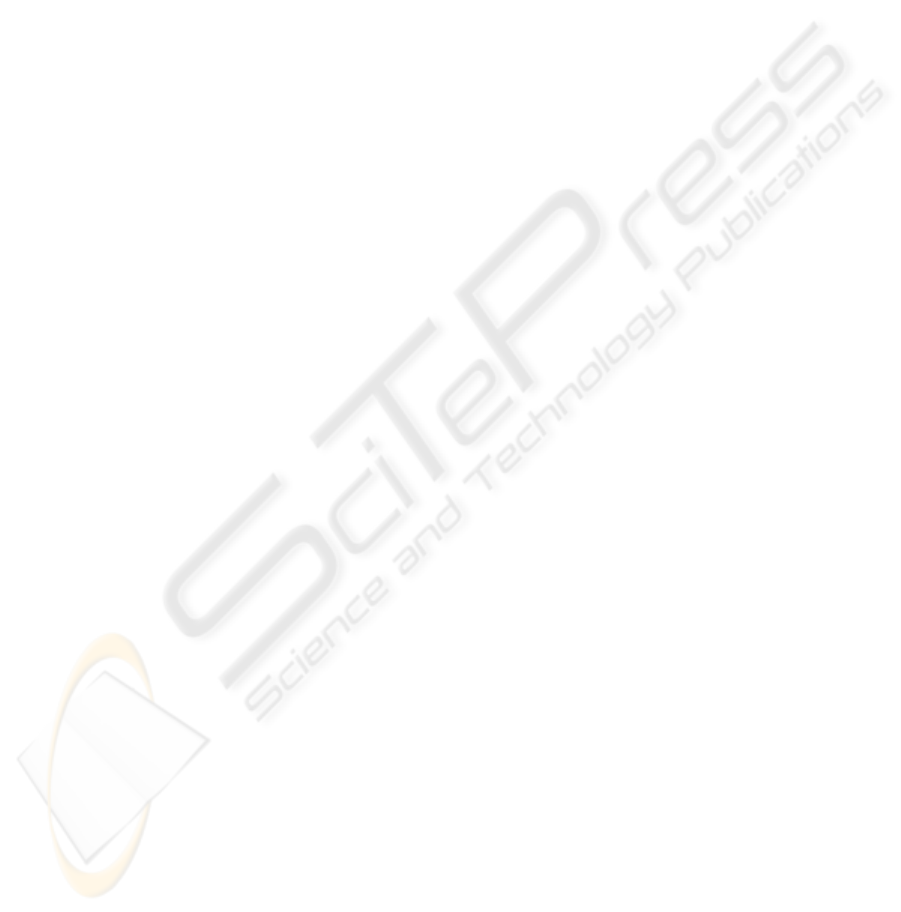
facilitates many useful advanced functions to be
developed, including control system verification,
HIL testing, monitoring by “playback” and model-
based fault detection, etc.
This paper has pointed out the importance of a
real-time communication framework that provides a
highly flexible communication mechanisms among
different sub-models and other system components,
possibly developed using a variety of tools running
on a distributed platform. RTI’s NDDS has been
selected as the suitable real-time networking
middleware for the development of the underlying
communication framework. Based on the publish-
subscribe model, NDDS provides many-to-many
communications to happen anonymously with
network location transparency, which are essential to
the implementation of connectors – the concept
introduced for maintenance specialists to define
multiple monitoring and fault detection scenarios by
flexibly connecting multiple sub-models,
algorithmic modules and data analysis tools. Future
publications will focus on the dynamics modelling
techniques and fault-detection algorithms for the
real-world industrial test cases within MASSIVE.
ACKNOWLEDGEMENTS
The authors gratefully acknowledge the Knowledge
Foundation (KK Stiftelsen), Sweden, and other
industrial participants, including AP&T, DELFOi,
Euromation, Volvo Cars and Volvo Powertrain, for
the provision of the research funding and their
collaborative input to the MASSIVE project. We
would also like to acknowledge Real-Time
Innovations for the grant of NDDS through our
participation in their University Program.
REFERENCES
Adolfsson, J., Ng, A. H. C. and Moore, P. R. (2000)
Modular machine system design using graphical
simulation. In Proceedings of the 33rd CIRP
International Seminar on Manufacturing Systems, 5-7
June, Stockholm, Sweden, pp 335-340.
Chen, J. and Patton, R. J. (1999), Robust model-based
fault diagnosis for dynamic systems, Kluwer
Academic Publishers, Dordrecht.
DELMIA (2003) IGRIP/Envision & QUEST D5 Release
12, Dassault Systemes, http://www.delmia.com.
Dépincé, P., Peer-Oliver, W. and Michael, Z. (2003)
Virtual Manufacturing, MANTYS - Thematic
Technology Trend Report.
Groll, F. (2002) Process visualization and optimization
with modern software tools. In Proceedings of the
International Symposium on Robotics, 7-11 October,
Stockholm, Sweden, pp. 193-197.
IEC 61131-3 (1993) Programmable controllers - Part 3:
programming languages, International
Electrotechnical Commission.
Isermann, R. and Ballé, P. (1997) Trends in the
application of model-based fault detection and
diagnosis of technical process, Control Engineering
Practice, 5 (5), pp. 709-719.
Lewis, R. (2001) Modelling control systems using IEC
61499, The Institution of Electrical Engineers,
London, United Kingdom.
Ljung, L. (1999). System identification: Theory for the
user, Prentice-Hall, Englewood, Cliffs, New Jersey.
Moore, P. R., Pu, J., Ng, A. H. C., Wong, C. B., Chong, S.
K., Adolfsson, J., Olofsgård, P. and Lundgren, J.-O.
(2003) Virtual Engineering: An integrated approach to
agile manufacturing machinery design and control,
Journal of Mechatronics, 13, pp. 1105-1121.
Nelles, O. (2001) Nonlinear system identification,
Springer-Verlag, Berlin, Heidelberg.
OPC Foundation (2003) http://www.opcfoundation.org.
Pardo-Castellote, G., Schneider, S. and Hamilton, M.
(1999) NDDS: The real-time publish-subscribe
middleware, Real-Time Innovations whitepaper,
http://www.rti.com.
Sundberg, M., Ng, A. H. C. and de Vin, L. J. (2003)
Distributed modular logic controllers for modular
conveyor systems. In Proceedings of the 20th
International Manufacturing Conference, Cork,
Ireland, pp. 493-500.
VIR-ENG (2001) Integrated design, simulation and
distributed control of agile modular manufacturing
machinery (VIR-ENG) ESPRIT Framework IV 25444,
final report, Final report, June.
Wolfram, A. and Isermann, R. (2002) Component based
tele-diagnosis approach to a textile machine, Control
Engineering Practice, 10, pp. 1251-1257.
AN INTEGRATED ENVIRONMENT FOR MACHINE SYSTEM SIMULATION, REMOTE MONITORING AND
FAULT DETECTION
157