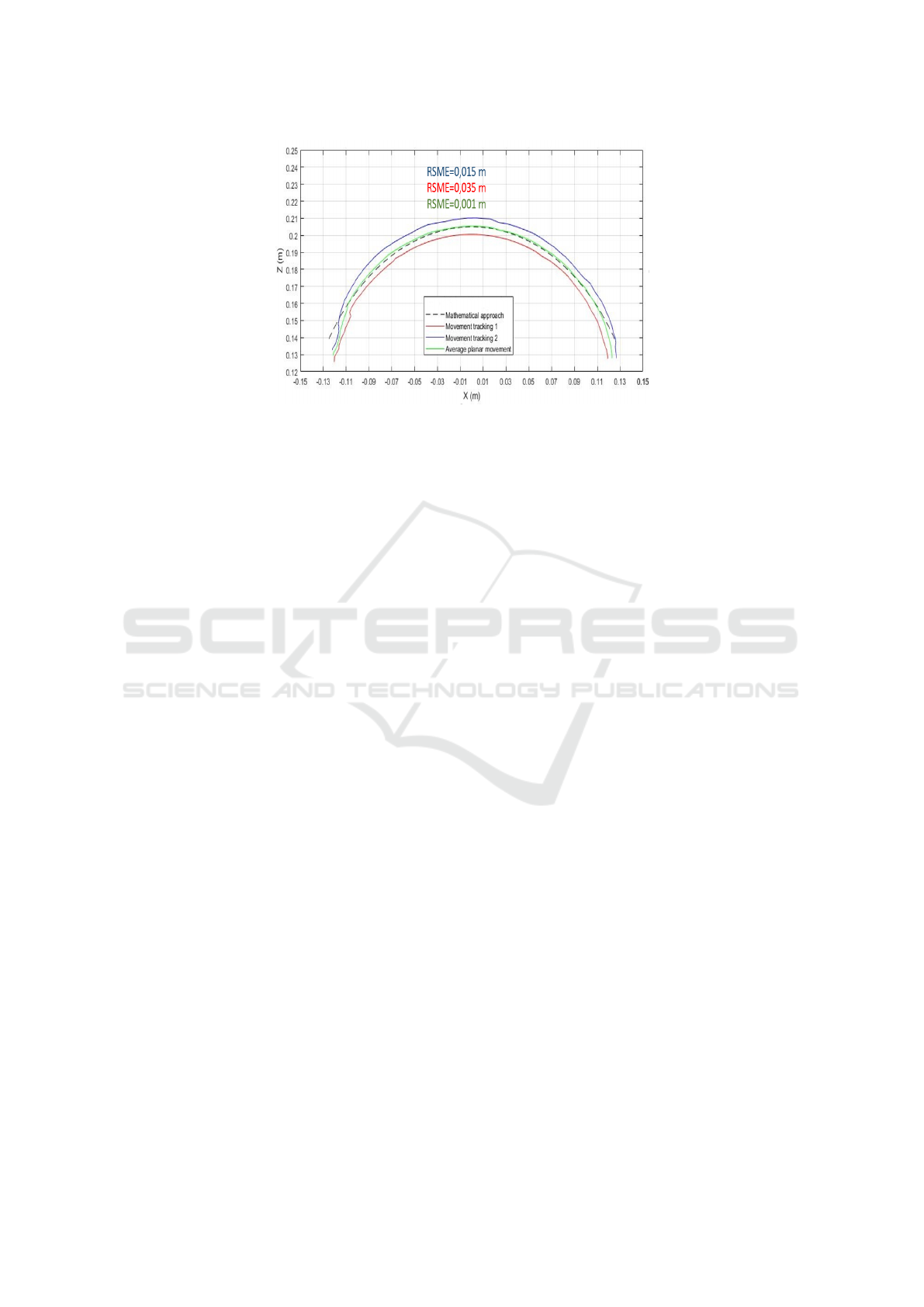
Figure 9: Comparison between different movements, their average and the calculated trajectory.
REFERENCES
Burgner, J., Rucker, D. C., Gilbert, H. B., Swaney, P. J.,
Russell, P. T., Weaver, K. D., and Webster, R. J.
(2014). A telerobotic system for transnasal sur-
gery. IEEE/ASME Transactions on Mechatronics,
19(3):996–1006.
Burgner-Kahrs, J., Rucker, D. C., and Choset, H. (2015).
Continuum Robots for Medical Applications: A Sur-
vey. IEEE Transactions on Robotics, 31(6):1261–
1280.
Chirikjian, G. S. and Burdick, J. W. (1995a). Kinematically
Optimal Hyper-Redundant Manipulator Configurati-
ons. IEEE Transactions on Robotics and Automation,
11(6):794–806.
Chirikjian, G. S. and Burdick, J. W. (1995b). The Kine-
matics of Hyper-Redundant Robot Locomotion. IEEE
Transactions on Robotics and Automation, 11(6):781–
793.
Crespi, A., Badertscher, A., Guignard, A., and Ijspeert, A. J.
(2005). AmphiBot I: An amphibious snake-like robot.
Robotics and Autonomous Systems, 50(4):163–175.
DHB (2013). Differential Geometry. Reading, (4):0.
Hannan, M. W. and Walker, I. D. (2003). Kinematics and
the implementation of an elephant’s trunk manipulator
and other continuum style robots. Journal of Robotic
Systems, 20(2):45–63.
Hirose, S. (1995). Biologically Inspired Robots: Snake-
Like Locomotors and Manipulators. Applied Mecha-
nics Reviews, 48(3):B27–B27.
Jones, B. A., McMahan, W., and Walker, I. D. (2006).
Practical Kinematics for Real-Time Implimentation of
Continuum Robots. IEEE International Conference
on Robotics and Automation, pages 1840–1847.
Jones, B. A. and Walker, I. D. (2006). Kinematics for multi-
section continuum robots. IEEE Transactions on Ro-
botics, 22(1):43–55.
Laschi, C., Cianchetti, M., Mazzolai, B., Margheri, L., Fol-
lador, M., and Dario, P. (2012). Soft robot arm inspi-
red by the octopus. Advanced Robotics, 26(7):709–
727.
Li, Z., Ren, H., Chiu, P. W. Y., Du, R., and Yu, H. (2016).
A novel constrained wire-driven flexible mechanism
and its kinematic analysis. Mechanism and Machine
Theory, 95:59–75.
Li, Z., Wu, L., Ren, H., and Yu, H. (2017). Kinematic com-
parison of surgical tendon-driven manipulators and
concentric tube manipulators. Mechanism and Ma-
chine Theory, 107(September 2016):148–165.
Liu, S., Yang, Z., Zhu, Z., Han, L., Zhu, X., and Xu, K.
(2016). Development of a dexterous continuum ma-
nipulator for exploration and inspection in confined
spaces. Industrial Robot: An International Journal,
43(3):284–295.
Ma, S., Hirose, S., and Yoshinada, H. (1994). Develop-
ment of a hyper-redundant multijoint manipulator for
maintenance of nuclear reactors. Advanced Robotics,
9(3):281–300.
Mahl, T., Hildebrandt, A., and Sawodny, O. (2014). A Vari-
able Curvature Continuum Kinematics for Kinematic
Control of the Bionic Handling Assistant. 30(4):1–15.
McMahan, W., Chitrakaran, V., Csencsits, M., Dawson, D.,
Walker, I. D., Jones, B., Pritts, M., Dienno, D., Gris-
som, M., and Rahn, C. D. (2006). Field trials and tes-
ting of the OcotArm continuum manipulator. Procee-
dings of the 2006 IEEE international conference on
robotics and automation (ICRA), (May):2336–2341.
Meng, G. Z., Yuan, G. M., Liu, Z., and Zhang, J. (2013).
Forward and Inverse Kinematic of Continuum Robot
for Search and Rescue. Advanced Materials Research,
712-715:2290–2295.
Pires, N. (2007). Robot Manipulators and Control Systems.
Industrial Robots Programming. Building Applicati-
ons for the Factories of the Future.
Robotics OC (2016). LaserPipe Remote in-bore laser wel-
ding of industrial pipelines.
Tiefeng, S., Libin, Z., Mingyu, D., Guanjun, B., and Qing-
hua, Y. (2015). Fruit harvesting continuum manipula-
tor inspired by elephant trunk. International Journal
Constant Curvature Kinematic Model Analysis and Experimental Validation for Tendon Driven Continuum Manipulators
217