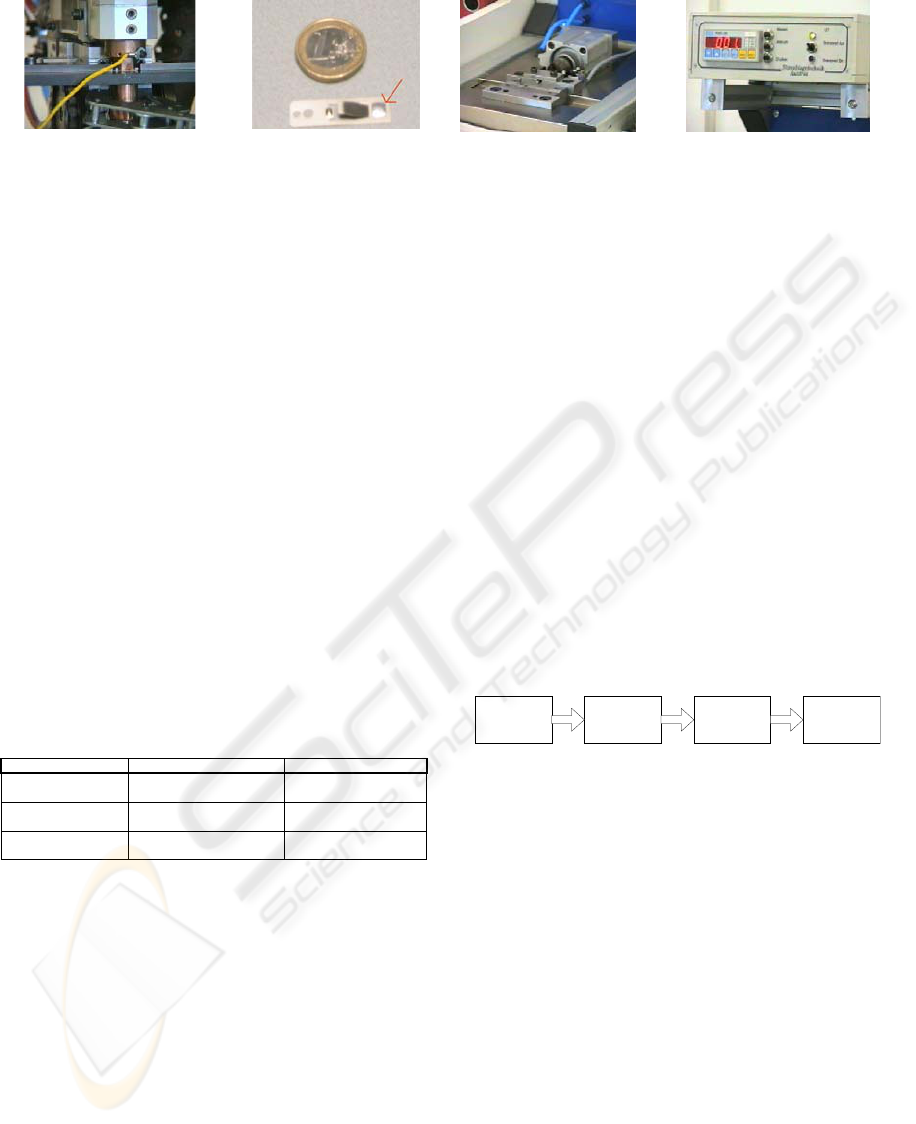
a)
b)
c)
d)
Figure 1: a) metal objects are joined using resistance spot welding, b) the welded part, c) the welding joint is torn apart in
a destructive test by a quality assurance device, d) tensile strength is shown on the screen of the quality assurance device.
experiments). The materials can be seen in Table 1.
The experiments were done by welding two metal
objects together and after that tearing the objects
apart in a destructive test (Figure 1). Each of the
observations contains measurements of current and
voltage signals recorded during and the tensile
strength of the spot measured after the welding.
The resistance curve, derived from the voltage
and current signals, contains the necessary
information for comparing the processes. Since it
was not feasible to train a SOM with all the data
points of a signal curve, suitable features were
extracted. Every resistance signal was divided into
ten parts of equal length, and their averages were
chosen as features. However, the whole feature set
was not used, but the number of features was
reduced to avoid cross-correlation and to eliminate
overlap. Furthermore, the data were divided into
training and test data sets, which consisted of 80 and
20 percent of the data, respectively.
In this work, the quality criterion was given as
tensile strength, and the distribution of quality
varied. For example, the quality limit for SBT 1 was
160 N, while for SBT 3 it was 550N.
Table 1: The materials used
Test series Base material Contact material
SBT 1, SBT 2 0.18mm Stainless steel Silver nickel
0.5x0.9mm
2
SBT 3, SBT 4 (Time
variation)
0.18mm Nickel-Beryllium
Stainless steel
Silver nickel
0.5x0.9mm
2
SBT 5 0.18mm Nickel-Beryllium Silver nickel
0.7x1.5x2.3mm
3
3 METHOD
The self-organizing map is a method that visualizes
high-dimensional data in a two-dimensional space.
This is done by keeping the topologic and metric
relations of the two-dimensional space as close as
possible to the relations of the initial space.
The SOM is usually formed of neurons on a
regular low-dimensional grid. The neurons are
model vectors m
i
=[m
i1
, m
i2
, … , m
in
], where n is the
dimension of the input space. The training is done
iteratively by choosing a data sample x and finding
the closest model vector m
c
(best-matching unit).
When the best-matching unit is found, it and its
closest neighbors are updated with the equation
m
i
(t+1) = m
i
(t) + α(t)h
ci
(t)(x(t) - m
i
(t)),
where α(t) is the learning rate factor and h
ci
(t) is the
neighborhood kernel centered on the winner unit c.
In this study, the SOM Toolbox, a function package
for Matlab implementing the Self-Organizing Map
algorithm, was used (HUT). For more information
on SOMs, (Kohonen) is recommended.
4 RESULTS
The study was divided into two phases: process
identification and search for initialization
parameters. The features selected were generally the
same in both cases, but the effect of welding time
was ignored when searching for the initialization
parameters, because it was the same inside process.
A strategy for deploying the results is presented
in Figure 2 and a case study of the implementation is
presented in the following chapters.
1) SOM
containing all
the processes
2) Process
identification
4) Return
parameters
leading to good
quality
3) SOM formed
for the states of
an individual
process
Figure 2: Steps for deploying the results.
4.1 Process identification
Figure 3a) shows a trained SOM. The division into 5
regions can be seen from the U-matrix. Now, the
division given by the SOM is researched in more
detail, because it is not yet certain that the different
regions in the map contain information from
different processes.
In Figure 3b), the spots of the 5 test series are
labeled with the numbers 1-5. These labels are
assigned to the map elements representing the curves
belonging to the corresponding cluster. From Figure
3b), it can be seen that all the regions visible in the
U-matrix contain only different processes. However,
the division in the lower part of the map only points
out the differences inside the processes 1 and 2,
which are thought to be similar processes and it is
therefore not considered as an important division.
The identification of different processes with this
RESISTANCE SPOT WELDING PROCESS IDENTIFICATION AND INITIALIZATION BASED ON
SELF-ORGANIZING MAPS
297