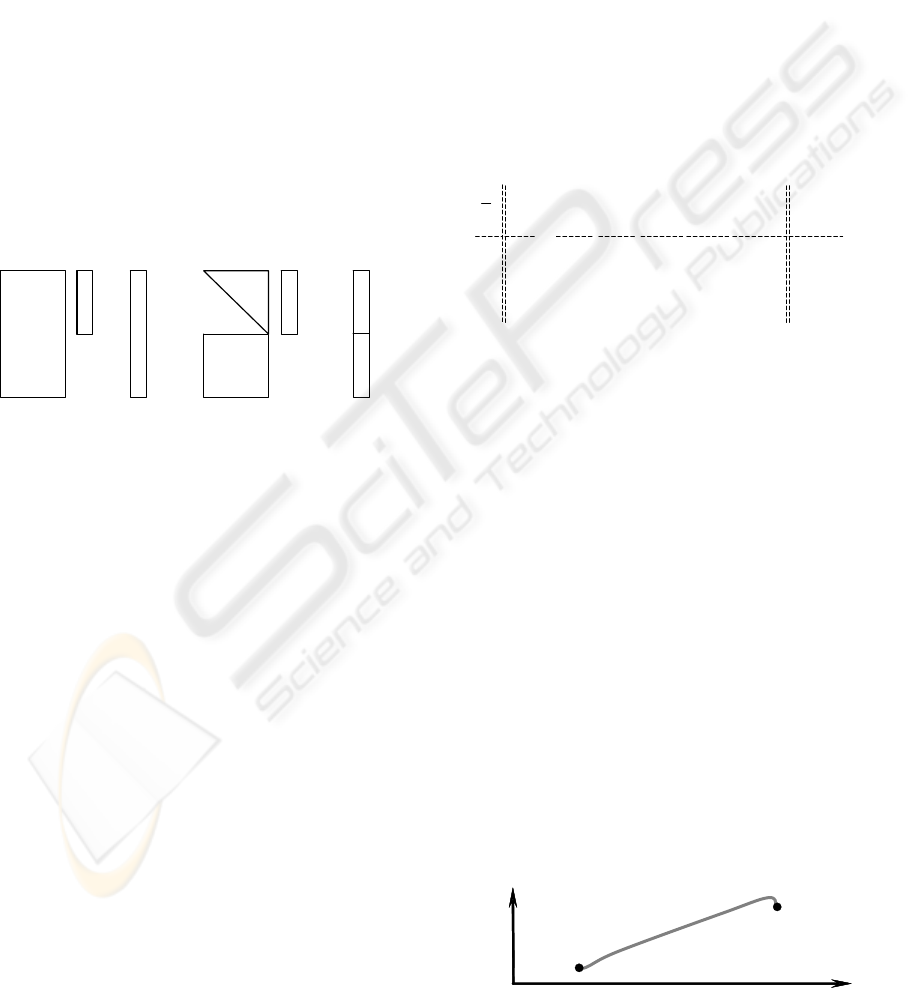
The objective is to search for such u, which
minimizes the square root (26) i.e. the control u
minimizes the norm |J| of the criterion. In case of
square root (26), the minimization leads to a system
of algebraic equations with more rows than
columns – over-determined system:
0
0
fwQ
u
Q
GQ
y
u
y
=
⎥
⎦
⎤
⎢
⎣
⎡
−
−
⎥
⎦
⎤
⎢
⎣
⎡
)(
0buA =−
(27)
For optimization of the criterion, the orthogonal
triangular decomposition (Golub and Van, 1989;
Lawson and Hanson, 1974) is used. It reduces
excess rows of matrix A [(2·N·i)×(N·i)] and elements
of vector b [2·N·i] (i is a number of DOF) into upper
triangular matrix R and a vector c according
to the following scheme:
T
TT
Q
b
b
Qu
u
A
A
Q
/
=
=
cuR =
(28)
⇒
=
A u
b
=
R
1
0
u c
c
z
1
(29)
Vector c
z
is a lost vector, whose Euclidean norm
|c
z
| is equal value of square root √J (i.e. J = c
z
T
c
z
).
To obtain unknown control actions u, only upper
part of the system (29) is need
11
1
1
)( cR
c
u
uR
T
=
=
(30)
Since a matrix R
1
is upper triangle, then the con-
trol u is given directly by back-run procedure.
The penalizations Qu and Qy (usually selected
as
Qy
=
diag(λ
y
),
λ
y
=1
and
Qu
=
diag(λ
u
), 〉〈∈ 1,0
u
λ
)
determines magnitude of the redistributed loss
in considered horizon of the prediction N.
The horizons Nu and No have not direct
utilization here. Control horizon Nu is usually equal
horizon of prediction N; lower values provide
equality of control actions at the end of optimization
horizon – useless for robot motion. Initial insen-
sitivity horizon No is also directly useless. It causes,
that control differences at the beginning of the hori-
zon N are not considered.
The different choice of ratio of penalization λ
u
/λ
y
together with horizon N enables to generate control
actions that the available drives were not fitfully
exerted. However, distributed changes of torques
are achieved with the cost of certain loss (error),
that theoretically equals value of the criterion.
3.3 Quadraticaly-Optimal Trajectories
As one interesting possibility, the predictive control
offers, due to its several horizons (N, No, Nu), planning
trajectories by record of outputs from simulation.
The task is defined as follows: let us have two points
– start and end, and at the same time, a path
(trajectory) is not conditioned, only end-point must
be achieved (Figure 2). In such case, we can use
predictive control with specific setting of the output
horizons N and No. If we set, that the horizon
maxNN
and kNNo
, where k is order of the
controlled system, then the quadratic criterion will
consider only last k differences among predicted
end-point and its reference value. Thus, the matrix G
and corresponding differences (w - f) in the criterion
(27), are reduced only on their last k rows and
elements respectively
⎥
⎥
⎥
⎥
⎥
⎥
⎥
⎥
⎥
⎥
⎥
⎦
⎤
⎢
⎢
⎢
⎢
⎢
⎢
⎢
⎢
⎢
⎢
⎢
⎣
⎡
−
−
=
⎥
⎥
⎥
⎥
⎥
⎥
⎥
⎥
⎥
⎥
⎥
⎦
⎤
⎢
⎢
⎢
⎢
⎢
⎢
⎢
⎢
⎢
⎢
⎢
⎣
⎡
−
⋅
⋅
−
−−
−
0
0
fw
fw
1
0
CB
0
.
CAB
.
.
.
1
CB
.
BCA
0
1
BCA
BCA
0
0
fw
10
1
01
G
#
#
#
#
"
"
"
"
"
"
"
#
#
#
N
kN
NN
kN
)(
)(
21
(31)
Lower unit matrix in (31) corresponds to dimen-
sion of input penalization. Such form, specifically
last k rows of matrix G and corresponding
differences (w – f), causes quadratic distribution
of energy to individual inputs (control actions)
within whole horizon Nmax.
If indicated procedure would be applied, then the
control process has no information, in which step
should stop. Difference of horizons N and No is still
the same. Information on stopping the control
process is given by horizon No.
Described sequence represents specific dead-
bead control spread within time. Thus, it is not
necessary to achieve end point during minimal
number of steps (= order of system) in control
process, but on the other hand (from reasons of
feasibility by drives) it is better to distribute the
input energy uniformly without rapid turns in some
wider horizon. Its length should arise from
technological requirements.
The sequence can be used only once under
condition, that the system is linear and horizon No is
a little bit lower than horizon N; i.e. value No gives
the length of horizon, on which the system should
stop after previous
)( No-maxN steps.
Figure 2: One example of planned trajectory
end
star
PREDICTIVE CONTROL FOR MODERN INDUSTRIAL ROBOTS - Algorithms and their applications
7