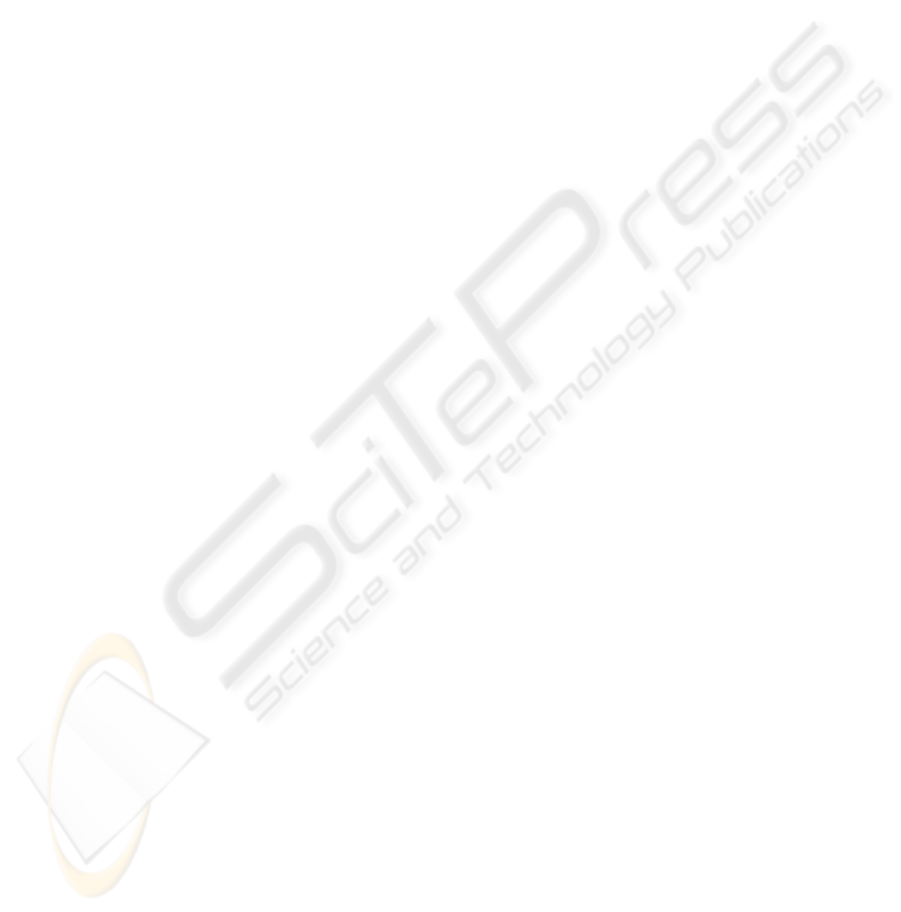
3 ISIAC
ISIAC is primarily meant to support the model-based
predictive multivariable controller MVAC, a part of
the APC suite developed by IFP and its affiliate RSI.
MVAC has first been validated on a challenging
pilot process unit licensed by IFP (Couenne et al.,
2001), and is currently under application in several
refineries world-wide. Its main features are:
• state-space formulation;
• observer to take into account unmeasured distur-
bances, intermediate variables, integrating behav-
ior;
• ranked soft and hard constraints;
• advanced specification of trajectories (funnels, set-
ranges);
• static optimization of process variables.
Though ISIAC is intended to be the natural com-
panion tool to MVAC, it is actually flexible enough
to be used as a full-fledged system identification and
model building tool or to support other APC pack-
ages.
3.1 Approaches to model estimation
The model estimation approaches selected for inclu-
sion in ISIAC combine accuracy and feasibility, both
in term of computational requirements and of user
choices. We have decided to favor non-iterative meth-
ods over prediction error methods (Ljung, 1999),
to avoid problems originating from a demanding
minimization routine and a complicated underlying
parametrization.
3.1.1 Two-stage method
The benefits of high-order ARX estimation in indus-
trial situations have been advocated by several re-
searchers ((Zhu, 2001; Rivera and Jun, 2000)). In-
deed, using a model order high enough, and with
sufficiently informative data, ARX estimation yields
models that can approximate any linear system arbi-
trarily well (Ljung, 1999). Ljung’s asymptotic black-
box theory also provides (asymptotic) expressions for
the transfer function covariance which can be used for
model validation purposes.
A model reduction step is necessary to use these
models as process control models, since they usually
are over-parameterized (i.e., an unbiased model with
much lower order can be found) and have high vari-
ance (which is roughly proportional to model order).
Different schemes have been proposed ((Hsia, 1977;
Wahlberg, 1989; Zhu, 1998; Rivera and Jun, 2000;
Tj
¨
arnstr
¨
om and Ljung, 2003)) to perform model re-
duction. For a class of reduction schemes (Tj
¨
arnstr
¨
om
and Ljung, 2003), it has been demonstrated that the
reduction step actually implies variance reduction,
and a resulting variance which is nearly optimal (that
is, close to the Cramer-Rao bound).
In ISIAC, truly multi-input multi-output (MIMO)
ARX estimation is possible, using the structure
A(q)y(t) = B(q)u(t) + e(t)
where y(t) is the p-dimensional vector of outputs
at time t, u(t) is the m-dimensional vector of in-
puts at time t, e(t) is a p-dimensional white noise
vector, A(q) and B(q) polynomial matrices respec-
tively of dimensions p × p and p × m. For faster
results, in the two-stage method, the least-square es-
timation problem is decomposed into p multi-input
single-output (MISO) problems. The Akaike infor-
mation criterion (AIC) (Ljung, 1999) is used to find
a “high enough” order in the first step, and the re-
sulting model is tested for unbiasedness (whiteness
of the residuals and of the inputs-residuals cross-
correlation). To find a reduced order model, we adopt
a frequency-weighted balanced truncation (FWBT)
technique (Varga, 1991). The calculated asymptotic
variance is used to set the weights and to automat-
ically choose the order of the reduced model, fol-
lowing an approach inspired by (Wahlberg, 1989).
The obtained model is already in the state-space form
needed by the MPC algorithm.
As a result, we get an estimation method which
is totally automated, and provides accurate results in
most practical situations, with both open-loop and
closed-loop data. Yet, this method might not work
correctly when dealing with short data sets and (very)
ill-conditioned systems.
3.1.2 Automated subspace estimation
The term subspace identification methods (SIM)
refers to a class of algorithms whose main charac-
teristic is the approximation of subspaces generated
by the rows or columns of some block matrices of
the input/output data (see (Bauer, 2003) for a recent
overview). The underlying model structure is a state-
space representation with white noise (innovations)
entering the state equation through a Kalman filter
and the output equation directly
x(t + 1) = Ax(t) + Bu(t) + Ke(t)
y(t) = Cx(t) + Du(t) + e(t)
Simplifying (more than) a bit a fairly complex theory,
input and output data are used to build an extended
state-space system, where both data and model infor-
mation are represented as matrices, and not just vec-
tor and matrices. Kalman filter state sequences are
then identified and used to estimate system matrices
A, C, and, if a disturbance model is needed, K (B and
D can be subsequently estimated in several different
ICINCO 2004 - SIGNAL PROCESSING, SYSTEMS MODELING AND CONTROL
88