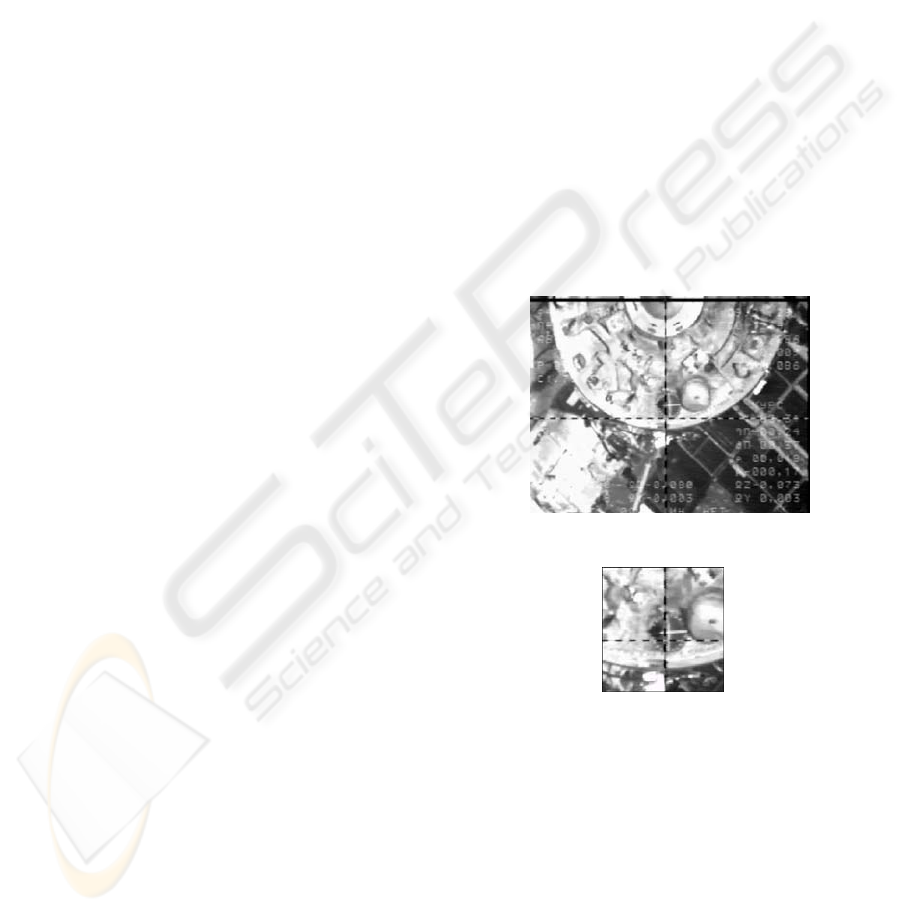
relative location definition. The TV-signal is
inputted into computer with the help of the
framegrabber. Besides that, the opportunity of the
processing already digitizing of sequences of the avi
format images is stipulated. All complex is realized
in OS Windows 98-XP.
An ultimate goal of the complex development is
a complete automation of the visual monitoring of
SC and ISS docking approach from the moment of
ISS visibility in the TV-camera field of view (about
500 m) and up to the complete SC and ISS docking.
In the basic integrated steps - stages of the
acquisition and processing of the visual data the
complex works similarly to the operator - person.
The complex in addition (in relation to the
person - operator) calculates and displays in the
kind, accepted for the analysis, parameters
describing the docking process.
This research work was partially financed by the
grants of the RFFI ## 02-07-90425, 02-01-00671,
MK-3386.2004.9 and the Russian Science Support
Foundation.
2 MEASURING SUBSYSTEM
The purpose of this software subsystem is the
extraction of the objects of interest from the images
and performance of measurements of the points’
coordinates and sizes of these objects. To achieve
this purpose it is necessary to solve four tasks:
1) Extraction of the region of interest (ROI)
position on the current image.
2) Preprocessing of the visual data inside the
ROI.
3) Extraction (recognition) of the objects of
interest.
4) Performing of the measurements of the sizes
and coordinates of the recognized objects.
All the listed above operations should be
performed in real time. The real time scale is
determined by the television signal frame rate. The
other significant requirement is that in the
considered software complex it is necessary to
perform updating of the spacecraft motion
parameters with a frequency of no less than 1 time
per second.
For reliability growth of the objects of interest
the extraction from the images of the following
features are provided:
1) Automatic adjustments of the brightness and
contrast of the received images for the optimal
objects of interest recognition.
2) Use of the objects of interest features of the
several types. Such features duplication (or even
triplication) raises reliability of the image processing
when not all features are well visible.
3) Self-checking of the image processing results
on a basis of the a priori information about the
observed scenes structure.
The ways of performing the calculation of the
ROI position on the current image are:
1) Calculation of the ROI coordinates (fig. 1) on
the basis of the external information (for example,
with taking into account a scene structure or by the
operator selection).
2) Calculation of the ROI coordinates and sizes
on the basis of the information received from the
previous images processing.
The second (preprocessing) task is solved on the
basis of the histogram analysis. This histogram
describes a brightness distribution inside the ROI.
The brightness histogram should allow the reliable
transition to the binary image. In the considered task
the brightness histogram is approximately bimodal.
The desired histogram shape is provided by the
automatic brightness and contrast control of the
image source device.
(a)
(b)
Figure 1: An example of the ROI positioning in the
spacecraft TV-camera field of view. a) Full image of the
field of view; b) The ROI image.
At the third processing stage the extraction of the
objects of interest is performed. These objects are
the station contour, the docking unit disk, the target
cross and the target disk with small labels. The main
features are the station contour, the cross and the
target labels. These features are considered the main
structured elements of the recognized scene and
used for measurement. At features extraction both
edge-based (Canny, 1986; Mikolajczyk et al., 2003)
ICINCO 2004 - ROBOTICS AND AUTOMATION
80