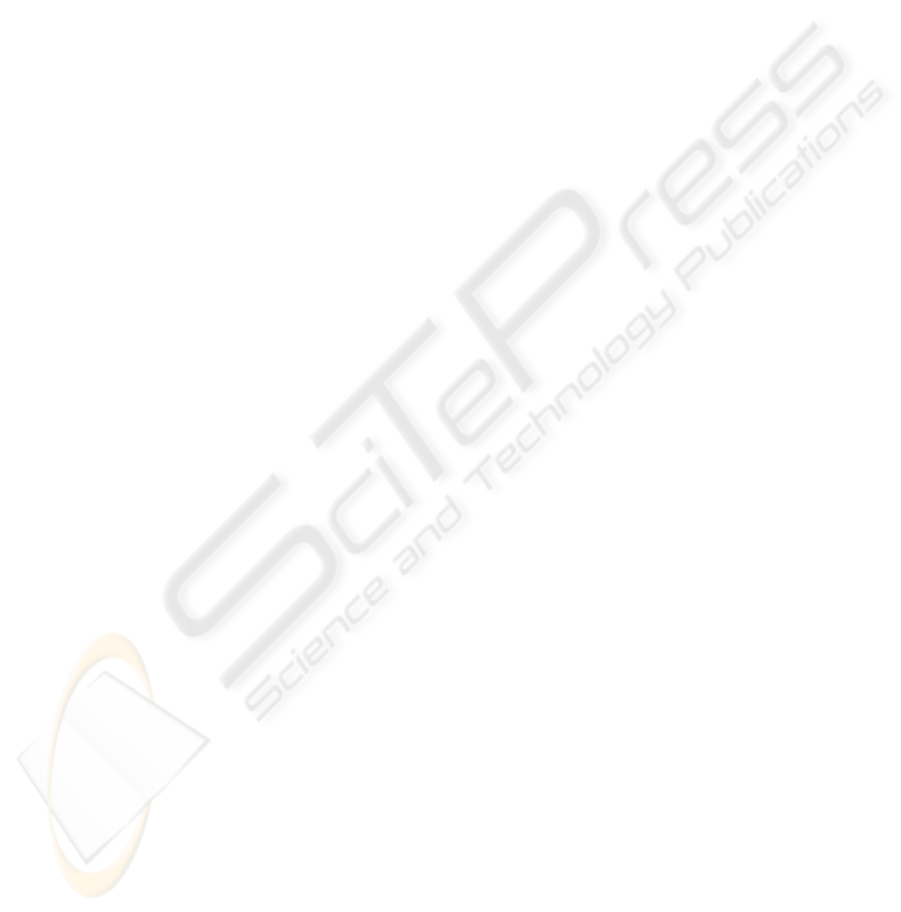
2 THE TARGET PROBLEM
The target problem addressed by the constraint
logic-based approach is scheduling an efficient
operations sequence in the dye house of a socks
manufacturing company. On the whole, the
production process of socks making is divided into
five divisions. The first process in sock
manufacturing is knitting using machines to turn raw
materials (called yarn), such as wool, nylon and
cotton, into semi-finished goods. The types of socks
produced range from fine gauge business socks,
right down to heavy cushion foot sports socks. The
next phase is seaming, or toe closing. Jobs are
required to go through three separate operations in
this area. They are: (i) turning the socks inside out
for sewing, (ii) sewing of the toe line, and (iii)
turning back to the right side and expanding the toe
line - to avoid having a large chunky over-locking
line at the toe of the sock. After the toe closing
operation socks are sent to the dye house for
colouring or finishing. The socks are dyed in
machines most suited to the fibre type. Wool takes
about 4 hours to dye, while cotton can take up to 8
hours. There are 4 different dyeing machine groups
in a dye house. The next process area is pressing.
This operation provides a permanent setting of the
fibre and a clean, smooth texture for final
presentation for sale. After pressing, socks are
examined and packed.
In this paper, the focus is on the use of constraint
logic programming in the dye house scheduling of a
socks manufacturing factory. The significance of
scheduling in the dyeing division is grounded on the
fact that it determines the quality of final products
for the reason of dependencies among the sequence
of colours, fibre types, and dyeing capabilities of
machines. It also affects the productivity of the
whole manufacturing process due to a limited
number of facilities equipped being in operation. At
present, the production scheduling in each division
is handled manually. However, the shop floor is a
very dynamic environment and the scope and the
pertinent variables in scheduling far exceed any
human scheduler's capabilities. As for dye house
scheduling, the types of job schedules to be
produced range from a three-day scheduling to daily
scheduling, in alignment with the aspect of shop
floor such as a set of job orders released from the
previous stages, jobs to be delivered to the next
process within the deadline requested, urgent orders
to be scheduled for a short period of time and the
capacity (load limits) of dye house resources. The
human scheduler is only able to produce a rough
schedule; the actual shop floor operation still
depends on constant monitoring by the human
scheduler.
2.1 The Test Domain
The scheduling domain is derived from actual
manufacturing data. It is based on a general
operations scheduling but remains grounded in a
real-world application. The scheduling data used is
provided by the factory. The test domain is based on
a dye house covering the operations associated with
the colouring of four types of fibres. The key
characteristics of the problem are as follows:
▪ An order may consist of a set of sequenced
operations to be dyed on the specified machine.
▪ The dye house consists of four major dyeing
machine groups, defined in terms of their
processing capabilities.
▪ The socks are dyed in dye machines most suited
to the fibre type.
▪ The operation duration (processing times) ranges
from 4 hours to 8 hours.
▪ In view of its previous process, each job operation
has a requested start time to perform the operation.
▪ The number of colours at a dye house can be
broadly divided into nine major groupings.
▪ The job sequence within specific machines for
dyeing is constrained by the colour of the dyes
which are ordered from light to dark colours.
▪ Each job operation has a requested deadline to
meet the delivery of job order.
The descriptions of job operations at a typical
dye house are given in Table 1. A job is identified
by a unique job order (style) number, which is
recorded in the job order column. However on the
shop floor, a job is often identified by its operation
formula which is combined by its fibre and colour
used. Each job is assigned a requested start time and
due time. The remaining column shows a description
of the operation to be dyed (e.g., blue 69 etc.
represents fabric dyeing of different colours). The
predominant fibres to be dyed are 100% wool (WL)
and wool-blends (WB), and 100% cotton (CT) and
cotton-blends (CB).
AN EFFECTIVE APPROACH FOR REAL-WORLD PRODUCTION PLANNING
115