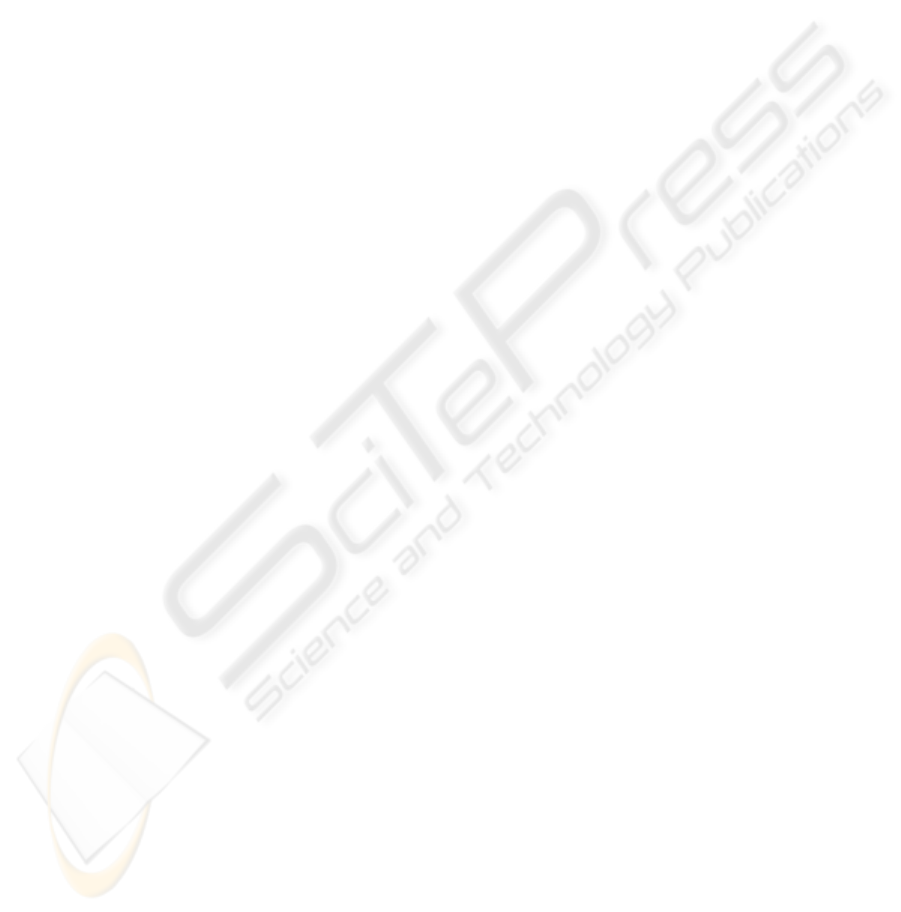
the cost function to be minimized and finally to
numerous constraints to be simultaneously
respected. The OFMPP is originally an optimal
control one and has been transformed into a
parametric optimization problem. The optimization
parameters are time transfer T and the position of
nodes defining the shape of joint variables. The
research of T has been separated from that of the
others parameters in order to make the computing
process efficient and to handle constraints easily by
transforming them into explicit bounds on T possible
values. In fact, the various possible constraints have
been regrouped in four families according to their
possible effects on T values and then have been
handled sequentially during each optimization step.
Nodes, defining q(x) shape, are connected by cubic
spline functions and their positions are perturbed
inside a stochastic process until the objective
function value is sufficiently reduced while all
constraints are all satisfied. This ensured smoothness
of resulted profiles. The objective function has been
written under a weighting form permitting to make
balance between reducing T and magnitude of
implied torques.
Numerical examples, where a stochastic
optimization process, implementing the proposed
approach, has been used along with cubic spline
approximations, and dealing with complex
problems, such as those involving discontinuous
friction efforts and obstacle avoidance, have been
presented to show the efficiency of this technique.
Others successful tests have been made in parallel
for complex robotic architectures, like biped robots,
will be presented in a future paper.
ACKNOWLEDGEMENTS
We thank Prof. H. E. Lehtihet for his suggestions
and helpful discussions.
REFERENCES
Angeles J., 1997, Fundamentals of robotic mechanical
systems. Theory, methods, and algorithms,” Springer
Edition.
Barraquand J., Langlois B., Latomb J. C., 1992, Numerical
Potential Field Techniques for robot path planning,
IEEE Tr. On Sys., Man, and Cyb., 22(2):224-241.
Barraquand J., Kavraki L., Latombe J. C., Li T. Y.,
Motwani R., Raghavan P., 1996, A random Sampling
Scheme for path planning, 7
th
Int. conf. on Rob.
Research ISRR.
Bobrow J.E., Dubowsky S., Gibson J.S., 1985, Time-
Optimal Control of robotic manipulators along
specified paths, The Int. Jour. of Rob. Res., 4 (3), pp.
3-16.
Bessonnet G., 1992, Optimisation dynamique des
mouvements point à point de robots manipulateurs,
Thèse d’état, Université de Poitiers, France.
Betts J. T., 1998, Survey of numerical methods for
trajectory optimization, J. Of Guidance, Cont. & Dyn.,
21(2), 193-207.
Chen Y., Desrochers A., 1990, A proof of the structure of
the minimum time control of robotic manipulators
using Hamiltonian formulation, IEEE Trans. On Rob.
& Aut. 6(3), pp388-393.
Chettibi T., 2000, Contribution à l'exploitation optimale
des bras manipulateurs, Magister thesis, EMP,
Algiers, Algeria.
Chettibi T., 2001a, Optimal motion planning of robotic
manipulators, Maghrebine Conference of Electric
Engineering, Constantine, Algeria.
Chettibi T., Yousnadj A., 2001b, Optimal motion planning
of robotic manipulators along specified geometric
path, International Conference on productic, Algiers.
Chettibi T., Lehtihet H. E., 2002a, A new approach for
point to point optimal motion planning problems of
robotic manipulators, 6th Biennial Conf. on
Engineering Syst. Design and Analysis (ASME ),
Turkey, APM10.
Chettibi T., 2002b, Research of optimal free motions of
manipulator robots by non-linear optimization,
Séminaire international sur le génie Mécanique, Oran,
Algeria.
Danes F., 1998, Critères et contraintes pour la synthèse
optimale des mouvements de robots manipulateurs.
Application à l’évitement d’obstacles, Thèse d’état,
Université de Poitiers.
Dombre E. & Khalil W., 1988, Modélisation et commande
des robots, First Edition, Hermes.
Fletcher R., 1987, Practical methods of optimization,
Second Edition, Wiley Interscience Publication.
Garber M., Lin. M.C., 2002, Constrained based motion
planning for virtual prototyping, SM’02, Germany.
Glass K., Colbaugh R., Lim D., Seradji H., 1995, Real
time collision avoidance for redundant manipulators,
IEEE Trans. on Rob. & Aut., 11(3), pp 448-457.
Hull D. G., 1997, Conversion of optimal control problems
into parameter optimization problems, J. Of Guidance,
Cont. & Dyn., 20(1), 57-62.
Jaques J., Soltine E., Yang H. S., 1989, Improving the
efficiency of time-optimal path following algorithms,
IEEE Trans. on Rob. & Aut., 5 (1).
Kang G. S., McKay D. N., 1986, Selection of near
minimum time geometric paths for robotic
manipulators, IEEE Trans. on Aut. & Contr., AC31(6),
pp. 501-512.
Kavraki L., Latombe J. C., 1994, Randomized
Preprocessing of Configuration Space for Fast Path
Planning, Proc. Of IEEE Int. Conf. on Rob. & Aut., pp.
2138-2139, San Diego.
Kavraki L., Svesta P., Latombe J. C., Overmars M., 1996,
Probabilistic Roadmaps for Path Planning in High
Dimensional Configuration space, IEEE trans. Robot.
Aut., 12:566-580.
A STOCHASTIC OFF LINE PLANNER OF OPTIMAL DYNAMIC MOTIONS FOR ROBOTIC MANIPULATORS
127