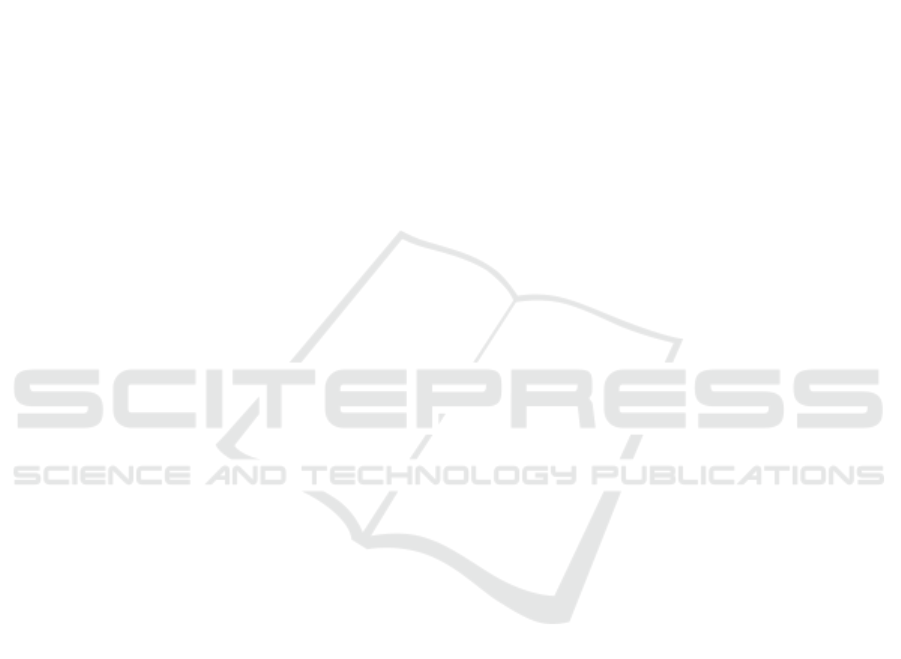
eliminate this drawback, 1/2D calculation models are
identified by the results of 3D calculations. The latter
have minimal assumptions and show the best
accuracy among the calculation methods known
today. Based on the comparison, corrective
corrections are found for the 1/2D model. 3D models
in turn are identified by the test results. When creating
identification blocks, “learning” algorithms for 1/2D
and 3D models are proposed.
An algorithm for identifying simplified models
using high-level models is developed and
successfully tested.
The developed algorithms and pilot samples of the
virtual compressor test bench are the first steps of a
fully-featured “bench”, which will be able to replace
most of the field tests. The virtual bench will allow to
model a larger range of impacts on the object under
study, including those that cannot be reproduced on
existing benches or require huge material and energy
costs. Modern development of automated tools and
tools for the design of gas turbine engines,
processing, management and accumulation of
information allows us to believe in the successful
solution of this problem and the achievement of a
qualitative leap forward in the characteristics and
capabilities of virtual test benches.
ACKNOWLEDGEMENTS
This work was supported by the Russian Federation
President's grant (project code МК-3168.2019.8).
REFERENCES
Boyce, M., 2012. Gas Turbine Engineering Handbook, Gas
Turbine Engineering Handbook, Butterworth-
Heinemann, Elsevier, MA. 4th ed.
Casey, M. and Robinson, C. 2013. A Method to Estimate
the Performance Map of a Centrifugal Compressor
Stage. Journal of Turbomachinery, 135 (2): 021034
Dubitsky, O., 2017. Optimization of Cycle Parameters, Fuel
Consumption, and Weight of a Turboshaft Engine
Using 1D Design Tools. Concepts NREC SpinOffs |
Turbomachinery Blog.
Erdmenger, R.R. and Michelassi, V. 2014. Impact of Main
and Splitter Blade Leading Edge Contour on the
Performance of High Pressure Ratio Centrifugal
Compressors. Proceedings of the ASME Turbo Expo,
GT2014-27062
Fadilah, P.A. and Erawan, D.F. 2018. Small centrifugal
compressor performance trend prediction based on
computational fluid dynamic. Paper presented at
the Journal of Physics: Conference Series, 1130(1)
Geller, M., Schemmann, C. and Kluck, N., 2017.
"Optimization of the Operation Characteristic of a
Highly Stressed Centrifugal Compressor Impeller
Using Automated Optimization and Meta-Modelling
Methods. Proceedings of the ASME Turbo Expo,
GT2017-63262
Guo, Z., Song, L., Zhou, Z., Li, J. fnd Feng, Z. 2015. Multi-
Objective Aerodynamic Optimization Design and Data
Mining of a High Pressure Ratio Centrifugal Impeller.
Journal of Engineering for Gas Turbines and Power,
137 (9), № 092602
Hehn, A., Mosdzien, M., Grates, D. and Jeschke, P. 2018.
Aerodynamic optimization of a transonic centrifugal
compressor by using arbitrary blade surfaces. Journal
of Turbomachinery, 140 (5): 051011
Hunziker, R., Dickmann, H.-P. and Emmrich, R. 2001.
Numerical and experimental investigation of a
centrifugal compressor with an inducer casing bleed
system. Journal of Power and Energy, 215 (6): 783-791
Komarov, O.V., Sedunin, V.A., Blinov, V.L., Serkov, S.A.
and Brodov, Yu.M., 2015. The effect of optimization
problem definition in 2D compressor airfoil.
Proceedings of the ASME Turbo Expo, GT2015-44043.
Kulagin, V.V., 2002. Teoria, raschet i proektirovanie
aviacionnyh dvigateley i energeticheskih ustanovok.
Uchebnik. Osnovy teorii GTD. Rabochiy process i
termodinamicheskiy analiz (The theory, calculation
and design of aircraft engines and power plants: a
Textbook. Fundamentals of the theory of the CCD.
Workflow and thermodynamic analysis),
Mashinostroenie, Moskow.
Li, X., Zhao, Y., Liu, Z. and Chen, H. 2016. The
Optimization of a Centrifugal Impeller Based on a New
Multi-Objective Evolutionary Strategy. Proceedings of
the ASME Turbo Expo, GT2016-56592
Liu, X.M. and Zhang, W.B. 2010. Two Schemes of Multi-
Objective Aerodynamic Optimization for Centrifugal
Impeller Using Response Surface Model and Genetic
Algorithm. Proceedings of the ASME Turbo Expo,
GT2010-23775
Medic,G., Sharma, O.P., Jongwook, L., Hardin, L.W.,
McCormick, D.C., Cousins, W.T., Lurie, E.A., Shabbir,
A., Holley, B.M. and Van Slooten P.R., 2014. High
Efficiency Centrifugal Compressor for Rotorcraft
Applications. NASA/CR-2014-218114.
NUMECA, 2008. User Manual AutoGrid5 Release 8.4,
NUMECA.inc., Belgium.
Popov, G., Goriachkin, E., Kolmakova, D. and Novikova,
Y. "Multicriteria optimization of axial low pressure
compressor of gas turbine power plant", Proceedings of
the ASME Turbo Expo, 2016, GT2016-57856.
Rusch, D. and Casey, M. 2013. The design space
boundaries for high flow capacity centrifugal
compressors. Journal of Turbomachinery, 135 (3):
031035
Siller, U., Kröger, G., Moser, T. and Hediger, S., 2014.
Towards a highly efficient small scale turboshaft
engine. Part II: Aero-mechanical turbine design and
optimization. Proceedings of the ASME Turbo Expo,
GT2014-26320.
Multi-level "Learnable" Model of the Workflow in the Centrifugal Compressor Stage
109