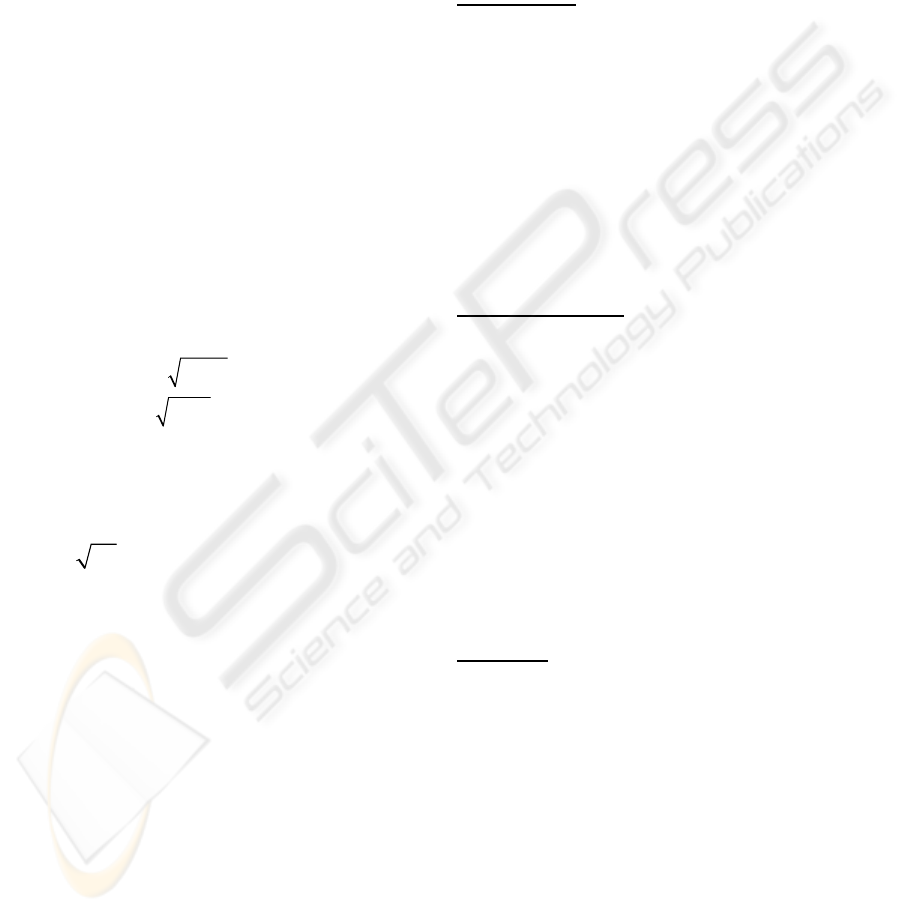
respectively. As is normally the case in such studies,
all states are assumed to be available thus making
the system observable. By introducing state
feedback, the control input u
L
can be written as
L
=−uKx
. (2)
Thus one obtains a closed loop system
(- )
L
=xABKx
&
. (3)
In Equation (3), matrix
-
BK decides the
modal parameters of the closed loop system, such as
the modal frequencies, damping ratios and mode
shapes. A relation exists, between the modal
parameters of the system and the eigen-parameters
of matrix
A-BK, as eigen-parameters decide the
controlled behavior of the closed loop system
(Nishitani,1998), Equation (3). To obtain the relation
explicitly, it is useful to define some notations.
Assuming
A-BK to be a matrix of real-numbers, the
eigenvalues and eigenvectors of
A-BK appear as
conjugate pairs. Let
21i
−
and
2i
be the ith pair of
eigenvalues, and
21i−
and
2i
be the corresponding
ith pair of eigenvectors. Also let
,
ii
and n
i
denote, respectively, the modal frequency, damping
ratio and mode shape of the
ith mode. Then we have:
2
21
2
2
j1
j1- ;
iiiii
iiiii
λζωωζ
λζωωζ
−
=− + −
=− −
;
⎫
⎬
⎭
and
21 2
21 2
;
ii ii
ii
ii
λλ
−
−
⎧⎫ ⎧
==
⎨⎬ ⎨
⎩⎭ ⎩
nn
zz
nn
;
for
i = 1 to n , (4)
where j =
1−
, and n is the number of degrees of
freedom of the system.
Equation (4) gives a one-to-one mapping
between the system modal parameters and the eigen-
parameters of matrix A
-BK. Therefore, if the modal
parameters
,i
and
ii
n
are specified in the
domain, one can calculate the corresponding
eigenvalues and eigenvectors for the closed loop
system using Equation (4). Moreover, according to
Equation (3), if one can modify and assign the
eigenstructure at desired values by selecting proper
feedback matrix K, the modal property of the system
can be modified accordingly. This is the essence of
the modal control procedure. It is also the reason
why modal control is also called eigenvalue
assignment control.
2.2 Hierarchical Structure
The control system developed for the deployable
manipulator system has a three-level structure. This
hierarchical form combines the advantages of a crisp
controller, i.e. a modal controller, with those of a
soft, knowledge-based, supervisory controller. The
overall structure can be developed into three main
layers (de Silva, 1995).
Bottom Layer
The bottom layer deals with information coming
from sensors attached to the system. This type of
information is characterized by a large amount of
high resolution data points produced and collected at
high frequency. The crisp controller used is a state
feedback regulator with feedback gain matrix
determined using the eigenstructure assignment
approach. The control algorithm can be described as:
;
- ;
+
=
xAxBu
uKx
&
(5)
where u is the control action and K the feedback
matrix.
Intermediate Layer
The data processing for monitoring and
evaluation of the system performance occurs in the
intermediate layer. Here high-resolution, crisp data
from sensors are filtered to allow representation of
the current state of the manipulator. This servo-
expert layer acts as an interface between the crisp
controller, which regulates the servomotors at the
bottom layer, and the knowledge-based controller at
the top layer. The intermediate layer handles such
tasks as performance specification, response
processing, and computation of performance indices.
This stage involves, for example, averaging or
filtering of the data points, and computation of the
rise time, overshoot, and steady state offset.
Top Layer
The knowledge base and the inference engine in
the uppermost layer are used to make decisions that
achieve the overall control objective, particularly by
improving the performance of low-level direct
control. This layer can serve such functions as
monitoring the performance of the overall system,
assessment of the quality of operation, tuning of the
low-level controllers, and general supervisory
control. In this layer, there is a high degree of
information fuzziness and a relatively low control
bandwidth. Figure 1 presents the hierarchical
structure of the three-level control system.
HIERARCHICAL MODAL CONTROL OF A NOVEL MANIPULATOR
207