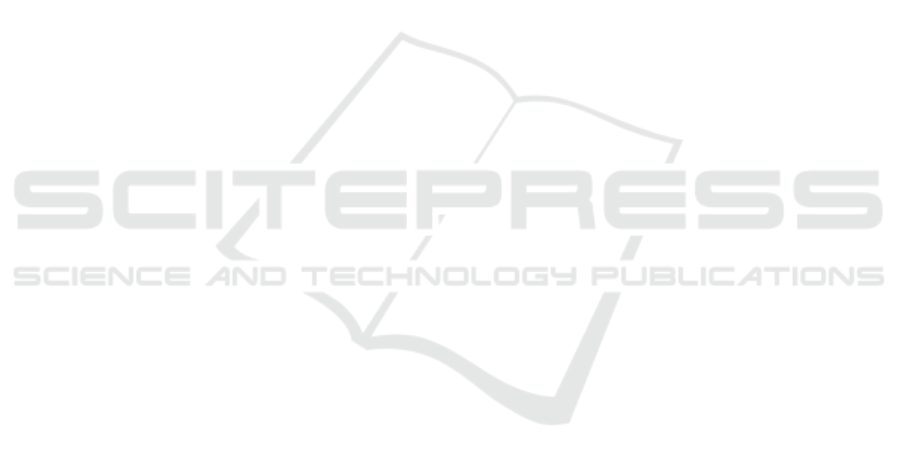
Dynamic Simulation and Test Analysis of Space Truss
Structure
H T Luo
1
, P Wang
2
, N Chen
2, *
, S P Chen
2
, W Wang
2
, T K Wu
3
and H N Wang
2
1
Shenyang Institute of Automation Chinese Academy of Sciences, Liaoning,
Shenyang 110016
2
Northeastern University, Shenyang 110019, P.R. China
3
Shenyang Ligong University, Shenyang 110159, P.R.China
Corresponding author and e-mail: N Chen, chenning2017@126.com
Abstract. Aerospace products are subjected to vibration environment during launching
process. The dynamic characteristics of aerospace products play a decisive role in
environmental adaptability of products. This paper describes the design of a space truss
structure and the load, in order to get the dynamic characteristics, finite element modal
analysis and modal test is done on the structural model, through correlation analysis to
determine the degree of conformity of the finite element model with the experimental model,
the truss structure and load finite element modal and experimental modal similarity degree is
higher, the finite element the model is acceptable; The dynamic simulation of the structure is
carried out by the qualified finite element model, and the dynamic simulation results are
verified by the vibration test; The method for obtaining the dynamic characteristics of
aerospace products and the way of dynamic simulation for launching process is of great
reference value for the design of aerospace products.
1. Introduction
As the spacecraft moves towards a larger, more complicated direction. The space truss [1] is widely
used because of its easy disassembly, good technology and light quality, and it can be adjusted
according to specific needs. It is also an important part of the international space station. The
application of space truss in space was first launched on August 20 and September 5, 1977 by
Voyager 2 and 1 [2].
The random vibration is mainly caused by the exhaust noise of the engine during takeoff, the
aerodynamic noise of the transonic flight section and the pressure pulsation in the engine combustion
chamber. The low-frequency sinusoidal vibration [3]
is primarily a free oscillation of the low order
mode of the elastomers caused by pogo vibration and engine start, ignition quenching and the stage
separation; the turbulence caused by the shock wave of the wind and transonic flight segments, and
the low-order longitudinal oscillation caused by incomplete combustion of the engine.
This kind of low frequency vibration environment
[4-5] can make the space truss structure
damaged, loose connections, structural deformation, the phenomenon of performance degradation,
and the vibration can reduce photoelectric instrument accuracy, mechanical fatigue, circuit
instantaneous short circuit, open circuit, even function failure
[6].
56
Luo, H., Wang, P., Chen, N., Chen, S., Wang, W., Wu, T. and Wang, H.
Dynamic Simulation and Test Analysis of Space Truss Structure.
In Proceedings of the International Workshop on Materials, Chemistry and Engineering (IWMCE 2018), pages 56-63
ISBN: 978-989-758-346-9
Copyright © 2018 by SCITEPRESS – Science and Technology Publications, Lda. All rights reserved