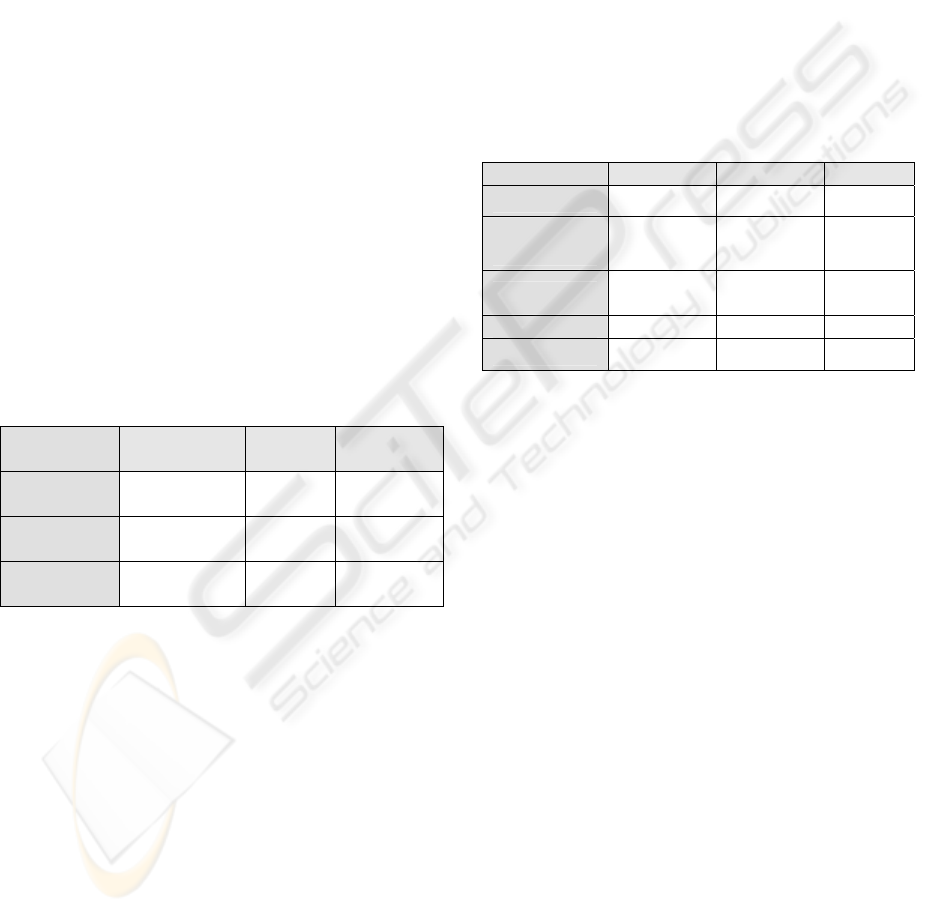
Instrument Automation and System Association
formed a committee of system vendors to develop
S95: Enterprise-Control System Integration
Standard (S952000). This standard provides means
to represent how ERP and MES are structured
inside the Enterprise Architecture.
This paper analyzes how different types of
manufacturing processes are supported by MES and
ERP systems. To better illustrate these ideas a
system framework is proposed in accordance with
the S95 hierarchy function model for a paper mill
enterprise.
2 MANUFACTURING PROCESSES
As business processes are the activities performed
within the business during which the state of
resources changes and which describe how work is
done, it is possible to define manufacturing
processes as business processes that transform
physical resources. ANSI/ISA classifies
manufacturing processes as discrete, continuous and
batch. This allows classifying manufacturing
processes according to resource type and their
relationship with time, as present on
Table 1
Table 1: Manufacturing types
Manufacturing
Process
Time
Characteristic
Type of
Input
Type of
Output
Discrete Discrete Time
Finite
Discrete
Finite
Discrete
Process
Continuous
Continuous
Time
Flow Flow
Process Batch
Interval of
Time
Finite not
discrete
Finite not
discrete
Discrete Manufacturing Processes are of two
types: Assembling: Several items are aggregated to
build one finished product (i.e. Auto Industry) and
Disassembling: Product is split in several sub-
products (i.e. Paper sheet production).
Manufacturing Batch Processes are based on a
recipe that is executed during a finite period of time,
consuming and producing finite quantities of
products, called lots (i.e. Pharmaceuticals Industry).
Continuous Manufacturing Processes
transform continuous input resources into
continuous output resources (i.e. Steel and Pulp
Industries).
There are industrial cases where the production
chain process is based on the aggregation of several
types of manufacturing processes. Production can be
composed by a continuous process followed by a
disassembling discrete process for cutting and an
assembling discrete process for packing, as in the
paper industry (Schroder1993).
3 MES AND ERP SYSTEMS
Systems to support quality and production planning
have to handle the different characteristics of each
manufacturing type described. The differences on
Manufacturing Processes that have influences in the
definition of applications are resumed on table 1.
Product identification is based on item number
for Discrete Process, lot number for Batch Process
and based on time interval or time instant on
Continuous.
Table 2: System features / manufacturing types
Discrete Continuous Batch
Identification Item Time Lot
Production
Planning entity
Bill of
Material
Rate Recipe Recipe
Quantities
Numbers of
items
Recipe Ratio
Based
Volume
or Weight
Quality Item based Time based Lot based
Trace Item based Flow based Lot based
The identification type influences quality
management, planning process and traceability
implementations, as all these processes have to
manipulate the product entity.
3.1 Overlapping features
The identification of the overlapping features
between MES and ERP systems is presented in
Table 3 where business activities are defined
according to the value chain model (Porter1985).
Inbound Logistics include activities of
planning, receiving and storing raw material,which
are usually supported by ERP systems.
Manufacturing aggregates activities of planning
and execution. It is the core capability of MES.
Quality control activity is usually well
supported by MES systems. ERP systems’ planning
is usually based on Bill Material or Recipe entities
that do not cover all Industries Operations
requirements.
Outbound Logistics as Inbound Logistics are
well supported by MES and ERP systems on storage
management, planning and execution of delivery
activities.
Sales are composed by the activities of order
fulfilment, planning and invoicing which are
supported by both systems. When the order deliver
INFORMATION SYSTEMS SUPPORT FOR MANUFACTURING PROCESSES - THE STANDARD S95
PERSPECTIVE
553