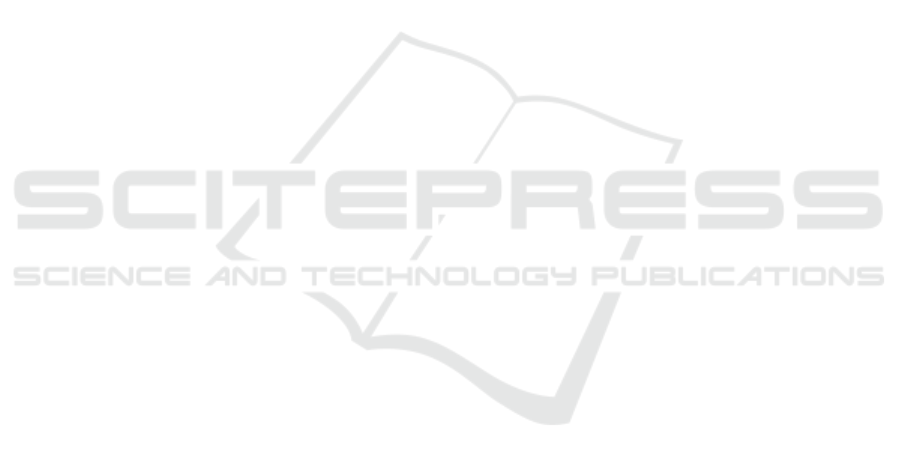
Three Dimensional Numerical Simulation of Oil Containment
Process by Flexible Oil Booms in Inland Waters
X Feng
*
, Y Y Zhang and Z W Wu
Marine Eng. College, Dalian Maritime Univ. Dalian 116026, China
Corresponding author and e-mail: X Feng, 530546168@163.com
Abstract. The deformation of oil containment boom in inland waters and the hydrodynamic
process are investigated based on multiphase CFD (Computational Fluid Mechanics) model
and the structure analysis model by system coupling. The velocity field near the flexible
boom under water current is compared with those behind the rigid boom. The process of
spilled oil interception by oil boom is simulated through employing the VOF (volume of
fluids) method to tracing the oil-water two phase flows and the variation of oil slick shape is
investigated.
1. Introduction
Inland water oil spills which are not so large scale compared with marine oil spills can still cause
serious damage to natural resources and to those whose livelihoods depend on these resources. With
regard to the bio-environmental impact, inland water oil spills could directly slay the organism such
as animals, plants and even the smallest micro-organisms by the toxicological reaction and hypoxia
effect [1].On the other hand, spilled oil could experience series of physical and chemical changes,
such as spreading, drifting, evaporation, emulsification, dissolution, and participate in the biological
cycle through the food chain and eventually endanger the human society. Therefore, it is important to
improve techniques and equipment that facilitate spill clean-up for inland water oil spills [2].
Effective use of skimmers or in situ burning for an oil spill generally requires that the spill first be
contained using booms which are frequently used in inland water conditions due to the simple water
conditions compared to sea water conditions. However, the booms often fail to hold the oil even in
simple inland water situations due to hydrodynamic forces, which will significantly boost the clean-
up costs. Therefore a better understanding of the oil containment process by oil booms is required. As
is pointed out by FENG [3], there are mainly six failure mechanisms for the oil boom as shown in
Figure 1: entrainment failure, drainage failure, critical accumulation failure, splash-over, boom
submergence and boom planning. The last three failure modes are usually caused by the wind and
wave effects which commonly happened in sea conditions and not so frequently for inland water
conditions. So only the first three failure modes are talked about here. The entrainment failure as
described by Leibovich [4] and Milgram et al. [5] is caused by breaking of Kelvin-Helmholtz water-
oil interfacial waves at sufficiently large relative velocity. The drainage failure usually takes place
when the boom draft is insufficient to contain the oil slick and some oil goes underneath the boom as
shown in Cross and Hoult[6]. As shown in many experimental results [7-8], a third failure
Feng, X., Zhang, Y. and Wu, Z.
Three Dimensional Numerical Simulation of Oil Containment Process by Flexible Oil Booms in Inland Waters.
In Proceedings of the International Workshop on Environmental Management, Science and Engineering (IWEMSE 2018), pages 463-468
ISBN: 978-989-758-344-5
Copyright © 2018 by SCITEPRESS – Science and Technology Publications, Lda. All rights reserved
463