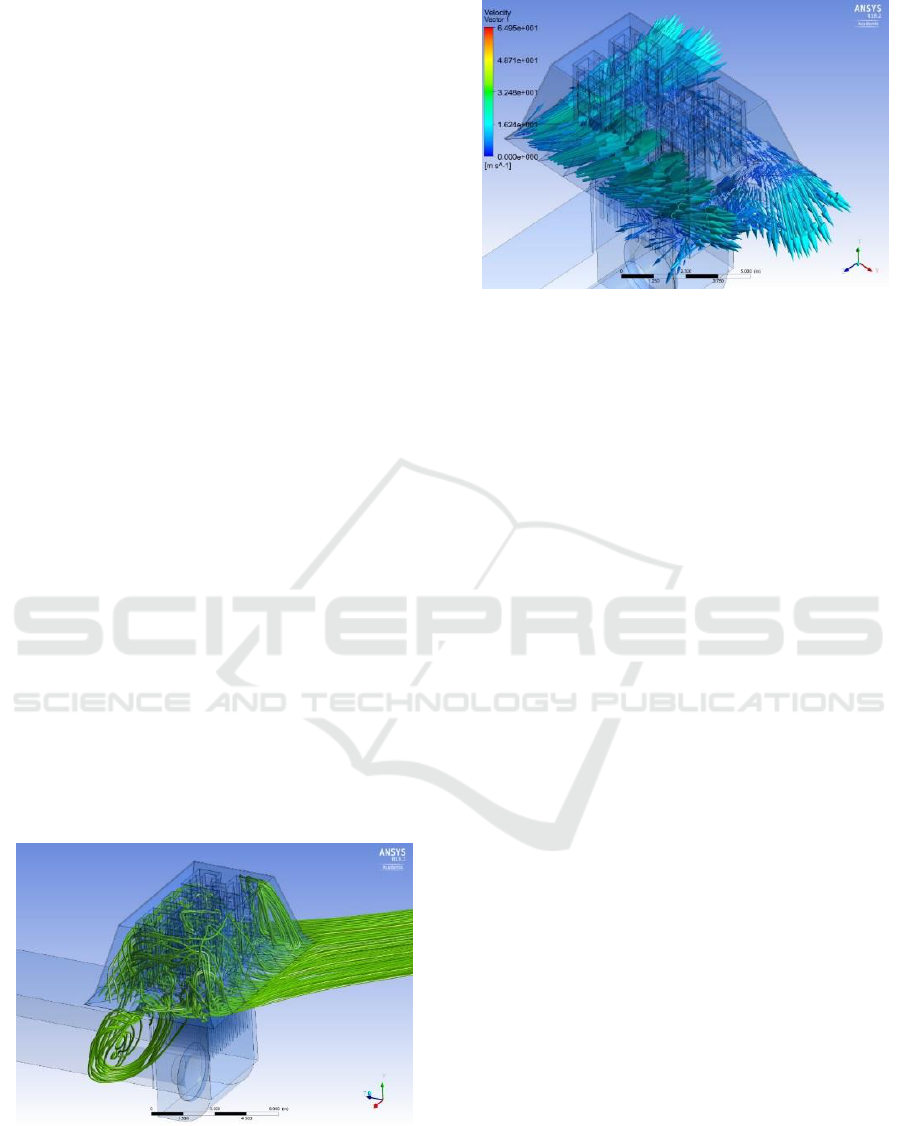
structure does not change in principle. It can be seen
that the working fluid is sucked into the shaft evenly
from all directions in windless weather, but in the
presence of wind the main part of the air enters from
the narrow sector on the windward side. At the same
time, when flowing the weather shield and shaft, a
vortex structure is formed on the leeward side (Figure
19, 20).
In calm weather, all the working fluid goes into
the filters after passing section 0 along the shortest
path. Overflow under the shield is minimal. In the
presence of wind, the working fluid immediately
enters the filters only on the windward side. At the
same time, the air flow velocity increases
substantially compared to calm conditions. The
amount of working fluid that passes under the shield
from the windward side is greater than the filters can
pass through on this side, and the working fluid
begins to flow to the leeward side. This overflow,
coupled with areas of reduced pressure on the leeward
side, caused by vortexes formation in the external
flowing past the shaft, leads to a complex unsteady
vortex structure between the inlet section and filter
box inlet on the leeward side. These circumstances
lead to the fact that the working fluid through the inlet
section under the weather shield (section 0) enters
unevenly, and there is a large number of backflows
(Figure 20), which increases the values of local
velocities there.
Another negative effect associated with such a
flow pattern under the shield is that the DIS tubes
installed in front of the filters is flowed not by air,
which goes in the direction of the filters, but by a
multidirectional and non-stationary flow. This will
blur the field of increased temperature created by
them and reduce the efficiency of the system.
Wind velocity - 20 m/s at an angle of 45
Figure 19: The trajectory of the particles of the working
fluid, before getting under the weather shield.
Wind velocity - 20 m/s at an angle of 135
Figure 20: Flow velocity vectors in the inlet section of the
shaft.
The described structure of the flow under the
shield in the presence of wind leads to the fact that the
distribution of flow rates between filter elements
changes. To confirm this, Figure 21 shows how the
mass flow rates of the working fluid change through
filter groups at a wind direction of 0° at a wind
velocity of 20 m/s. Distribution of mass flow rates for
other wind directions is not fundamentally different.
As can be seen, the presence of wind has a
significant impact on the distribution of mass flow
rates between the filter sections. As a rule, on the
windward side, the flow rate of working fluid through
the filters increases. There is an increase of flow rate
(at 20 m/s up to 3 times relative to windless weather)
at the angles (90...135° and 220...270°) relative to the
wind direction. In the presence of wind, the number
of filter elements (by 4 pcs.) from which the working
fluid is thrown back or the flow rate is significantly
less than the average value (they are mainly
concentrated in the “pockets” and on the leeward
side) on average is 12, which is 1.5 times greater than
in calm weather. The greatest number of filters that
do not work properly takes place with side winds
(45...135°).
The greatest pressure losses during the flowing
past the weather shield occur when the wind blows
into the corner (45° and 135°). This is because an
additional vortex is generated under the shield from
the inner side of the corner (Figure 22).
The presence of baffles streamlines the flow of the
working fluid under the shield. Without baffles, the
working fluid “hits” the lower row of filters, making
the mass flow rate distribution between the filters of
one vertical more uneven. On the windward sides, the
working fluid also moves with a significant horizontal
component, which adversely affects the operation of
the DIS. The variant with rounding the lower part of
SIMULTECH 2019 - 9th International Conference on Simulation and Modeling Methodologies, Technologies and Applications
96