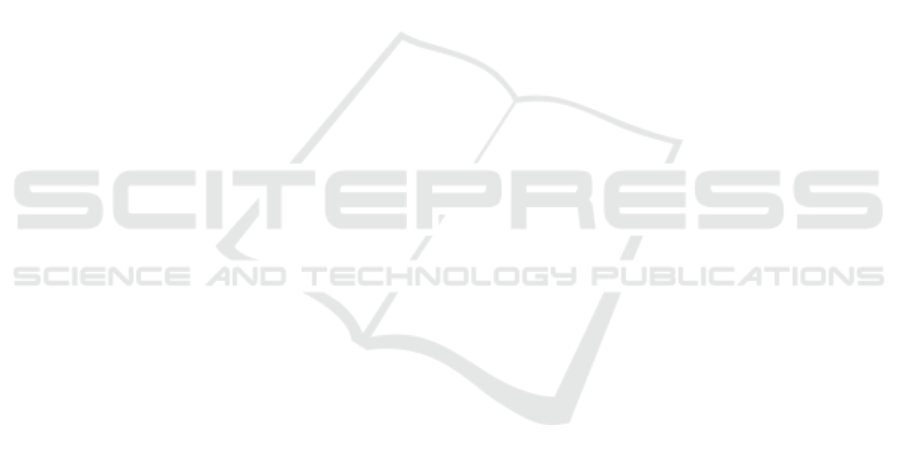
Ryu, K. H., Kim, G. and Han, J. S., 2001. AE-Automation
and Emerging Technologies: Development of a
Robotic Transplanter for Bedding Plants, J. Agric.
Eng. Res., vol. 78, no. 2, pp. 141-146.
Kang, D. H., Kim, D. E, Lee, G. I, Kim, Y. H., Lee, H. J.
and Min, Y. B, 2012. Development of a Vegetable
Transplanting Robot," J. of Biosystems Eng., vol. 37,
no. 3, pp. 201-208.
Tian, S., Lichun Qiu, L., Kondo, N., Yuan, T., 2010.
Development of automatic transplanter for plug
seedling," IFAC Proceedings Volumes, vol. 43, no. 26,
pp. 79-82.
Xin, J., Kaixuan, Z., Jiangtao, J., Hao, M., Jing, P., and
Zhaomei, Q., 2019. Design and experiment of
automatic transplanting device for potted tomato
seedlings, Proceedings of the Institution of
Mechanical Engineers, Part C: Journal of Mechanical
Mechanical Engineering Science, vol. 233, no. 3, pp.
1045–1054.
Jin, X., Li, M., Li, D., Ji, J., Pang, J., Wang, J. and Peng,
L., 2018. Development of automatic conveying system
for vegetable seedlings, EURASIP Journal on
Wireless, Communications and Networking, vol.
2018:178, pages 1-9.
Han, L., Mao, H., Hu, J. and Tian, K., 2015. Development
of a doorframe-typed swinging seedling pick-up
device for automatic field transplantation, Spanish
Journal of Agricultural Research, vol. 13, no. 2,
e0210, 14 pages.
Xin, J., Kaixuan,Z., Jiangtao, J., Xinwu, D., Hao, M., and
Zhaomei, Q, 2018. Design and implementation of
Intelligent transplanting system based on photoelectric
sensor and PLC, Future Generation Computer
Systems, vol. 88, pp. 127-139.
Tsuga, K., 2000. Development of fully automatic
vegetable transplanter. JARQ, Japan Agricultural
Research Quarterly, vol. 34, no. 1, pp. 21-28.
Kumar, G. V. P. and Raheman, H., 2011. Development of
a walk-behind type hand tractor powered vegetable
transplanter for paper pot seedlings, Biosyst. Eng., vol.
110, no. 2, pp. 189-197.
Dihingia, P. C. Kumar, G. V. P. , Sarma, P. K. and Neog,
P. 2018. Hand-Fed Vegetable Transplanter for Use
with a Walk-Behind-Type Hand Tractor, International
Journal of Vegetable Science, vol. 24, no. 3, pp. 254-
273.
Ndawula, I., Assal, S. F. M., 2018. Conceptual Design and
Kinematic Analysis of a Novel Open Field 3DOF
Multi Gripper Pot Seedlings Transplanting Robot, in
Proc. of the IEEE Int. Conf. on Mechatronics and
Automation (ICMA 2018), Changchun, China, August
5-8, pp.1458–1463.
Huang, T., Li , Z., Li, M., Chetwynd, D. G., Gosselin, C.
M., 2004. Conceptual design and dimensional
synthesis of a novel 2-dof translational parallel robot
for pick-and-place operations, ASME Journal of
Mechanical Design, vol. 126, pp. 449-455.
Kang, D. H., Kim, D. E., Lee, G. I., Kim, Y. H., Lee, H. J.
and Min, Y. B., 2012. Development of a vegetable
transplanting robot, J. of Biosystems Eng., vol. 37(3),
pp. 201–208.
Assal, S. F. M., 2017. A novel planar parallel manipulator
with high orientation capability for a hybrid machine
tool: kinematics, dimensional synthesis and
performance evaluation, Robotica, vol. 35, pp. 1031–
1053.
Laribi, M.A., Romdhane, L., Zeghloul, S., 2007. Analysis
and dimensional synthesis of the DELTA robot for a
prescribed workspace, Mechanism and Machine
Theory, vol. 42, pp. 859–870.
Optimum Design and FEA of a Hybrid Parallel-deployable Structure-based 3-DOF Multi-gripper Translational Robot for Field Pot
Seedlings Transplanting
77