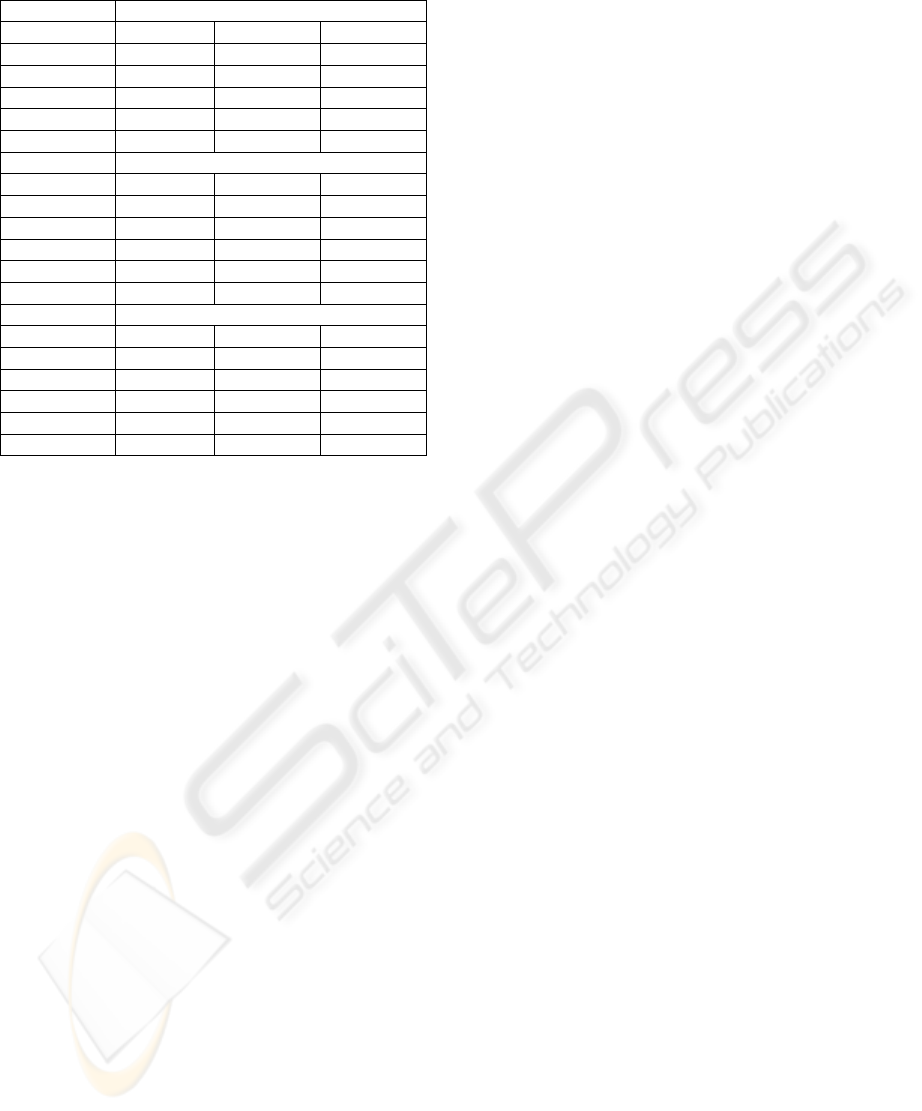
Table 2: Parameters for the memberships functions
Error membership funtion
Fuzzy State b W n
NH -3 3 8
NL -1 1 4
ZERO 0 0.5 2
PL 1 1.5 4
PH 3 2 8
Error velocity membership funtion
Fuzzy State b W n
NH -10 4 8
NL -4 2 4
ZERO 0 1 2
PL 4 2 4
PH 10 4 8
Power supply membership funtion
Fuzzy State b W n
HEI -3 3 8
LEI -1 1 4
STOP 0 0.5 2
LED 1 1 4
HED 3 3 8
In the defuzzification stage a numerical final output
value is obtained through the center-average
defuzzification method.
4 EXPERIMENTAL RESULTS
The objective of this stage is to implement the
proposed Fuzzy Logic Controller using the pilot-
plant cylinder dryer so as to control the exit web
humidity by actuating the power supplied to the
inductors.
The trial initially involved manual operating
conditions leading to a preliminary decrease in web
humidity during drying by using a cylinder
rotational speed of 1.7 rev/min., a power supply of
2.42 kW and the maximun degree of web-cylinder
surface contact (1618 cm
2
). This startup step for the
process takes about 26 min. Figure 1 shows the
operational variables measured on line during the
complete trial: the cylinder temperature and the web
humidity at the inlet of the drying section, the
temperature of the fabric at the exit of the drying
section, and the cylinder rotational speed. Once
steady–state conditions were achieved, the process
was changed to automatic mode and a set point for
the exit web humidity fixed at 20 g water/100 g dry
fabric. From this moment on, the process is under
the Fuzzy Logic Controller action.
In first stage of the process control, as shown in
Figure 2, an important increase of the power
supplied to the inductors is observed generating an
immediate increase in the cylinder temperature, and
consequently a fabric with a low exit humidity.
From these conditions of over-drying, a reduction of
the power is observed. In this early stage, the web
humidity oscillates around the set point of 20 g
water/100 g dry fabric and the controller takes
approximately 45 min. to control the exit web
humidity to the set point.
Once the set point value is attained, a step
perturbation was made changing the position of the
movable roller, decreasing the contact web-cylinder
surface. From this second stage of the trial, there is
an immediate increase of the web humidity
following a reduction in the area of web-cylinder
contact (or reduction of the drying time).
The fuzzy logic controller responds by increasing
the power supplied to the inductors but the same
previous oscillatory dynamic of the exit web
humidity is observed tending towards the set point.
In the last stage of the trial, a set point change was
made, changing the value from 20 to 10 g water/100
g dry fabric. Figure 6 shows the dynamic reponses,
for the controlled and manipulated variables and as
in the previous stages, the web humidity tends
towards the new set point
.
5 CONCLUSIONS
A Fuzzy Logic Controller was used with success to
control a complex process, like the drying of a fabric
by contact with a rotating cylinder heated by
electromagnetic induction. The performance of the
controller was tested using a pilot scale dryer and a
stable reponse was observed when the process was
perturbed with changes in the operational conditions
and in the set point for the exit web humidity.
REFERENCES
Dhib, R., 1994. Modelisation, simulation et côntrole
numérique d’un procédé de séchage par rayonnement
infrarouge, Thèse de doctorat, Université de
Sherbrooke, QC.
Jones, P.L. 1992. Electromagnetic wave energy in drying
process. In drying 92, A.S. Mujumdar, Ed. Elsevier,
Amsterdam, pp. 115-136.
Passino K.M., S. Yurkovich. 1998. Fuzzy Control,
Addison-Wesley Longman Inc., Menlo Park,
California.
Pérez S., N. Thérien and A.D. Broadbent. 2001. Modelling
the continuous drying of a thin sheet of fibres on a
cylinder heated by electric induction. Can. J. Chem.
Eng. 79, 977-989.
ICINCO 2004 - INTELLIGENT CONTROL SYSTEMS AND OPTIMIZATION
336