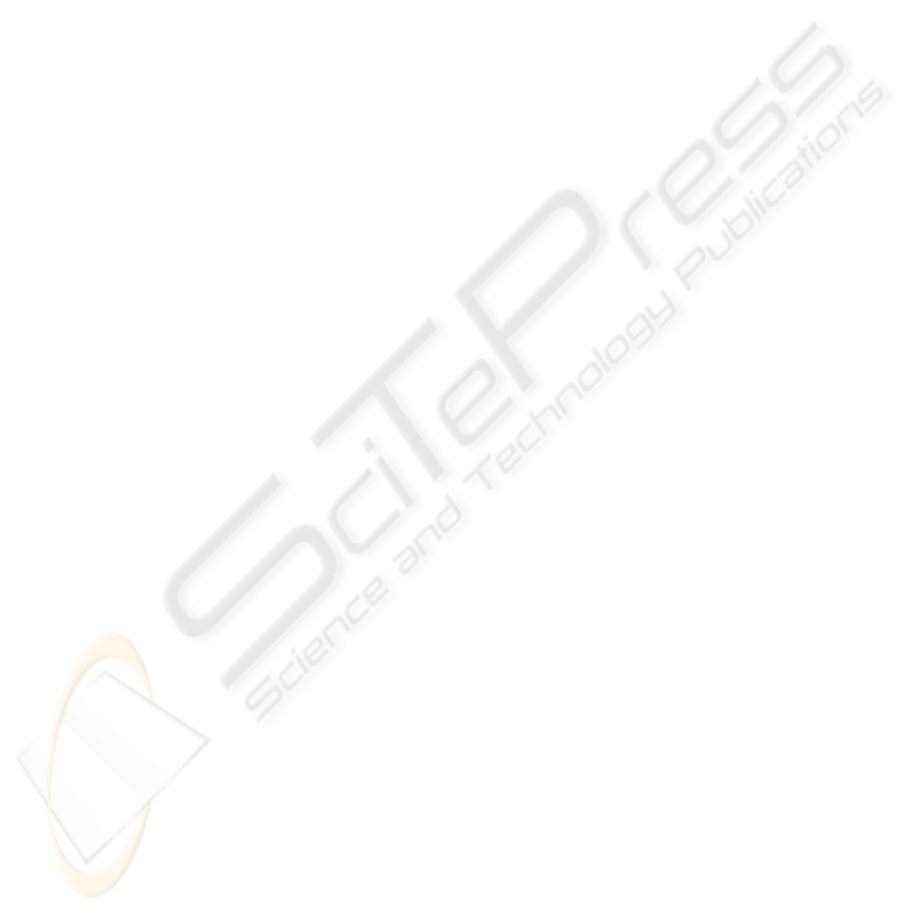
this procedure five times in clockwise direction and
five times in counter-clockwise. The measure of dead
reckoning accuracy for systematic errors that we ob-
tained is E
max,syst
= 114 mm, which is compara-
ble with those achieved by other dead reckoning sys-
tems (Borenstein and Feng, 1996).
6 RELATED WORKS
As we said in Section 1, Mobile Robot Position-
ing has been one of the first problem in Robotics
and odometry is the most widely used navigation
method for mobile robot positioning. Classical odom-
etry methods based on dead reckoning are inexpen-
sive and allow very high sample rates providing good
short-term accuracy. Despite its limitations, many re-
searcher agree that odometry is an important part of
a robot navigation system and that navigation tasks
will be simplified if odometric accuracy could be im-
proved.
The fundamental idea of dead reckoning is the inte-
gration of incremental motion information over time,
which leads inevitably to the unbounded accumula-
tion of errors. Specifically, orientation errors will
cause large lateral position errors, which increase pro-
portionally with the distance traveled by the robot.
There have been a lot of work in this field especially
for differential drive kinematics and for systematic er-
ror measurement, comparison and correction (Boren-
stein and Feng, 1996).
First works in odometry error correction were
done by using and external compliant linkage vehicle
pulled by the mobile robot. Being pulled this vehicle
does not suffer from slipping and the measurement
of its displacing can be used to correct pulling robot
odometry (Borenstein, 1995). In (Borenstein and
Feng, 1996) the authors propose a practical method
for reducing, in a typical differential drive mobile
robot, incremental odometry errors caused by kine-
matic imperfections of mobile encoders mounted onto
the two drive motors.
Little work has been done for different kinemat-
ics like the ones based on omnidirectional wheels. In
these cases, slipping is always present during the mo-
tion and classical shaft encoder measurement leads
to very large errors. In (Amini et al., 2003) the Per-
sia RoboCup team proposes a new odometric system
which was employed on their full omni-directional
robots. In order to reduce non-systematic errors,
like those due to slippage during acceleration, they
separate odometry sensors from the driving wheels.
In particular, they have used three omni-directional
wheels coupled with shaft encoders placed 60
o
apart
of the main driving wheels. The odometric wheels are
connected to the robot body through a flexible struc-
ture in order to minimize the slippage and to obtain a
firm contact of the wheels with the ground. Also this
approach is independent from the kinematics of the
robot, but its realization is quite difficult and, how-
ever, it is affected by (small) slippage problems.
An optical mouse was used in the localization sys-
tem presented in (Santos et al., 2002). In their ap-
proach, the robot is equipped with an analogue com-
pass and an optical odometer made out from a com-
mercially available mouse. The position is obtained
by combining the linear distance covered by the robot,
read from the odometer, with the respective instanta-
neous orientation, read from the compass. The main
drawback of this system is due to the low accuracy of
the compass which results in systematic errors.
However, odometry is inevitably affected by the
unbounded accumulation of errors. In particular, ori-
entation errors will cause large position errors, which
increase proportionally with the distance travelled by
the robot. There are several works that propose meth-
ods for fusing odometric data with absolute position
measurements to obtain more reliable position esti-
mation (Cox, 1991; Chenavier and Crowley, 1992).
7 CONCLUSIONS
We have presented a dead reckoning sensor based on
a pair of optical mice. The main advantages are good
performances w.r.t. the two main problems that affect
dead reckoning sensors: slipping and crawling. On
the other hand, this odometric system needs that the
robot operates on a ground with a surface on which
the mice always read with the same resolution.
Due to its characteristics, the proposed sensor can
be successfully applied with many different robot ar-
chitectures, being completely independent from the
specific kinematics. In particular, we have developed
it for our omnidirectional Robocup robots, which will
be presented at Robocup 2004.
REFERENCES
Agilent Technologies Semiconductor Products Group
(2001). Optical mice and hiw they work: The optical
mouse is a complete imaging system in a tiny pack-
age. Technical Report 5988-4554EN, Agilent Tech-
nologies Inc.
Agilent Technologies Semiconductor Products Group
(2003). Agilent adns-2051 optical mouse sesor data
sheet. Technical Report 5988-8577EN, Agilent Tech-
nologies Inc.
Amini, P., Panah, M. D., and Moballegh, H. (2003). A new
odometry system to reduce asymmetric errors for om-
DEAD RECKONING FOR MOBILE ROBOTS USING TWO OPTICAL MICE
93