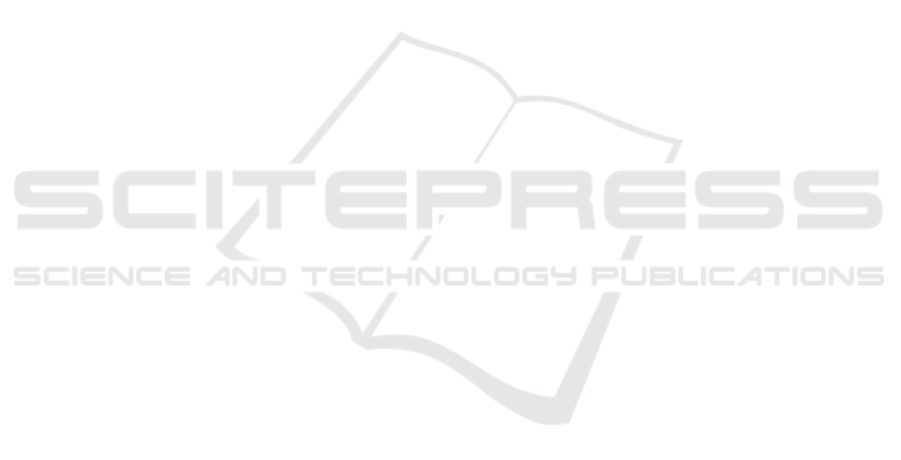
drill carried out at the factory which does not reflect
the true evacuation process. In the drill, fire and
smoke are not created and most importantly, exits are
not blocked during the fire drill at the factory. But
exits near the fire will be blocked and halt the
occupants from safe egress. In Pathfinder simulation,
in case of fire in warehouse, exits were blocked near
fire location and occupants were assigned to use
specific exit route through waypoint to safe exit.
Pathfinder provides some extent of behavior based on
parametric input from the data from survey. The
simulation gives the Required Safe Egress Time and
identifies hazardous area in terms of congestion in
exits of the floors due to high density which helps
assessing the risk. One important drawback is that,
Pathfinder cannot predict the real behavior of
occupants in case of emergency. Behavior of
occupants varies largely based on the experience,
training, safety culture etc. However, the Pathfinder
simulation largely opens the scope of optimizing the
current emergency management approach in terms of
adopting different strategy in emergency
preparedness, response, mitigation and recovery. To
optimize the emergency strategy, following measures
can be taken:
Relocating the warehouse to some other places
would be the optimal choice for the management of
the factory to avoid huge economic loss and loss of
lives.
The findings from simulation like clogging,
behavior etc. should be taken into consideration
during fire drill in mitigation and prevention phase of
emergency management.
Quantitative risk analysis tools may be used to
assess the fire risks.
The number of occupants in 2nd and 3rd floor
should be reduced.
Authority should engage the local people,
hospitals and law enforcement agencies in the
response and recovery stage.
There should be an incident command system at
the factory for handling any emergency at any time
(day or night).
This research using risk analysis tools and
Pathfinder simulation software can help the entire
Readymade garment industries along with other
industries and any building structures to assess the
risk and to optimize the emergency management in
case of fire evacuation.
ACKNOWLEDGEMENTS
The authors would like to express their gratitude to
Ms Annette Kaalund-Jørgensen, Capacity
Development Advisor, Danida Fellowship Centre for
her kind support.
REFERENCES
Ahmed, S., Mehmood, S. and Kristensen, A.S., 2019.
Critical Analysis of Computer-based Evacuation
Simulation of an Educational Institution. s.l., in
Proceedings of the 11th International Conference On
Computer Modeling and Simulation (pp. 26-30). ACM.
Aven, T., 2008. Risk analysis: Assessing uncertainties
beyond expected values and probabilities. Chichester,
UKT: Wiley.
Barua, U. and Ansary, M.A., 2017. Workplace safety in
Bangladesh ready-made garment sector: 3 years after
the Rana Plaza collapse. International Journal of
Occupational Safety and Ergonomics, 23(4), pp. 578-
583.
FSCD, 2019. Accident, Rescue and Yearly Statistics.
[Online] Available at: http://www.fireservice.gov.bd/
site/files/e4d115ed-d51b-4bfc-b941-2092c1a5c916/
Accident,-Rescue-&-yearly-Statistic [Accessed 12 My
2019].
Galea, E., 2003. SFPE Engineering Guide to Human
Behavior in Fire. s.l.:s.n.
George D. Haddow; Jane A. Bullock; Damon P. Coppola,
2006. Introduction to Emergency Management. 5th ed.
225 Wyman Street, Waltham, MA 02451, USA:
Elsevier.
Hasan, M. and Mahmud, A., 2017. Risks Management of
Ready-Made Garments Industry in Bangladesh.
International Research Journal of Business Studies,
10(1), pp. 1-13.
ISO, 2015. Fire safety engineering -- Selection of design
fire scenarios and design fires -- Part 1: Selection of
design fire scenarios. [Online] Available at:
https://www.iso.org/standard/63140.html [Accessed 12
May 2019].
Khandoker, M.A.R., Mou, R.J., Muntaha, M.A. and
Rahman, M.A., 2018. Numerical simulation of fire in a
multistoried ready-made garments factory using
PyroSim. s.l., In AIP Conference Proceedings (Vol.
1980, No. 1, p. 050026). AIP Publishing..
Solidarity Centre, 2018. Bangladesh Safety Incident Chart.
[Online] Available at: https://
www.solidaritycenter.org/wp-content/uploads/2018/
04/Bangladesh-Safety-Incident-Chart.4.9.18.pdf
[Accessed 12 May 2019].
Thunderhead engineering, 2018. Pathfinder user manual.
s.l.:403 Poyntz Avenue, Suite B, Manhatten, KS 66502
USA.
Optimization of Egress Controls of Fire Emergency Management Plans using Agent based Simulation: A Case Study of Ready-made
Garment Industry
391