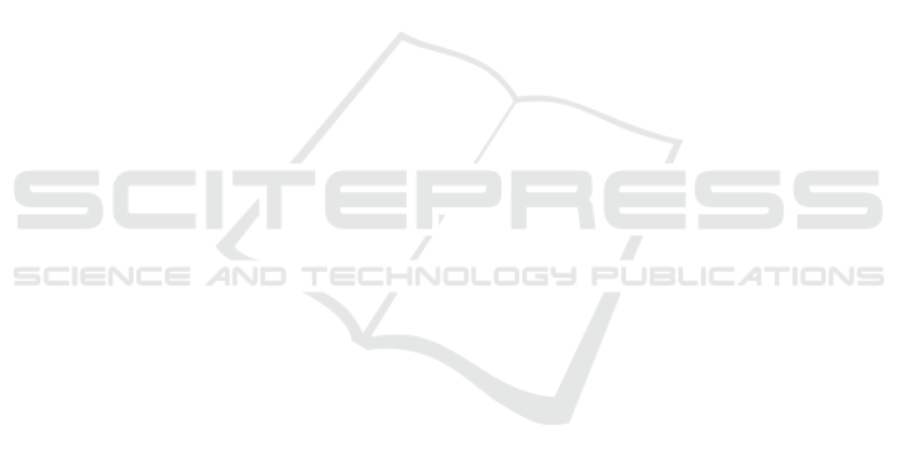
Preparation of Flexible Epoxy Resin Containing
Polyurethane Segments
C Z Liu
1,2
, M M Sun
1,2
, J X Jia
3
, G Xue
1
, C Y Song
1,2
, J H Li
1
, X G Zhang
1,2
, L
Wang
1
, M Zhao
1
and B Zhang
1,2,*
1
Institute of Petrochemistry, Heilongjiang Academy of Sciences, Harbin,
Heilongjiang 150040, P. R. China.
2
Institute of Advanced Technology, Heilongjiang Academy of Sciences, Harbin,
Heilongjiang 150020, P. R. China.
3
AVIC huiyang aviation propeller co., Ltd, Baoding, Hebei 071000, P. R. China.
Corresponding author and e-mail: B Zhang, zhangbin_hipc@126.com
Abstract. Epoxy resin is applicable for adhesives, coatings, electronic packaging, composite
materials and other fields. In this paper, an original flexible epoxy resin (FEP) was
synthesized by introducing polyurethane segments into the main chain. The formation of FEP
was characterized using FTIR and
1
H MNR methods. Subsequently, the bonding properties of
the FEP/bisphenol A diglycidyl ether (DGEBA) blends were studied, and 4,4’-
diaminodiphenylmethane (DDM) was used as a curing agent. The results showed that the
introduction of FEP made a great improvement for T-peel strength, while the lap shear
strength at different temperature increased firstly and then decreased with the increasing of
FEP content.
1. Introduction
Epoxy resin has been widely used in many industrial applications, such as adhesives, coatings and
composite materials for many years [1-2]. Similar to other thermosetting resins, the cured epoxy resin
shows a brittle behavior due to high crosslink density. The commonly approach used to improve the
toughness of epoxy resins is the incorporation of second phase particles, such as rubber elastomer,
thermoplastic polymer, inorganic nanoparticle, liquid crystalline polymer, and hyperbranched resin
reported in many papers [2-5].
In recent years, polyurethane (PU) has attracted much research attention due to its versatile
applications. Generally, PU was composed of polyether or polyester “soft” segments and a varieties
of isocyanate (-NCO)-based “hard” segments [6]. It was found that the modified epoxy resin with PU
elastomer showed a good toughness and low temperature performance because of the formation of an
interpenetrating network structure. The urethane groups (-NHCOO-) in the PU molecular chain also
play a positive impact on mechanical strength, impact resistance and bonding strength of epoxy resin.
However, the traditional PU is sensitive to moisture for the existence of free -NCO groups, and the
corresponding modified epoxy adhesive exhibits a poor storage stability [7]. Therefore, in this work,
Liu, C., Sun, M., Jia, J., Xue, G., Song, C., Li, J., Zhang, X., Wang, L., Zhao, M. and Zhang, B.
Preparation of Flexible Epoxy Resin Containing Polyurethane Segments.
In Proceedings of the International Workshop on Materials, Chemistry and Engineering (IWMCE 2018), pages 565-570
ISBN: 978-989-758-346-9
Copyright © 2018 by SCITEPRESS – Science and Technology Publications, Lda. All rights reserved
565