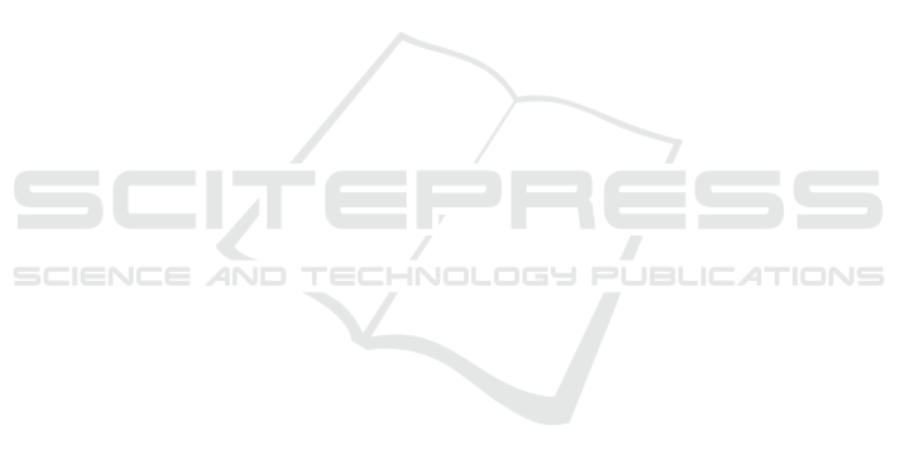
Thermo-Fluid-Solid Coupling Analysis in the Steam
Generator of a High Temperature Gas Cooled Reactor
W Afsar
*
, J Cai and S S Cui
School of Nuclear Science and Engineering, North China Electric Power University,
Beinong Road, Huilongguan, Changping District, Beijing, China, 102206
Corresponding author and e-mail: W Afsar, wajahatafsar98@yahoo.com
Abstract. This paper is about the high temperature gas cooled reactor (HTGR-10) of China
which is an experimental reactor. The thermo-flu id-solid coupling analysis for the steam
generator of HTGR is performed in wh ich the steam generator is modelled and then tested for
some boundary conditions. The analysis is of key impo rtance as Steam generator is very
crucial component of a power plant system that ensures the safety and efficiency of a plant.
To predict the thermal distribution in the tubes of a steam generator the coupled heat transfer
between the primary and secondary sides must be considered. ANSYS Fluent is used for
analysis that employs finite element method to achieve the task. The temperature distribution
within the steam generator is analysed. The resulting temperature profile, pressure profile and
the velocity profile for the coolant and feedwater is determined. In static structural analysis
equivalent stress, equivalent elastic strain and the total deformat ion produced in the tube
under such conditions is calculated. We see that the temperature of feedwater increases
continuously as it moves upward in the tube while the coolant (He gas) temperature decreases
as it goes down through the shell. The pressure of a coolant decreases as it flows downwards
in the shell and consequently its velocity increases in the said direction. The velocity of a
feedwater increases gradually as it rises up in the tube due to gradual decrease in its pressure.
The equivalent stress, equivalent elastic strain and the total deformation produced in a tube
are highly dependent on system temperature, tube material and the geometric configuration of
tube.
1. Introduction
High temperature gas-cooled reactors can serve as possible energy generation source as well as the
process heat source at different temperatures. Due to simultaneous production of electricity with the
recovery and utilization of heat the plant can acts as a combined heat and power plant. Some of the
unique features of this type of plant include its inherent safety, passive heat removal system for
residual heat, graphite reactor core, free from corrosion problems, eliminates risk of fuel coolant
interaction due to coated fuel particles, non-radioactive coolant, higher conversion efficiency and a
lower power density [1, 2].
No doubt while talking about nuclear reactors one of the most important concern that quickly
comes in mind is the safety of a plant as there have been some of the serious accidents in the past
history that have left very tragic after-effects. However, HTGR is considered as an excellent
236
Afsar, W., Cai, J. and Cui, S.
Thermo-Fluid-Solid Coupling Analysis in the Steam Generator of a High Temperature Gas Cooled Reactor.
In Proceedings of the International Workshop on Materials, Chemistry and Engineering (IWMCE 2018), pages 236-242
ISBN: 978-989-758-346-9
Copyright © 2018 by SCITEPRESS – Science and Technology Publications, Lda. All rights reserved