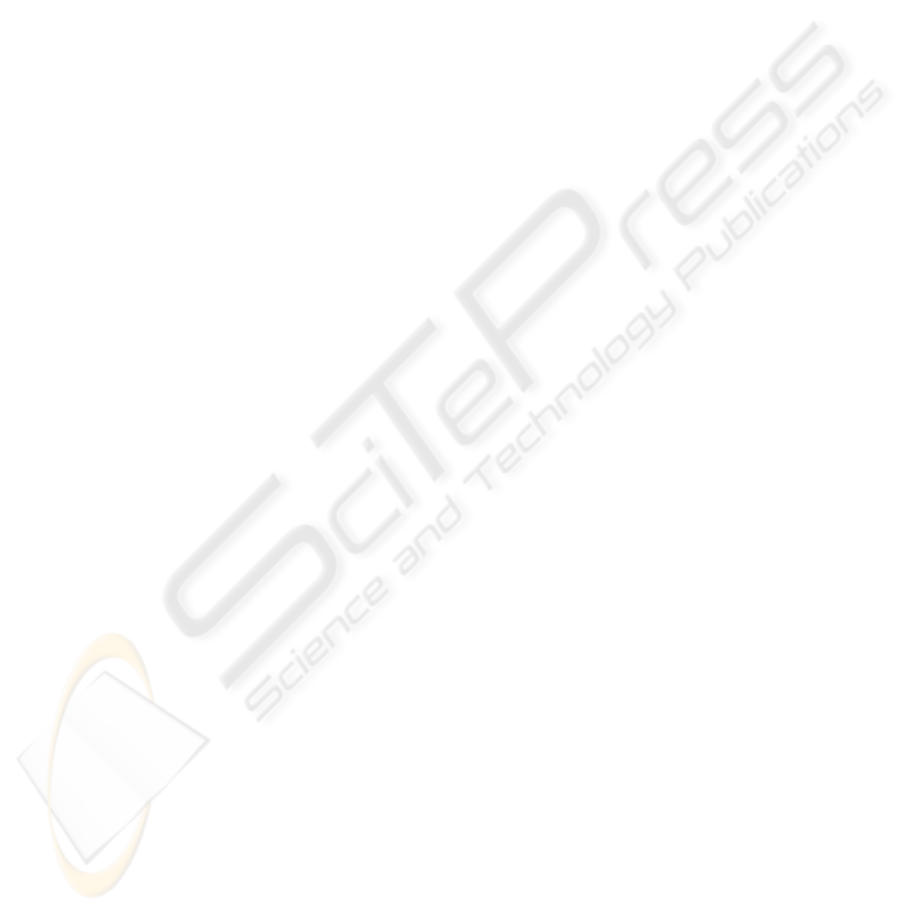
the wait for set-up of the workstation (B),
minimizing the wait in queue at the workstation (C),
and using a learning strategy (D). It can be noted
how the reactive policy (D), designed with the aid of
the DEVS model, outperforms the common (static)
decision rules using MAS.
Future research aims at applying the proposed
approach to other complex distributed control and
optimization problems, such as those involved in
large-scale logistic or supply chains.
6 CONCLUDING REMARKS
In this paper, we used the DEVS formalism to
specify the model of the main agents operating in a
MAS controlling part-driven heterarchical
manufacturing systems. In this context, we detailed
the interactions guiding the negotiations related to a
generic step in a working procedure associated with
a part process. The model respects heterarchical
principles and can be used in a simulation platform
which allows us to analyze both the classical
performance indices of a manufacturing system and
the effectiveness of the MAS, using decision
policies which implement adaptation strategies.
The proposed method leaves many interesting
issues open for further research. The next step
toward the experimentation of the multi-agent
control system on an automated manufacturing
plant, is to test the DEVS model on a distributed
network of computers, each hosting one or more of
the agents in the heterarchical network. This aims at
investigating and properly addressing the critical
issues related to distributed autonomous controllers
that cannot be examined when simulating the whole
set of agents on a centralized platform.
REFERENCES
Duffie, N.A., Prabhu, V.V., 1996. Heterarchical control of
highly distributed manufacturing systems.
International Journal of Computer Integrated
Manufacturing, Vol. 9, No. 4, pp. 270-281.
Han, W., Jafari, M.A., 2003. Component and Agent-Based
FMS Modeling and Controller Synthesis. IEEE Trans.
Sys., Man, and Cybernetics – Part C, Vol. 33, No. 2,
pp. 193-206.
Heragu, S.S., Graves, R.J., Kim, B.-I., Onge, A.St., 2002.
Intelligent Agent Based Framework for Manufacturing
Systems Control. IEEE Trans. Sys., Man, and Cyber. -
Part A, Vol. 32, No. 5.
Hsieh, F.-S., 2004. Model and control holonic
manufacturing systems based on fusion of contract
nets and Petri nets. Automatica, 40, pp. 51-57.
Huhns, M.N., Stephens, L.M., 2001. Automating supply
chains. IEEE Int. Comput., Vol. 5, No. 4, pp. 90-93.
Kotak, D., Wu, S., Fleetwood, M., Tamoto, H., 2003.
Agent-based holonic design and operations
environment for distributed manufacturing. Computers
in Industry, 52, pp. 95-108.
Lee, J.S., Hsu, P.L., 2004. Design and Implementation of
the SNMP Agents for Remote Monitoring and Control
via UML and Petri Nets. IEEE Trans. Control Sys.
Techn., Vol. 12, No. 2, pp.293-302.
Lin, F., Norrie, D.H., 2001. Schema-based conversation
modeling for agent-oriented manufacturing systems.
Computers in Industry, Vol. 46, pp. 259-274.
Logan, B., Theodoropoulos, G., 2001. The distributed
Simulation of Multiagent systems. Proceedings of the
IEEE, Vol. 89, No.2, pp. 174-185.
Maione, G., Naso, D., 2003a. A Genetic Approach for
Adaptive Multi-Agent Control in Heterachical
Manufacturing Systems. IEEE Trans. Sys., Man, and
Cyb. – Part A: Spec. Issue Collective Intelligence in
Multi-Agent Systems, Vol. 33, No. 5, pp. 573-588.
Maione, G., Naso, D., 2003b. A Discrete-Event System
Model for Multi-Agent Control of Automated
Manufacturing Systems. In IEEE SMC’03, Int. Conf.
on Sys., Man and Cyb., Washington D.C., USA.
Maione, G., Naso, D., 2003c. A Soft Computing Approach
for Task Contracting in Multi-Agent Manufacturing
Control. Comp. Ind., Vol. 52, No. 3, pp. 199-219.
Parunak, H.V.D., 1994. Applications of Distributed
Artificial Intelligence in Industry. In O’Hare,
Jennings, (Eds.), Foundations of Distributed Artificial
Intelligence, Wiley-Inter-Science.
Prabhu, V., Duffie, N., 1999. Nonlinear dynamics in
distributed arrival time control of heterarchical
manufacturing systems, IEEE Trans. Control Systems
Technology, Vol. 7, No. 6, pp. 724-730.
Shattenberg, B., Uhrmacher, A.M., 2001. Planning Agents
in James. Proc. of the IEEE, Vol. 89, No. 2, pp. 158-
173.
Shen, W., Norrie, D.H., 1999. Agent-Based Systems for
Intelligent Manufacturing: A State-of-the-Art Survey,
Knowledge and Information Systems, an International
Journal, Vol. 1, No. 2, pp. 129-156.
Smith, R.G., 1980. The Contract Net Protocol: High Level
Communication and Control in a Distributed Problem
Solver. IEEE Trans. Computers, Vol. 29, No. 12, pp.
1104-1113.
Sousa, P., Ramos, C., 1999. A distributed architecture and
negotiation protocol for scheduling in manufacturing
systems. Computers in Industry, Vol. 38, pp. 103-113.
Zeigler, B.P., Praehofer, H., Kim, T.G., 2000. Theory of
Modelling and Simulation, Academic Press, 2nd edit..
USING A DISCRETE-EVENT SYSTEM FORMALISM FOR THE MULTI-AGENT CONTROL OF
MANUFACTURING SYSTEMS
91