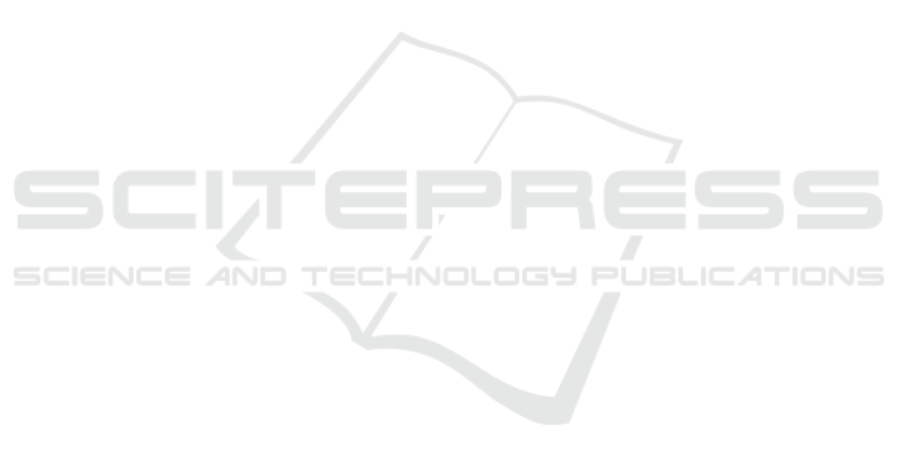
In recent years, many research institutes have conducted temperature sensor dynamic calibration
research. Because dynamic calibration of temperature sensor also relate to the environment in which
they are used, so it makes certain differences in dynamic calibration of temperature sensor in many
research institutes.
2. Research actuality of dynamic calibration of sensor
2.1. Domestic and foreign research situation
The research of dynamic character of sensor is always an active subject in academic field. In recent
ten years, the research has changed from applying to military field to civil fields and it has made that
more and more people begin to conduct research about dynamic character of sensor.
It has been a long time to conduct the research about temperature sensor dynamic calibration
overseas and involved in broader areas. Many countries such as America, Russia, Germany and India
have already achieved high level, but they don’t share their achievements. In recent ten years many
domestic institutes and universities have made deep research about the dynamic calibration of sensor
and obtain satisfied results.
2.2. Concept of dynamic calibration
When the temperature of gas stream changes, such as rise or depress abruptly, we call it dynamic
temperature. When the temperature sensor measures dynamic temperature, it can’t reflect the changes
of the temperature of gas stream rapidly because of its certain mass and heat inertia.
The dynamic response characteristic of temperature sensor means the relation of the temperature of
sensor itself and increment of temperature being measured. We usually express them with differential
equation or transfer function. As the temperature being measured changes in different forms such as
step signal, impulse, or sine wave, the response to sensitive element of temperature sensor can reflect
the dynamic characteristic of the sensor. So we often describe the dynamic characteristic of sensor
with its response to step temperature and define two parameters, thermal response time and time
constant, to reflect the dynamic characteristic. The quality of dynamic characteristic directly reflects
the tracking ability of sensor on temperature changing over time.
Dynamic calibration of temperature sensor is a process of record and calculation. First the sensor’s
response to step signal under certain conditions is measured, and then, the thermal response time or
time constant will be calculated through the tracking record in the response process. Calibration
process mainly include generation of stable calibration conditions (stable velocity field and
temperature field), making the temperature sensor accept the temperature step signal stimulation,
collection of being calibrated sensor’s response to step signal by testing system, calculating the
thermal response time or time constant. The two parameters not only relate to structure, material,
using conditions of the sensor, but also relate to flow stream being tested and calibration conditions.
2.3. Content of dynamic calibration
Dynamic calibration of sensor mainly include two factors.
2.3.1. Dynamic demarcate. Because sensor is widely used in automatic inspect of produce process,
new type of sensors are continuously manufactured. In order to know the dynamic characteristic of
sensor accurately, we need to conduct the dynamic demarcate.
2.3.2. Dynamic proofread. After a long-term use there will be some problems in the sensor or home-
made sensor such as time float, temperature float, or some parameters changed. All these phenomena
can result in sensitivity or zero position changed obviously. So it must be dynamic proofreaded for
sensor [2].
IWMCE 2018 - International Workshop on Materials, Chemistry and Engineering
6