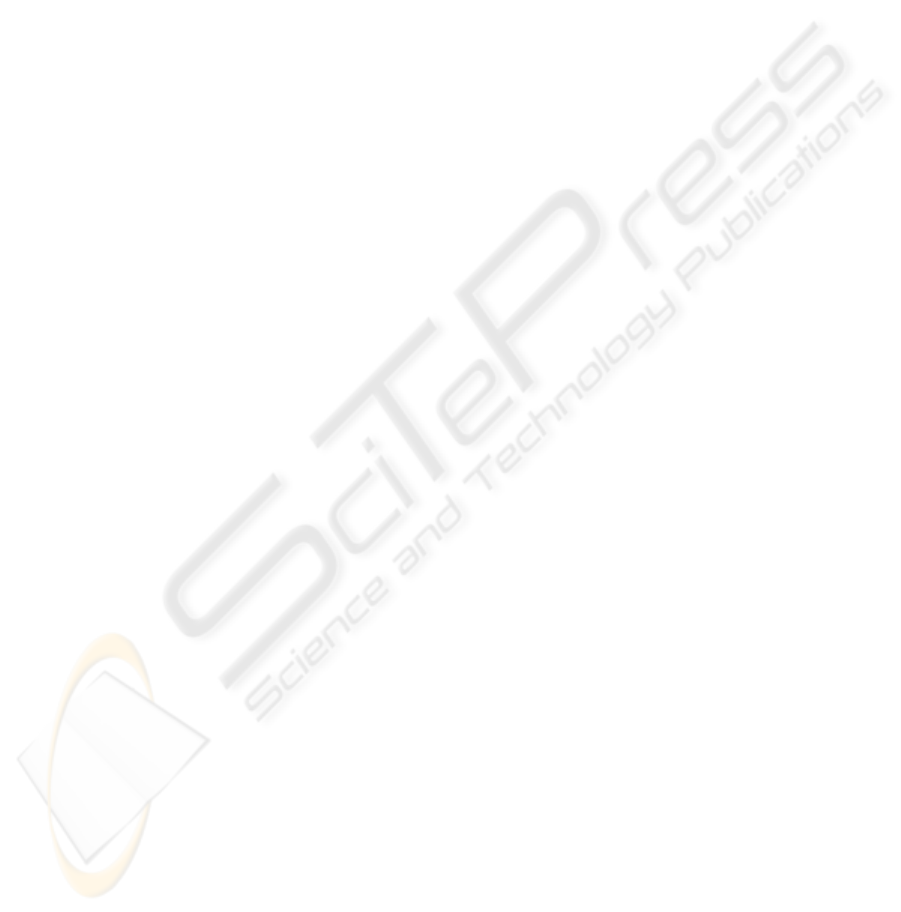
POSITION CONTROL OF AN ELECTRO-HYDRAULIC
SERVOSYSTEM
A non-linear backstepping approach
Claude Kaddissi, Jean-Pierre Kenné, Maarouf Saad
École de Technologie Supérieure, 1100 Notre-Dame West street, Quebec H3C 1K3, Canada
Keywords: Electro-hydraulic systems modeling, Non-linear control, Backstepping.
Abstract: This paper studies the control of an electro-hydraulic servosystem using a non-linear backstepping based
approach. These systems are known to be highly non-linear due to many factors as leakage, friction and
especially the fluid flow expression through the servo-valve. Another fact, often neglected or avoided, is
that such systems have a non-differentiable mathematical model for bi-directional applications. All these
facets are pointed out in the proposed model of this paper. Therefore, the control of this class of systems
should be based on non-linear strategies. Many experiments showed the failure of classic control with
electro-hydraulic systems, unless operating in the neighborhood of a desired value or reference signal. The
backstepping is used here to overcome all the non-linear effects. The model discontinuity is solved in this
paper, by approximating the non-differentiable function by a sigmoid, so that the backstepping could be
used without restrictions. In fact, simulation results show the effectiveness of the proposed approach in
terms of guaranteed stability and zero tracking error.
1 INTRODUCTION
An electro-hydraulic system is composed of multiple
components: A pump, which feeds the system with
fluid oil from an oil container; An accumulator,
which acts as an auxiliary of energy integrated in the
hydraulic circuit; A relief valve on the other hand to
compensate the increase of pressure if any; A
hydraulic actuator to drive a given load at a desired
position, its displacement direction, speed and
acceleration are determined by a servo-valve. Note
that oil exiting the hydraulic actuator is driven
through the servo-valve back to the tank.
Electro-hydraulic systems became increasingly
current in many kinds of industrial equipments and
processes. Such applications include rolling and
paper mills, aircraft’s and all kinds of automation
including cars industry where linear movements, fast
response, and accurate positioning with heavy loads
are needed. This is principally because of the great
power capacity with good dynamic response and
system solution that they can offer, as compared to
DC and AC motors. However, as a result of the ever-
demanding complexity with these applications,
considering non-linearity and mathematical model
singularity, the traditional constant-gain controllers
have become inadequate. Lim (1997) applied simple
poles placement for a linearized model of an electro-
hydraulic system. Plahuta et al. (1997) tried a
retroaction strategy for variable displacement
hydraulic actuator and this by using two cascaded
control loops for position and speed control. Zeng
and Hu (1999) used a PDF algorithm (Pseudo-
Derivative Feedback) where the integrator part of a
PID controller was placed in the direct path.
Experiments and simulations showed that factors
resulting in dynamic variations are beyond the
capacity of these controllers. And there are also
many of these factors to take into account, such as
load variations, changes of transducers
characteristics and properties of the hydraulic fluid,
changes of servo components dynamics and other
system components, etc. As a result, many robust
and adaptive control methods have been used. Yu
and Kuo (1996) employed an indirect adaptive
controller for speed feedback, based on pole
placement. Sliding mode controller has been used by
Fink and Singh (1998), in order to regulate the
pressure drop due to the load across the actuator. On
the other hand fuzzy logic control has been
270
Kaddissi C., Kenné J. and Saad M. (2004).
POSITION CONTROL OF AN ELECTRO-HYDRAULIC SERVOSYSTEM - A non-linear backstepping approach.
In Proceedings of the First International Conference on Informatics in Control, Automation and Robotics, pages 270-276
DOI: 10.5220/0001134402700276
Copyright
c
SciTePress