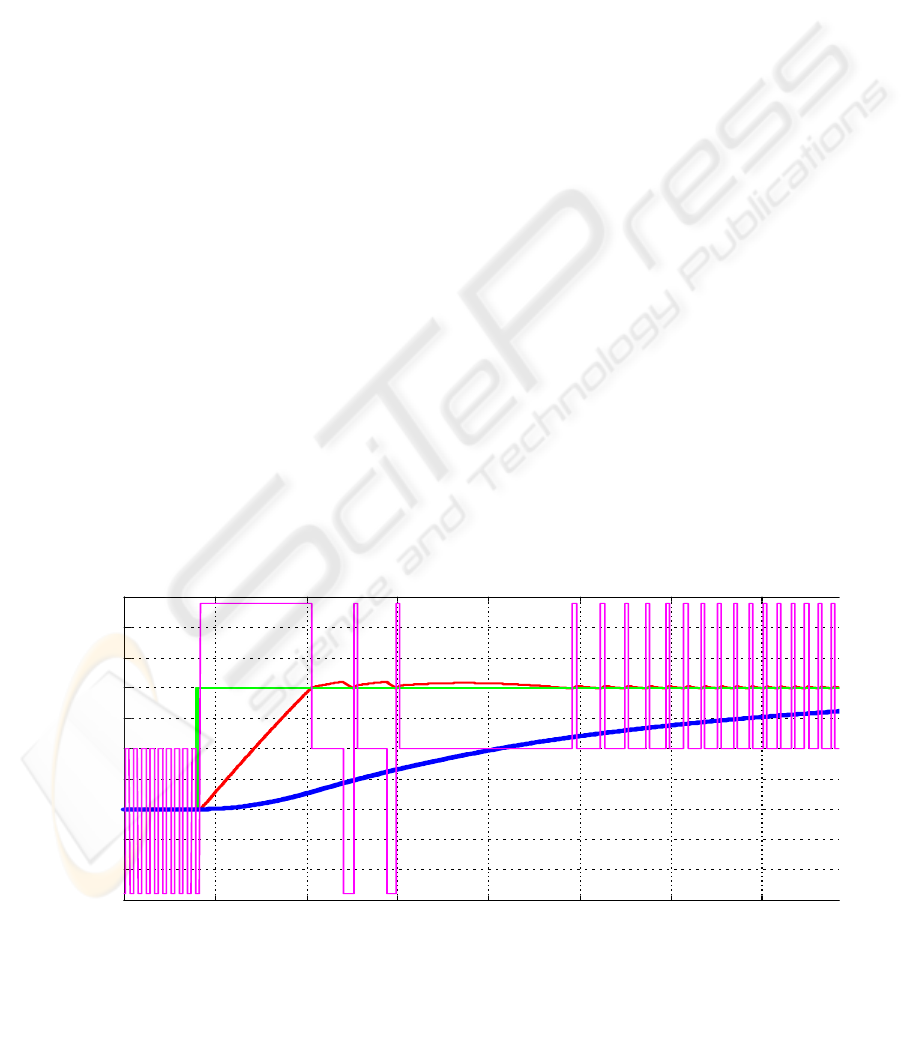
0
0.005
0.01
0.015
0.02
0.025
0.03
0.035
-25
-20
-15
-10
-5
0
5
10
15
20
25
Figure 7: The rapidly switching line represents the motor drive voltage in response to the step reversal in
current demand, the sloping line from -10A to +10A is the motor current, and the wide line from -10 to
+10rads/s is the motor speed.
that the current is fully controlled and that not much
extra bipolar switching is required. The advantages
and disadvantages of the 3 switching modes are
listed in table 1.
The hardware used did not switch both sides at
the same time so the negative voltage step changes
were limited to V
supply
at any one time rather than
2V
supply
for the bipolar drive. Software control can
apply this to all bipolar drives and reduce
electromagnetic interference from the drive.
The application of this hybrid switching
technique to the hand precluded fast measurements
of the motor current which changed very rapidly in
the small motors that have low values of motor
inductance L and relatively high resistance R. Such
rapid current changes would require specialized
hardware to track and control the current as was
done by Dunlop and Cree. It would also need to
operate an order of magnitude faster than for the
larger motors tested with the hardware.
In order to reduce the hardware and heating
requirements in the walker and hand, a model of the
DC motor was used to calculate the motor voltage
required for a given speed state and for the
maximum torque available to change that speed. The
maximum allowable current through the motor is
used to achieve the speed change and that value
must not be exceeded or excessive heating can
destroy the motor. Software is then used to switch
from unipolar driving to bipolar operation as the
motor starts regenerating i.e. operating within
diagonal hatched area in quadrants 2 and 4 in
fig.5(a). As shown in fig.4, the output of the PWM is
applied to FETs 1 and 3, while FETs 2 and 4 can be
driven high or low to set the current direction for a
unipolar drive depending on whether the signal is
connected to logic 1 or 0 by software inside the
CY8C6643 PSoC processor (programmable system
on a chip c.f. Cypress Microsystems). When a
bipolar drive is needed, the PWM is inverted and
applied to FETs 2 and 4. Revision to a unipolar drive
is simply a matter of by passing the inverted PWM
signal and setting the processor output to 0 or 1 for
FETs 2 and 4.
4 MODEL CONTROL
It is desirable to avoid using extra hardware for the
direct measurement of the current in the motors.
This lead to the development of model control for
the 11 DC motors in the dexterous hand. A Simulink
model of the DC motor used in the hand (a
Minimotor 1016 012G) is shown in fig.8. The
leadscrew driven linkages in the finger have a slight
effect on the motor and gearbox, and almost none
during regenerative braking as plain lead screws are
not easily back drive. The main effect is the motor
and gearbox inertia. The basic DC model includes
the thermal power output by the armature resistance,
and the effect of brush and bearing friction. This
friction is overcome by the specified “no load”
current but, as seen from equation 5, the no load
current is zero. In fact the friction must be overcome
and the “no load” current is required to do this. The
friction is modeled as Coulomb friction which
opposes the motion and decreases the torque
INTELLIGENT ELECTRIC DRIVE SYSTEM - A mechatronics approach
45