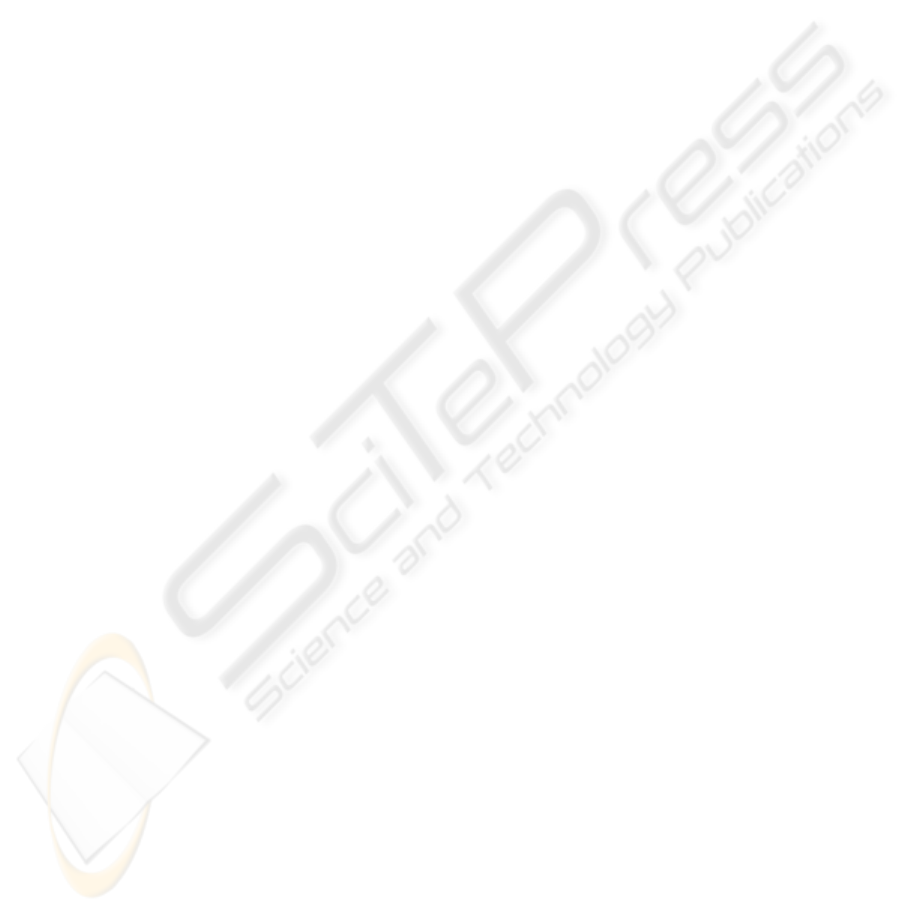
3.2 Comparison
The spectral analysis of the estimated
electromagnetic torque computed by different
methods clearly shows that when a rotor fault is
present a component appears at the fault’s
characteristic frequency « f
0
=2sf» and his amplitude
is directly linked to the severity of the fault. In order
to elaborate motor mechanical diagnosis, a criterion
“R” is used to represent the severity of the
mechanical fault see Figure 4.
M
s
PR −=
in dB (22)
“P
s
” is the amplitude of the fault characteristic
frequency. “M” is the spectrum average, for a fault-
free motor, in the range where the fault characteristic
frequency may occur. In our case the range is [0.3
Hz, 5 Hz], corresponding to the fault characteristic
frequency at no load and at 120% of the motor
nominal load. Figure 5 and Figure 6 show a
comparison between all the three diagnosis methods
with respect to the comparison criterion “R”, at three
load levels in case of one Figure 5 and two broken
bars Figure 6. Experimental results clearly show that
the EKF and ELO methods are better able than the
SMO observer to detect broken bars at all load
levels. EKF and ELO detection methods were
comparable as regards their capacity to detect
mechanical faults, although EKF displayed a much
higher comparison criterion at low load levels.
4 CONCLUSION
This paper has treated a new detection approach
using a sliding mode observer and compared three
non-invasive approaches for the detection of rotor
imperfections. In a first approach, the sliding mode
observer (SMO) is used to estimate stator flux
components in the absence of any speed sensing or
speed estimation. The second approach uses an
extended Kalman filter (EKF) and the third approach
uses an extended Luenberger observer for flux
components and velocity estimation. Experimental
results using real electrical signals (assuming no
change in motor parameters) show the importance of
using the Kalman filter to estimate the
electromagnetic torque, which can provide more
effective detection of rotor faults even at low load
levels. We are currently concentrating on the
sensitivity of these two approaches to natural
variations in electrical parameters, which can
sometimes give rise to false alarms.
REFERENCES
Cardoso, A.J.M., 1993. Computer-Aided Detection of
Airgap eccentricity in operating three phase
induction’s Motors by park vector Approach. In IEEE
Transactions on Industry Applications, vol. 29 N° 5,
pp. 897–901.
Cruz, S.M.A et al., 2000. Rotor cage Fault Diagnosis in
three-phase induction Motors by Extended Park’s
Vector Approach. In Electric Machines and Power
Systems, vol. 28, pp.289-299.
El tabach, M., 2002. Detection of induction motors broken
bars by electromagnetic torque estimation using
Kalman filtering. In EPE-PEMC, 10th International
Power Electronics and Motion Control conference,
Dubrovnik, Croatia.
Janson, 1992. A physically insightful approach to the
design and accuracy assessment of flux observers for
field oriented induction machine drives. In IEEE – IAS
Annual meeting record, pp. 570-577.
Kheloui, A., 2000. Design of a stator flux sliding mode
observer for direct Torque control of Sensorless
induction machine. In IEEE Industry Application
Conference, vol. 3, pp.1388-1393
Kliman, G.B., 1992. Methods of motor current signature
Analysis. In Electric Machines and Power Systems.
Vol. 20 N° 5 , pp. 463-474.
Kral, Ch., et al., 2000. Sequences of field-oriented Control
for the detection of faulty rotor Bars in induction
Machines, the Vienna monitoring method. In IEEE
Transactions on Industrial Electronics, vol. 47 N° 5,
pp. 1042-1050.
Stanislaw, F. et al., 1996. Instantaneous Power as a
medium for the signature analysis of induction
Motors. In IEEE Transactions on Industry
Applications, vol 32 N° 4, pp. 904-909.
Trzynadlowski, A.M et al., 2000. Comparative
Investigation of Diagnostic Media for Induction
Motors: a case of rotor cage faults. In IEEE
Transactions on Industrial Electronics, vol. 47, pp.
1092 –1099.
BROKEN BAR DETECTION IN INDUCTION MOTORS - Using non intrusive torque estimation techniques
149