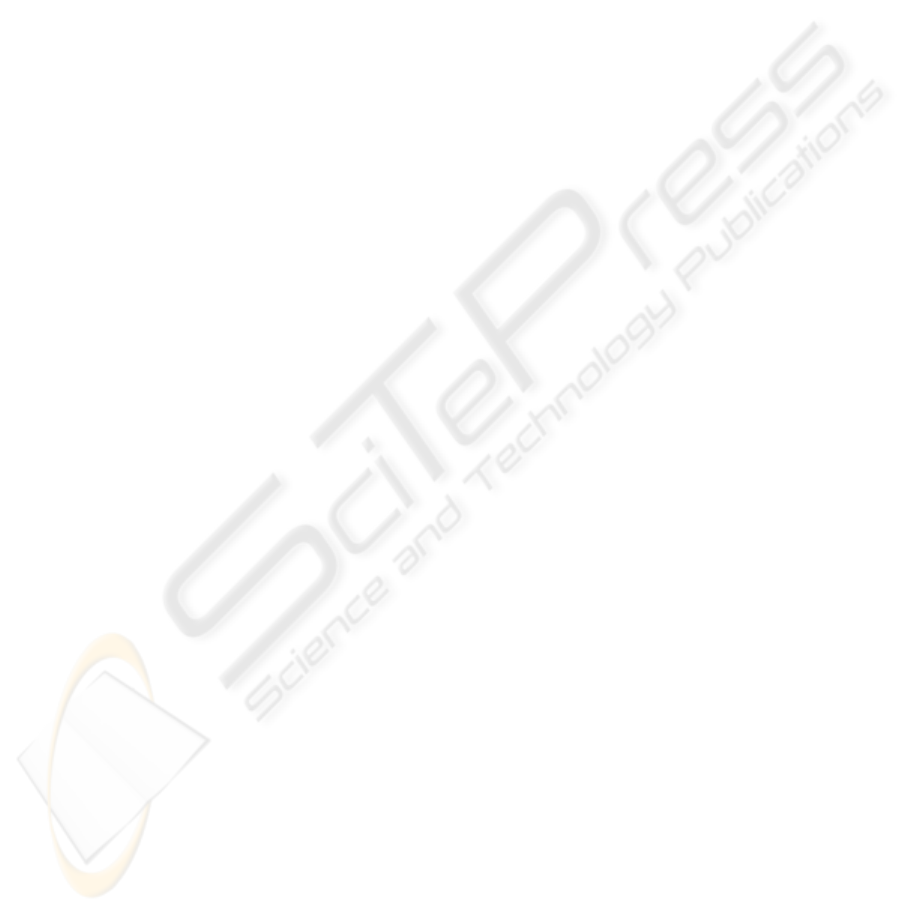
calculation of the operation starting and completion
due times of all respective operations. However,
changes in the operation processing times only
requires re-calculation of the operation starting and
completion due times of the succeeding operations.
A new job arrival requires definition of the
correspondent operation starting and completion
times and a regenerating mechanism to integrate all
operations on the respective single machine
problems. In the presence of a job cancellation, the
application of a regenerating mechanism eliminates
the job operations from the SMSP where they
appear. After the insertion or deletion of positions,
neighbourhood regeneration is done by updating the
size of the neighbourhood and ensuring a structure
identical to the existing one. Then the scheduling
module can apply the search process for better
solutions with the new modified solution.
4 CONCLUDING REMARKS
In most practical environments, scheduling is an
ongoing reactive process where the presence of real
time information continually forces reconsideration
and revision of pre-established schedules.
The handling of uncertainty is an important issue in
real-world scheduling problems. Uncertainty can
arise through incomplete knowledge of the problem,
through incomplete knowledge of how the problem
will change over time or may be inherent to the
problem itself.
This work is concerned with the resolution of
realistic Job-Shop Scheduling Problems (EJSSP).
Thus, not only it focuses on the solution of the
dynamic EJSSP problem but also on both the
deterministic and non-deterministic versions of it.
Moreover, it is concerned with integrated scheduling
of jobs which are products composed by several
parts or components which may be submitted to a
number of manufacturing and multi level assembly
operations, having as the main criterion meeting due
dates. We call these problems Extended EJSSP.
Considering that natural evolution is a process of
continuous adaptation, it seemed us appropriate to
consider Genetic Algorithms for tackling real Non-
Deterministic Scheduling Problems. Thus, the GA
based scheduling system developed adapts the
resolution of the static and deterministic problem to
the dynamic one in which changes may occur
continually. A population regenerating mechanism is
put forward, for adapting the population of solutions,
according to disturbances, to a new population,
which increases or decreases according to new job
arrivals or cancellations.
We recognize the need for further testing,
particularly for better evaluation of the suitability the
proposed framework and mechanisms under
dynamic Extended Job-Shop environments. We also
recognize that this is not an easy task because it is
difficult to find in the literature test problems with
the job structure that we selected and think
important, in industrial practice, namely jobs made
from several parts to be manufactured and
assembled through several assembly operations and
stages.
REFERENCES
Adams, Joseph, Balas, Egon and Zawack, Daniel, 1988,
The Shifting Bottleneck Procedure for Job Shop
Scheduling, Management Science, Vol. 34, nº 3, USA.
Baker, K.R., 1974, Introduction to sequencing and
scheduling, Wiley, New York.
Blazewicz, J., Ecker, K.H., Pesch, E., Smith, G. and
Weglarz, J., 2001, Scheduling Computer and
Manufacturing Processes, Springer, 2nd edition, New
York.
Dimopoulos, C. and Zalzala, Ali M. S., 2000, Recent
Developments in Evolutionary Computation for
Manufacturing Optimization: Problems, Solutions and
Comparisons, IEEE Trans. on Evol. Computation, nº4,
vol.2, 93-113.
French, S., 1982, Sequencing and Scheduling: An
introduction to the Mathematics of the Job Shop, Ellis
Horwood, Chichester.
Madureira, Ana M., Ramos, Carlos and Silva, Sílvio do
Carmo, (2001a), A Genetic Approach for Dynamic
Job-Shop Scheduling Problems, 4th MetaHeuristics
International Conference (MIC‘2001), Porto
(Portugal).
Madureira, Ana M., Ramos, Carlos and Silva, Sílvio do
Carmo, (2001b), A GA Based Scheduling System for
The Dynamic Single Machine Scheduling Problem,
ISATP‘2001 (IEEE International Symposium
Assembly and Task Planning), Fukuoka (Japão).
Madureira, Ana M., Ramos, Carlos and Silva, Sílvio do
Carmo, (2002), A Coordination Mechanism for Real
World Scheduling Problems Using Genetic
Algorithms, IEEE 2002 IEEE World Congress on
Computational Intelligence, Honolulu - Hawaii
(EUA).
Morton, E. Thomas and Pentico, David W., 1993,
Heuristic Scheduling Systems, John Wiley & Sons.
Portmann, M. C., 1997, Scheduling Methodology:
optimization and compu-search approaches, in The
planning and scheduling of production systems,
Chapman & Hall.
EVOLUTIONARY APPROACH FOR DYNAMIC SCHEDULING IN MANUFACTURING
291