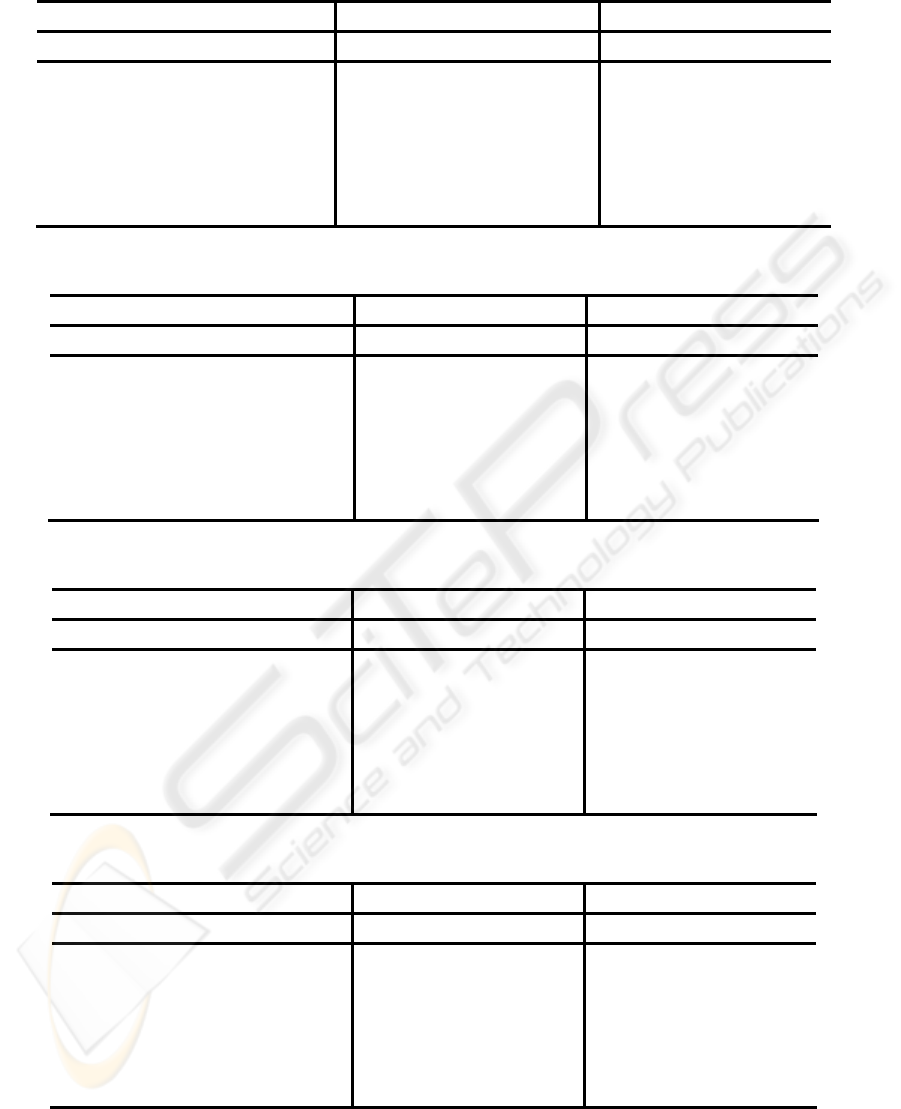
Table 3: Average of the initial and final number of setups and number of tool switches for the dispatching rules, with Tabu
List size set in 100 position and considering only the machine setup.
Initial Solutions Batch swap Batch insertion
Istn std issn std fstn std fssn std fstn std fssn std
FAM 40,4 4,22 21,9 2,23 39,5 4,99 20 2,75 39,8 4,92 39,8 4,92
LPTF 198,1 13,16 82,9 2,47 52,4 8,13 20,7 2,83 50,8 7,21 50,8 7,21
MDR 214,5 15,57 86,6 1,17 50,1 6,38 21,1 2,96 49 8,87 49 3,03
PMSR 28,1 2,64 20,5 2,55 27,9 3,21 19,6 3,03 27,9 3,40 27,9 3,35
RAN 200,5 13,54 77,7 20,39 49,6 8,47 20,4 2,67 49,8 8,07 49,8 2,62
Table 4: Average of the initial and final number of setups and number of tool switches for the dispatching rules, with Tabu
List size set in 10 position and considering only the tool switches.
Initial Solutions Batch swap Batch insertion
istn std issn std fstn Std fssn std fstn std fssn std
FAM 40,4 4,22 21,9 2,23 34,8 3,77 20 2,79 32,7 2,31 20,1 2,69
LPTF 198,1 50,41 82,9 2,47 40,8 7,83 23,1 5,00 32,3 2,11 20,4 2,41
MDR 214,5 15,57 86,6 1,17 38,7 3,92 22,2 3,16 32,3 2,58 20,2 2,86
PMSR 28,1 2,64 20,5 2,55 26,9 3,11 19,8 2,86 26,6 2,88 19,6 3,03
RAN 200,5 13,54 84 2,21 41,1 7,02 22,5 3,72 33,6 2,55 20,2 2,82
Table 5: Average of the initial and final number of setups and number of tool switches for the dispatching rules, with Tabu
List size set in 50 position and considering only the tool switches.
Initial Solutions Batch swap Batch insertion
istn std issn std fstn std fssn std fstn std fssn std
FAM 40,4 4,22 21,9 2,23 34,1 3,45 20 2,79 31,5 2,59 19,9 2,69
LPTF 198,1 50,41 82,9 2,47 37,9 5,09 21,6 2,80 31,9 2,56 20,1 2,81
MDR 214,5 15,57 86,6 1,17 37,7 4,06 21,7 3,16 30,7 2,91 19,7 2,98
PMSR 28,1 2,64 20,5 2,55 26,9 3,11 19,8 2,86 26,3 2,87 19,6 3,03
RAN 200,5 13,54 84 2,21 37,8 6,11 21,3 2,75 33 2,49 20,2 2,82
Table 6: Average of the initial and final number of setups and number of tool switches for the dispatching rules, with Tabu
List size set in 100 position and considering only the tool switches.
Initial Solutions Batch swap Batch insertion
Istn std issn std fstn std fssn std fstn std fssn std
FAM 40,4 4,22 21,9 2,23 34,2 3,46 20 2,79 30,9 3,28 19,9 2,69
LPTF 198,1 50,41 82,9 2,47 37,1 3,51 21,2 2,44 31,8 2,57 20,1 2,81
MDR 214,5 15,57 86,6 1,17 37,4 4,01 21,3 3,16 31 2,49 19,8 2,82
PMSR 28,1 2,64 20,5 2,55 26,9 3,11 19,7 2,98 26,7 3,23 20,3 3,40
RAN 200,5 13,54 84 2,21 37,9 7,19 21,1 2,69 33,2 2,49 20,2 2,82
ICINCO 2004 - INTELLIGENT CONTROL SYSTEMS AND OPTIMIZATION
24