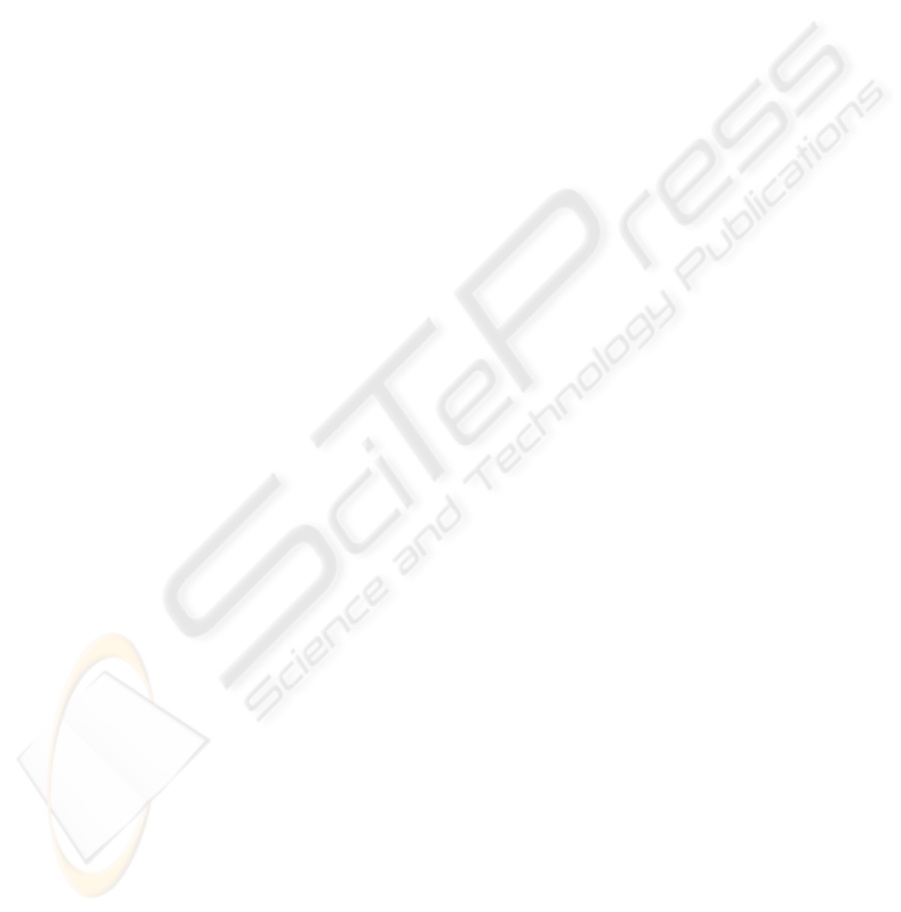
REFERENCES
Armaou, A., Christofides, P. (2002). Dynamic
optimization of dissipative PDE systems using
nonlinear order reduction.
Chem. Eng. Sc., 57, 5083-
5114.
Baker, J., Christofides, P. (1999). Output feedback control
of parabolic PDE systems with nonlinear spatial
differential operators.
Ind. Eng. Chem. Res., 38, 4372-
4380.
Chatterjee, A. (2000). An introduction to the proper
orthogonal decomposition.
Current Science, 78, 808-
817.
Chiu, T., Christofides, P. (1999). Nonlinear control of
particulate processes.
AIChE Journal, 45, 1279-1297.
Christofides, P. (1998). Robust control of parabolic PDE
systems.
Chem. Eng. Sc., 53, 2949-2965.
Christofides, P. (2001a). Control of nonlinear distributed
process systems: recent developments and challenges.
AIChE Journal, 47, 514-518.
Christofides, P. (2001b).
Nonlinear and Robust Control of
PDE Systems: Methods and Applications to transport
reaction processes.
Birkhäuser, Boston.
Christofides, P. J. Baker, (1999). Robust output feedback
control of quasi-linear parabolic PDE systems. In
Systems & Control Letters, 36, 307-316.
Christofides, P., Daoutidis, P. (1996). Nonlinear control of
Diffusion-Convection-Reaction processes.
Comp.
Chem. Eng.,
20, 1071-1076.
Christofides, P., Daoutidis, P. (1997). Finite-Dimensional
Control of Parabolic PDE Systems Using
Approximate Inertial Manifolds.
Journal of
mathematical analysis and applications,
216, 398-420.
El-Farra, N., Armaou, A., Christofides, P. (2003).
Analysis and control of parabolic PDE systems with
input constraints.
Automatica, 19, 715-725.
El-Farra, N., Christofides, P. (2004). Coordinating
feedback and switching for control of spatially
distributed process. Comp. Chem. Eng.,28, 111-128.
Gay, D., Ray, W. (1995). Identification and control of
distributed parameter systems by means of the singular
value decomposition.
Chem. Eng. Sc., 50, 1519-1539.
Gonzáles-García, R., Rico-Martínez, R., Kevrekidis, I.
(1998). Identification of distributed parameter
systems: A neural net based approach.
Comp. Chem.
Eng.,
22, 965-968.
Hoo, K., Zheng, D. (2001). Low order control-relevant
models for a class of distributed parameter systems.
Chem. Eng. Sc., 56, 6683-6710.
Newman, A. (1996a). Model reduction via the Karhunen-
Loève Expansion Part I: An exposition.
Technical
Report 96-32,
University of Maryland, College Park,
MD.
Newman, A. (1996b). Model reduction via the Karhunen-
Loève Expansion Part II: Some elementary examples.
Technical Report 96-33, University of Maryland,
College Park, MD.
Padhi, R., Balakrishnan, S. (2003). Proper orthogonal
decomposition based optimal neurocontrol synthesis
of a chemical reactor process using approximate
dynamic programming.
Neural Networks, 16, 719-728.
Padhi, R., Balakrishnan, S., Randolph, T. (2001).
Adaptive-critic based optimal neuro control synthesis
for distributed parameter systems.
Automatica, 37,
1223-1234.
Park, H., Cho, D. (1996a). The use of Karhunen-Loeve
decomposition for the modelling of distributed
parameter systems.
Chem. Eng. Sc., 51, 81-89.
Park, H., Cho, D. (1996b). Low dimensional modelling of
flow reactors.
Int. J. Heat Mass Transfer, 39, 3311-
3323.
Park, H., Kim, O. (2000). A reduction method for the
boundary control of the heat conduction equation.
Journal of Dynamic Systems Measurement and
Control
, 122, 435-444.
Sarimveis, H., Alexandridis, A., Tsekouras, G., Bafas, G.
(2002). A fast and efficient algorithm for training
radial basis function neural networks based on a fuzzy
partition of the input space.
Ind. Eng. Chem. Res., 41,
751-759.
Shvartsman, S., Kevrekidis, I. (1998). Nonlinear model
reduction for control of distributed systems: a
computer –assisted study.
AIChE Journal, 44, 1579-
1595
Shvartsman, S., Theodoropoulos, C., Rico-Martínez, R.
Kevrekidis, I., Titi, E., Mountziaris, T. (2000). Order
reduction for nonlinear dynamic models of distributed
reacting systems.
Journal of Process Control, 10, 177-
184.
Zheng D., Hoo, K. (2002). Low-order model identification
for implementable control solutions of distributed
parameter systems.
Comp. Chem. Eng., 26, 1049-
1076.
Zheng, D., Hoo, K. (2004). System identification and
model-based control for distributed parameter
systems.
Comp. Chem. Eng., 28, 1361-1375.
Zheng, D., Hoo, K., Piovoso, M. (2002a). Low-order
model identification of distributed parameter systems
by a combination of singular value decomposition and
the Karhunen-Loève expansion.
Ind. Eng. Chem. Res.,
41, 1545-1556.
Zheng, D., Hoo, K., Piovoso, M. (2002b). Finite
dimensional modeling and control of distributed
parameter systems. In
2002 American Automatic
Control Conference,
A.A.C.C.
ICINCO 2005 - INTELLIGENT CONTROL SYSTEMS AND OPTIMIZATION
24