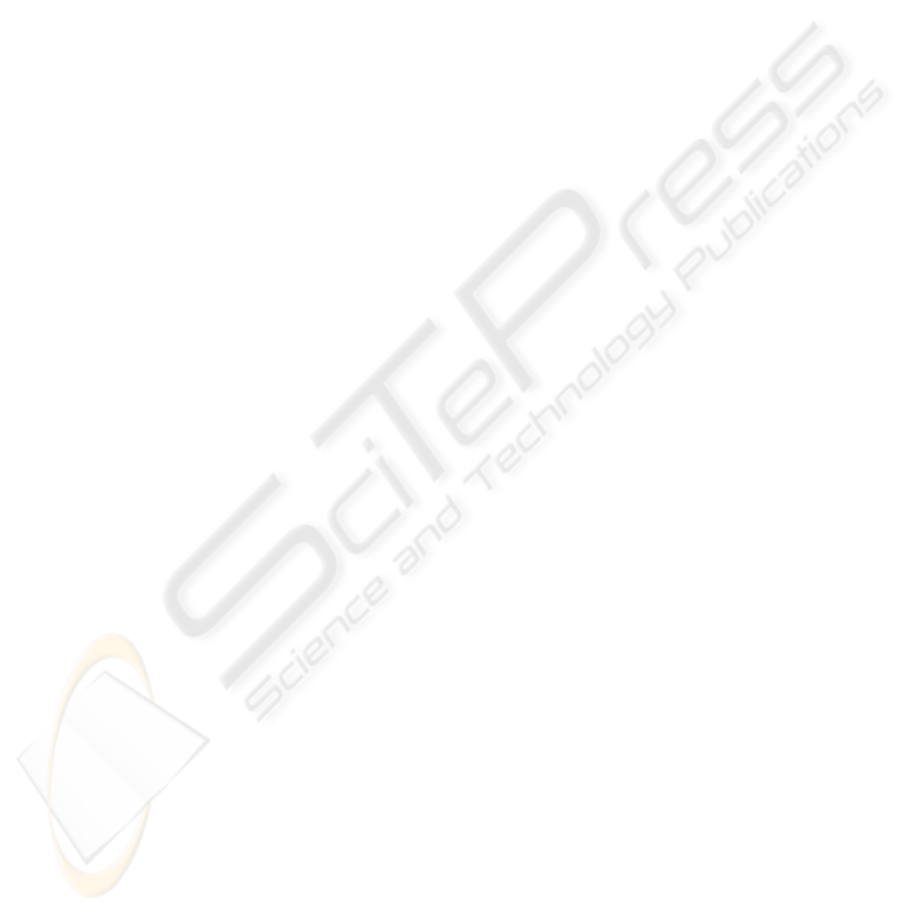
The simplest inspection is a visual examination
of the hull surface. Underwater however,
(particularly in harbors and at anchor in coastal
waters) a visual inspection must be performed very
close to the ship. The health of a ship’s skin may
also be judged by measuring plating thickness, or
checking for chemical evidence of corrosion. For
security purposes, a sonar image may be adequate
because of larger target size. For instance, the US
Customs Service currently uses a towfish sidescan
sonar to check hulls (Wilcox, 2003).
Some military vessels are now using small, free-
swimming ROVs for in-situ inspection (Harris &
Slate, 1999). This method eliminates the safety
hazard of diver work, but retains the disadvantage of
uncertain navigation and human load. The only
commercial hull inspection robot, at the time of this
writing, is the Imetrix Lamp Ray. Lamp Ray is a
small ROV designed to crawl over the hull surface.
The ROV is deployed from the vessel under
inspection; the vehicle swims in and closes with the
hull under human control, then holds itself in place
using front-mounted thrusters for suction. The
operator then drives the ROV over the hull surface
on wheels. This limits the survey to flat areas of the
hull; more complex geometry around e.g. sonar
domes, propeller shafts, etc. must still be visually
inspected with a free-swimming ROV. The Cetus II
AUV is an example of a free-swimming autonomous
system that has also conducted ship hull surveys
(Trimble & Belcher 2002). Using altimeters to
maintain a constant relative distance from the hull,
and the AquaMap long baseline navigation system
(DesertStar, Inc.), Cetus II records globally-
referenced position information, and this (with depth
and bearing to the hull) is the primary navigation
sensor used to ensure and assess full coverage. The
AquaMap system uses a transponder net deployed in
the vicinity of the ship being inspected (see URL in
References); clearly, a long baseline acoustic system
could be used for any vehicle.
Our vehicle program has three unique aspects to
address the needs of ship hull inspection:
development of a small autonomous vehicle
optimized for hovering, and of a hull-relative
navigation procedure, wherein dependence on a
deployed acoustic navigation system is avoided.
The data product this vehicle will produce is a high-
resolution sonar mosaic of a ship hull, using the
DIDSON imaging sonar (University of
Washington’s Applied Physics Laboratory) as a
nominal payload (Belcher et al., 2003).
2 PHYSICAL VEHICLE
OVERVIEW
The hovering AUV (HAUV, Figure 1) has eight
hubless, bi-directional DC brushless thrusters, one
main electronics housing, and one payload module.
The symmetrical placement of the large number of
thrusters makes the vehicle agile in responding to
wave disturbances, and capable of precise flight
maneuvers, such as orbiting targets for inspection or
hovering steadily in place. The vehicle is intended
to operate in water depths ranging from the Surf
Zone (SZ) through Very Shallow Water (VSW) and
beyond, up to depths of 100 meters; and to perform
in waves up to Sea State Three.
Onboard non-payload instruments include a
Doppler velocity log (DVL), inertial measurement
unit (IMU), depth sensor, and acoustic modem for
supervisory control. While we do carry a magnetic
compass, this cannot be expected to work well in
close proximity to a metal hull. As noted above, the
nominal payload at this writing is the DIDSON
imaging sonar. Both the DIDSON and the DVL are
mounted on independent pitching servos at the front
of the vehicle, because the DIDSON produces good
imagery at an incidence angle greater than 45
degrees, while the DVL needs to maintain a normal
orientation to the hull. The DVL can also be pointed
down for a bottom-locked velocity measurement.
The vehicle is strongly passively stable, with a
gravity-buoyancy separation of about 3cm. It has
approximate dimensions of 100cm long, 80cm wide,
and 30cm tall; it displaces about 45kg. Of this
weight, about 12kg are for a 1.5kWh battery.
3 OUR APPROACH TO HULL
NAVIGATION
We have chosen to attack this problem from a
feature-relative navigation standpoint, as this has
some advantages compared to current approaches.
Our basic strategy is to measure tangential velocity
relative to the hull being inspected using a Doppler
velocity log (DVL), and to servo a desired distance
from the hull, and orientation, using the individual
ranges from acoustic beams.
The immediate impact of this functionality is the
elimination of support gear for the robot itself; no
localized network setup like LBL is needed. This
reduces complexity and provides a simple, quick
deployment where the robot can operate unattended;
our long-term goal is that the mission focus could
shift towards analyzing the data collected. The lack
of a shipboard system presence also means the craft
ICINCO 2004 - ROBOTICS AND AUTOMATION
128