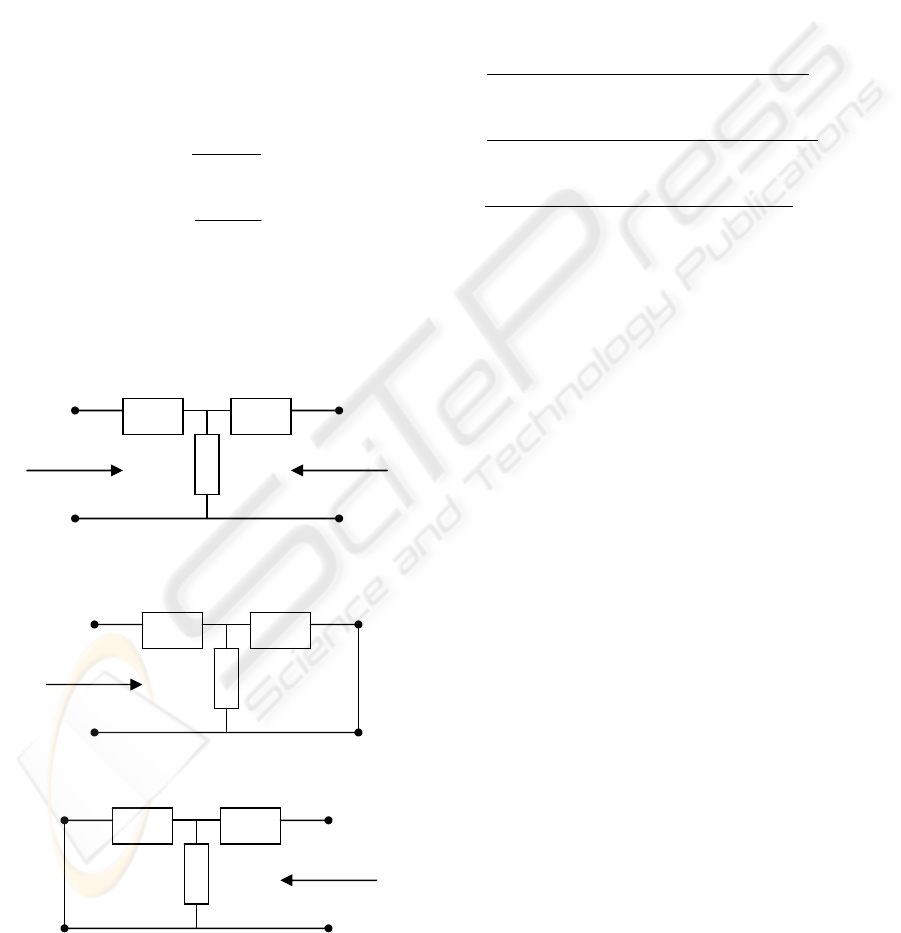
2.2 Mathematical Model
The common used mathematical model for a
resolver is shown in fig. 3, and it is the typical model
for a transformer.
This model is suitable to supply the usual
customer demanded electrical characteristics of the
resolver, namely the Rotor and Stator Impedances
(open and short circuited).
According the below schematics, using the
traditional circuit analysis methods, the following
equations are obtained:
; (2)
31ro
ZZZ +=
; (3)
32so
ZZZ +=
32
32
1rs
ZZ
ZZ
ZZ
+
+=
; (4)
31
31
2ss
ZZ
ZZ
ZZ
+
+=
; (5)
Where:
Zro = Rotor Impedance with Stator open
Zso = Stator Impedance with Rotor open
Zrs = Rotor Impedance with Stator shorted
Zss = Stator Impedance with Rotor shorted
Rotor Impedance with Stator open (Zro) and
Stator Impedance with Rotor open (Zso)
Rotor Impedance with Stator shorted (Zrs)
Stator Impedance with Rotor shorted (Zss)
Figure 3: Common used resolver models
This model although useful for computing the
main electrical characteristics for customer needs is
from less use for the sensors manufacturer. Actually
this model doesn’t copy with anyone of the directly
controllable variables in a resolver manufacture.
The new model proposed in this paper is
appropriate for resolver manufacturers because it
deals explicitly with the actually controllable
variables in a resolver production plant (mainly
winding parameters).
The main variables that influence directly the
customer specific electrical characteristics can be
divided into 3 groups:
Group 1: Material related variables: magnetic
permeability of the rotor, the stator, the rotor-
-transformer, the stator-transformer.
Group 2: Geometry related variables: stator
dimensional tolerances, rotor dimensional
tolerances, rotor/stator air-gap, transformer air-gap.
Group 3: windings related variables: windings
distribution around the rotor and the stator, number
of stator-windings, stator-windings wire diameter,
number of rotor-windings, rotor-windings wire
diameter, number of stator/transformer-windings,
stator/transformer-windings wire diameter, number
of rotor/transformer-windings, rotor/transformer-
windings wire diameter.
From this 3 groups of variables, the resolver
manufacturer can only influence on a feasible way
the 3
rd
variables Group, since the other groups are
usually fixed for the sensor manufacturer as he buys
the materials and parts from external suppliers. Even
if the resolver manufacturer is vertically integrated,
producing also its parts, what is very unusual, the
parts production pace and environment is completely
apart from the resolver assembly line, this implies
that, for having its parts, the assembly line has to
deal always with stock management (the assembly
line can never control the groups 1 and 2 related
variables).
Z
Z
In such a scenario a useful resolver mathematical
model for a resolver manufacturer must deal
explicitly with the Group 3 Variables.
In Figueiredo, 2004, an explicit mathematical
model for Pancake resolvers was proposed. This
model although very accurate has its major
application on the design of new products. For
manufacturing purposes where the main needs are
the compensation of the processes variability that
affect the product characteristics and increase the
scrap, that model has less application. In fact, those
model variables cannot be directly used by the
resolver manufacturer, as they account for the
standard physical effects of an electromagnetic
device (transformer ohmic resistances, indutances,
electromagnetic losses in windings and metal…).
These standard electromagnetic variables are very
Z
Z
Z
Roto
Stato
Z
Z
Z
Z
Z
Z
Z
Z
ICINCO 2004 - SIGNAL PROCESSING, SYSTEMS MODELING AND CONTROL
40