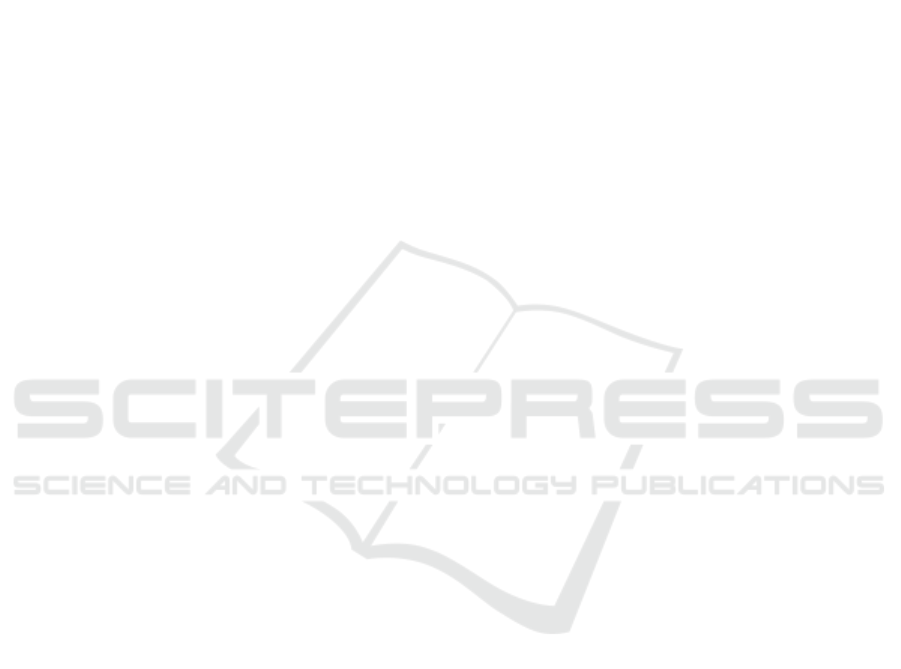
Dynamic Modeling and Simulation of a Slurry Mixing and Pumping
Process: An Industrial Case
Ridouane Oulhiq
1,2
, Khalid Benjelloun
1
, Maarouf Saad
3
, Yassine Kali
3
and Laurent Deshayes
2
1
AII Laboratory, Ecole Mohammadia d’Ing
´
enieurs, Mohammed V University, Rabat, Morocco
2
Innovation Lab for Operations, Mohammed VI Polytechnic University, Benguerir, Morocco
3
Electrical Engineering Department,
´
Ecole de Technologie Sup
´
erieure, Montreal, QC H3C 1K3, Canada
laurent.deshayes@um6p.ma
Keywords:
Mixing Tank, Centrifugal Pump, Slurry, Modeling, Simulation, Density Variation, Level Variation.
Abstract:
In this paper, a dynamic model of a slurry mixing and pumping process is proposed. The centrifugal pump
is modeled based on the hydraulic application, the hydraulic part and the induction motor models, taking into
account the pumped slurry density. This paper also proposes a new approach to estimate the parameters of the
pump’s hydraulic part model based on the pump characteristic curves. Additionally, a dynamic simulation of
the system is realized under MATLAB/Simulink environment and the variation effect of the process inputs on
the outputs is studied.
1 INTRODUCTION
In many process industries, the mixing and pumping
process is a decisive step. It is common to blend dif-
ferent products together to form a mixed slurry for
downstream processes. Eventually, the quality of the
final product will be derived by how good the mix
is and the precision of the inlet flows (Nienow et al.,
1997). Considering the widespread of such a pro-
cess, understanding its dynamics is of great impor-
tance. A steady state approach is often used to de-
scribe the system. However, a steady state process
requires constant properties. For slurry processes,
solids’ properties such as the granulometry change
as a function of time and place as does the solids’
density (Miedema, 1996). Since inlet density impacts
how easily the slurry is pumped (Blevins and Nixon,
2010), this change in density impacts the flow rate of
the slurry. Therefore, a dynamic model is needed, for
a better understanding, simulation and control of the
system.
A mathematical model, based on first order non-
linear differential equations, is used to describe the
mixing process (Deng, 2002). For the slurry pumping
process, the centrifugal pump is used. In (Kallesøe
et al., 2006), the dynamic model of the centrifugal
pump is divided into three sub parts: the pump mo-
tor, the hydraulic part and the hydraulic application.
The parameters of hydraulic part are calculated based
on the physical properties of the pump. The hydraulic
application is not detailed and the variation of flow is
not discussed. In (Valtr, 2017), the centrifugal pump
is modeled based on the hydraulic system without
considering the pump’s motor. In (Miedema, 1996) a
dynamic model for the system pump/pipeline is pro-
posed and simulated. However, the model assumes
that the pump drive behaves like a constant torque
system. Concerning the pump’s motor, the induction
motor is used. The model of the induction motor is
extensively described in literature. The most popular
representation is the so-called qd model based on a
series of mathematical transformations (Manekar and
Bodkhe, 2013). The idea of a revolving reference
frame, dq, is introduced to transform the ac compo-
nents of the vectors in the stator frame into dc sig-
nals in order to simplify calculations (Trzynadlowski,
2000).
In this work, a graphical method is used to es-
timate the pump’s hydraulic part, the head and the
load torque parameters. In literature, a numerical
method is used to calculate these parameters based on
the physical properties of the pump (Isermann, 2007;
Kallesøe et al., 2006), which is time consuming and
hard to apply in an industrial environment. For the
hydraulic application, it depends on the studied sys-
tem. A generalized method is presented in this work,
taking into account the friction factor variation along
with the slurry flow rate variation.
Oulhiq, R., Benjelloun, K., Saad, M., Kali, Y. and Deshayes, L.
Dynamic Modeling and Simulation of a Slurry Mixing and Pumping Process: An Industrial Case.
DOI: 10.5220/0007774000270035
In Proceedings of the 9th International Conference on Simulation and Modeling Methodologies, Technologies and Applications (SIMULTECH 2019), pages 27-35
ISBN: 978-989-758-381-0
Copyright
c
2019 by SCITEPRESS – Science and Technology Publications, Lda. All rights reserved
27