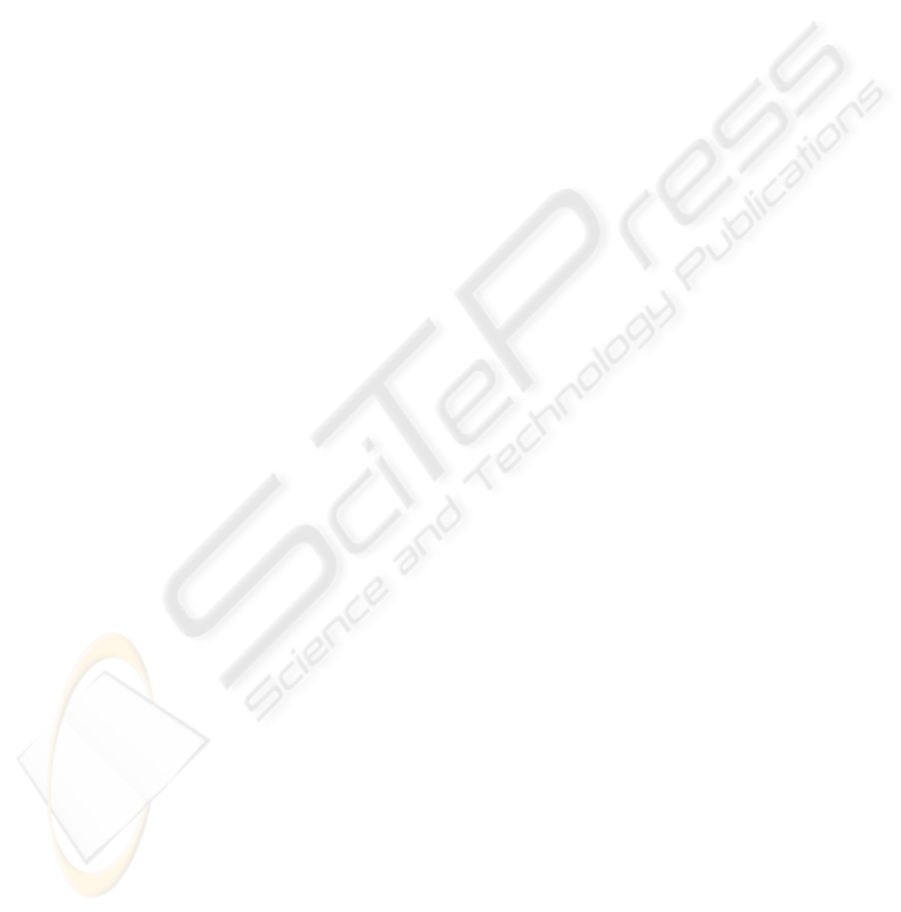
iterations is valid. To test the algorithm's behavior,
simulated movement was accelerated by factor 2, 4
and 8, while maintaining the same cycle duration of
1 ms. Only by reaching the 8-fold acceleration,
when the total movement time equals a very
unrealistic half a second, did the algorithm produce
more significant errors, while still holding to the
correct solution.
7 HEXAPOD ANALYSIS AS WEB
SERVICE
The described methods of hexapod analysis have
been implemented as Web services at
(http://hexapod.zemris.fer.hr/). Hexapod structure
can be defined through Web interface and then a
particular operation is performed. Workspace
volume can be calculated as a number representing
volume in cubic units, or drawn as VRML shape or
cross-section with horizontal or vertical plane. Error
values and kinematics values can be calculated as
overall values through all workspace or just in cross-
section with a plane.
Implementation is done through CGI programs,
PHP scripting language for Apache Web server,
currently running on a two processor Windows 2000
Server. CGI is chosen because of performance issues
since analysis methods are computationally
intensive. PHP scripts are used to collect hexapod
parameters from users and temporary store them in
session variables. Before calling CGI programs,
PHP script writes parameters to a file on a server.
CGI then reads those files, performs calculations and
produces results. Depending on demanded
calculations, results can be in HTML form, images
or VRML files. VRML format is used for displaying
hexapod models and its workspace. An implicit
surface triangulation method is used for generating
workspace. Improving and optimizing process of
this triangulation method is in progress.
To utilize multiprocessor system a multithreaded
version of program is written since computations can
be easily parallelized. Additional 15-20 percent
speedup is achieved using hyper-threading
technology of Intel Xeon processors.
Regarding speed, workspace calculation can take
up to a few minutes to complete. Kinematics is little
more time demanding, depending on chosen
operation and precision. Error analysis, in spite of
enormous effort in optimizing, is still extremely
slow and time consuming, and it can take 15 to 20
minutes or even more to compute.
8 CONCLUSION
Methods for hexapod analysis are shown, starting
with workspace calculation, error sensitivity analysis
and kinematics evaluation. A forward kinematics
algorithm designed for use in real-time environment
is presented. These methods are prepared and
implemented in a functional Web based system.
ACKNOWLEDGEMENT
This work was carried out within the research
project "Distributed Embedded Computing
Systems", supported by the Ministry of Science and
Technology of the Republic of Croatia.
REFERENCES
Patel, A.J., Ehmann, K.F., 1997. Volumetric Error
Analysis of a Stewart Platform-Based Machine Tool,
Annals of the CIRP, vol. 47/1, pp. 287-290.
Wang, S.M., Ehmann, K.F., 1995. Error Model and
Accuracy Analysis of a Six-DOF Stewart Platform,
Manufacturing Science and Eng., 2-1, pp. 519-530.
Jakobović, D., Jelenković, L., 2002. The Forward and
Inverse Kinematics Problems For Stewart Parallel
Mechanisms,
8
th
Int. Sci. Conf. Production Eng.:
CIM2002,
Brijuni, 2002, pp. II-001- II-012.
Huang, T., Whitehouse, D.J., Wang, J., 1998. The Local
Dexterity, Optimal Architecture and Design Criteria of
Parallel Machine Tools,
Annals of the CIRP, vol. 47/1,
pp.347-351.
Stoughton, R.S., Arai, T., 1993. A Modified Stewart
Platform Manipulator with Improved Dexterity,
IEEE
Trans. on Robotics and Automation
, vol. 9, no. 2, pp.
166-173.
Merlet, J.-P., 1993. Direct Kinematic of Parallel
Manipulators,
IEEE Transactions on Robotics and
Automation
, Vol. 9, No. 6, pp. 842-845
Jakobović, D., Budin, L., 2002. Forward Kinematics of a
Stewart Parallel Mechanism,
Proc. 6
th
Int. Conf. on
Intelligent Engineering Systems INES 2002
, Opatija,
May 26-28., pp.149-154
Dasgupta, B., Mruthyunjaya, T.S., 1994. A Canonical
Formulation of the Direct Position Kinematic Problem
for a General 6-6 Stewart Platform,
Mech. Mach.
Theory
, Vol. 29, No. 6, pp. 819-827,
Raghavan, M., 1993. The Stewart Platform of General
Geometry has 40 Configurations,
Journal of
Mechanical Design
, Vol. 115, pp. 277-282
Wen, F., Liang, C., 1994. Displacement Analysis of the 6-
6 Stewart Platform Mechanisms,
Mechanism and
Machine Theory
, Vol. 29, No. 4, pp. 547-557
HEXAPOD STRUCTURE EVALUATION AS WEB SERVICE
497