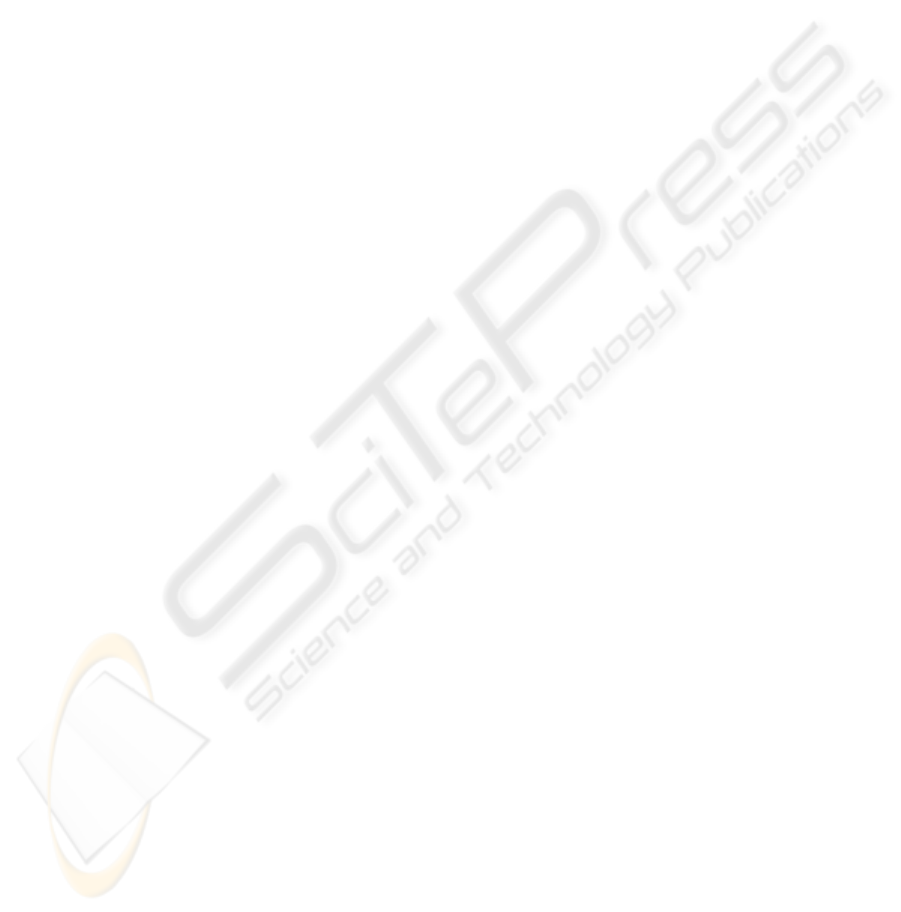
performance and in terms of quality of planning
schedule generated. Also, the company will be able
to analyze the impact of rescheduling the
manufacturing planning and to predict the
production orders finish date and even detects
possible bottlenecks.
In order to model the information system under
development, an object-oriented approach was
followed, namely the UML - Unified Modelling
Language (Booch et al., 1999).
This paper is structured as follows. The
following section describes the company, presents
their manufacturing process, and concludes with
some issues concerning production planning and
control. An overview of the main requirements for
the decision support system under development is
presented in section three. Finally, we will
summarise our results and make a brief reference to
some topics for future work.
2 THE CASE STUDY
3.4
Company Description
The company to which reference is made throughout
this paper produces special test equipment tables for
automobile test components manufacturers, namely
cable testing tables. For each variant of automobile
cable, the company, at most, produces three testing
tables and they are always product specific. This
means that the same testing table cannot be used for
different automobile cable models.
The most important organisational aspect of the
company is their manufacturing production model to
be Make-to-Order oriented. The company plans the
production taking into account firm customer’s
orders and available capacity. Even though they
have a product portfolio, every potential customer
order, due the particular technical specification, is
nearly always a new product, and their
manufacturing cycle time is usually very tight,
normally between two or three weeks.
3.5 Manufacturing Process
The company considered here is a make-to-order
firm, with a discrete production model, which
manufactures and delivers complex products. The
total operations for realizing an order consists of
partly overlapping phases: design and engineering,
procurement, component production, pre-assembly
of subsystems, final assembly and testing. Within
the manufacturing plant, the resources are organised
as a functional layout, exploring at cell level, group
technology. This layout organisation was prepared
for ‘one-of-a-kind’ production and can be
conceptualized and managed as job-shop
manufacturing environment. In these areas are
manufactured all components and assembled the
final product, according order specification. In
Figure 1 is represented one of the core company’s
processes: the production business process with its
sub-process.
3.6 Production planning and
control issues
Production planning is an important task within a
manufacturing system. We define the planning
system as that part of the manufacturing system that
is responsible for regulating, coordinating, and
monitoring the flow of work through the production
system. The way the planning system accomplishes
its function strongly influences the performance of
the production system. Presently the company
performs the production planning based on the
delivery date of each order. When arrive a customer
order, it goes to an orders queue. The orders with
short delivery time are the first to be manufactured,
what means that the orders are orderly by priorities
Top priorities are given to express deliveries and
normal priorities are given to orders with large
delivery margin, being their priority raised as due
date became closer. In the beginning of every week
the production department analyzes the delivery date
for each order and with that, the current production
status, the tables lifetime and the better management
practice the week planning schedule is done.
This brings two problems for the company, the
major is that the capacity needs in different phases
of production changes abruptly as the needs for
anticipate deliveries or to satisfy orders that are
crucial in company strategy. The effect is that
modules progress through production quite
randomly and the lead times became longer what
results in a high level of WIP (Work-in-Progress).
The second problem is a consequence of the
first, i.e. if the manufacturing isn’t executed as initial
planned, the manufacture planning becames
unreliable, making almost impossible assess the
impact of new orders acceptance.
Ideally, the planning and control method should
level the need for capacity in a way that allows for
prediction completion for each order and
simultaneously results in adequate capacity
utilization.
ICEIS 2004 - ARTIFICIAL INTELLIGENCE AND DECISION SUPPORT SYSTEMS
418