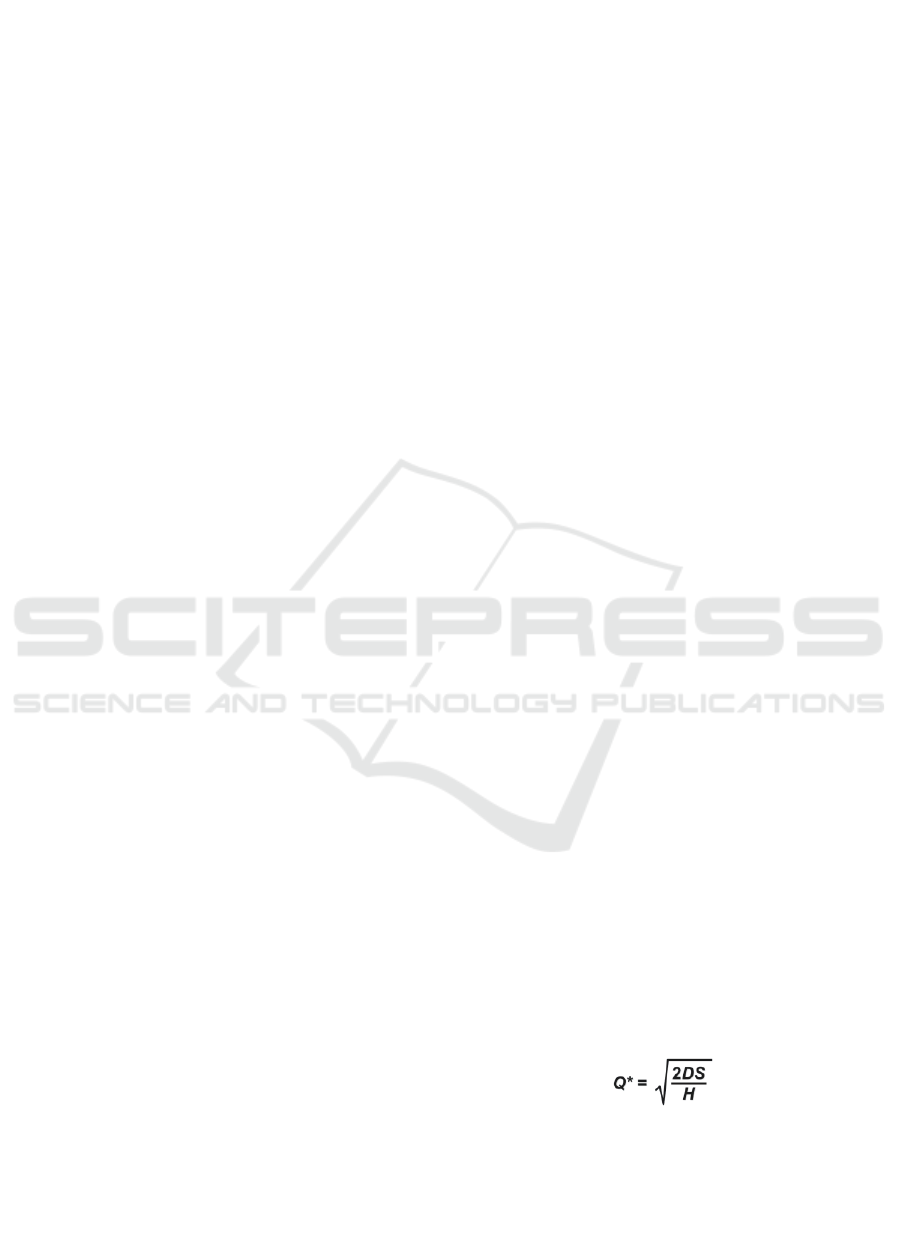
2 LITERATURE REVIEW
The stock of material on inventory management is
used to facilitate production or meet customer
demand. The main reason companies should have
inventory are; protecting from uncertainty, enabling
economical purchase and production, masking
changes in anticipated demand and supply,
providing transit (Schroeder, 2011). The external
customer demand also has to be an orientation for
organization to keep a stock of items (Russell,
2006). The purpose of inventory management in
general is to determine the amount of inventory to be
stored, how much and when to order, and to get a
balance between inventory investment and service to
consumers. Inventory management has two main
approaches, base on the customer demand which
consists of dependent and independent. On
independent demand, the method used is Economic
Order Quantity, and others. As for the dependent
demand techniques used are Material Requirement
Planning (Heizer, 2014).
2.1 Material Requirement Planning
The main purpose of the MRP is to keep inventory
levels as low as possible. The MRP achieves it by
determining when a component is needed and
scheduling it to be available on time. To minimize
inventory cost, the company also can use JIT
system, but it is more suitable for small lot size and
large variety production, while MRP for large lot
size and small variety production (Hui Wang, 2017).
To use the MRP method effectively, the required
inputs are: Master Production Schedule (MPS), Bill
of Materials (BOM), inventory records, purchase
orders, and Lead Time are known. The MRP system
parameter is one of the most important activities for
the perfect system functioning. They should take
into consideration some reality and circumstances of
companies environment. For instance, supplier
deliveries are not always on time (fuzzy lead time),
so the safety stock option can be adopted as the
included parameter (Santin, 2015). In the case of
MRP problem with fuzzy lead times, analysis can
use a fuzzy multi-objective integer linear
programing (Madronero, 2015). The accuracy of the
MRP input is the main factors of MRP system
success. Once all inputs are available, the next step
is to determine gross demand and net requirement of
material. The difference of them lies in the
calculation of inventory stocks of the company.
Most of MRP outputs needed by the company
are; a) MRP report per period, b) MRP report per
day, c) Report of the plan of reservation, this report
contains Planned Order Releases and Planned Order
Receipt, d) Purchase Recommendation, e) Exception
report, is an additional report for raw materials that
have special treatment in the ordering process
(Heizer, 2014, Russell, 2006).
The MRP process consists of several steps;
netting, lot measurement, and offsetting as a
determination of order quantity and time by
considering process time. To achieve cycle time
reduction, it can use a smaller lot size, a reduction in
lot size transferred directly into lower raw process
times (Ying-MeiTu, 2017). MRP methods produce
schedule of production and the need for material
which required Lot Sizing technique. Determining
lot sizes in production areas is an essential task of
production planning and control (Schmidt, 2015).
There are various kinds of lot sizing techniques,
including: Lot for Lot (LFL), Economic Order
Quantity (EOQ), and Periodic Order Quantity
(POQ).
2.1.1 Lot for Lot (LFL)
Lot for Lot (LFL) is a technique that produces the
right amount of raw materials to meet the plans that
have been made. The LFL technique is in line with
the objectives of the MRP to meet the needs of
dependent demand. Therefore, the MRP system
must produce goods as required (Heizer, 2014).
2.1.2 Economic Order Quantity (EOQ)
The objective of EOQ is to minimize the amount of
ordering and storage costs. This technique is one of
the most commonly used and easy-to-use based on
the following assumptions: a) demand is known,
constant, and independent, b) lead time is known
and constant, c) receipt of inventory is instantaneous
and complete, d) quantity discounts are not possible,
e) only variable costs are setup and holding, f) stock
outs can be completely avoided (Heizer, 2014).
Although EOQ is more suitable for use when
demand is relatively constant and independent, it can
be used in known queries by finding the average
requests that appear within a year. The formula used
is:
Q* = Optimal number of pieces per order (EOQ)
D = Annual demand in units for the inventory item
S = Setup or ordering cost for each order
H = Holding or carrying cost per unit per year
Analysis of Material Requirement Planning (MRP) Implementation on The Company
141