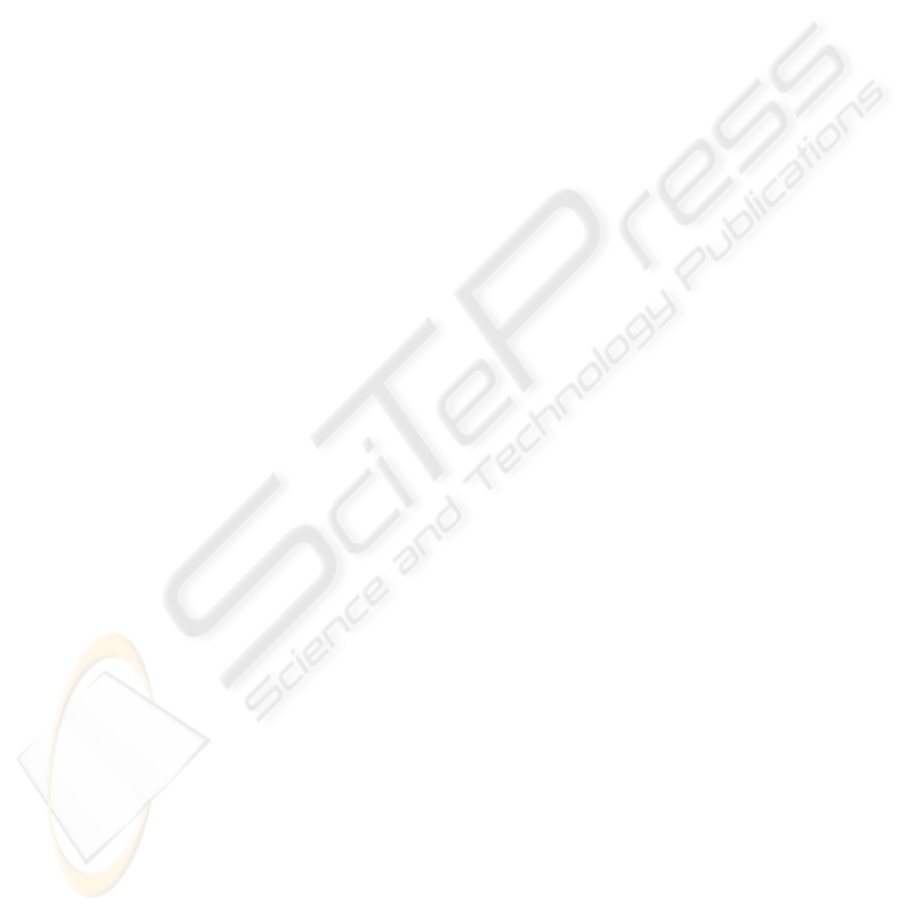
the pilot and rail pressures oscillating behavior
within the 100 ms control period: the pressure
increases when the solenoid valve is opened, while
decreases when it is closed. Further simulations may
show that shortening the control period attenuates
these pressure variations.
Fig. 4 depicts model output for constant 40 bar
tank pressure and 9% d.c. and a varying injectors
driving signal. Simulation starts from a steady state
condition corresponding to a 2200 engine speed and
3 ms injectors exciting time interval within the
injection cycle. At time 4.5 s we have applied a 4000
rpm speed step, and raised the injection time interval
to 12 ms, so that the applied d.c. is no longer able to
maintain the initial rail pressure, because of the more
injected fuel amount. Besides, the fuel flow between
main and pilot circuit causes the pilot circuit
pressure to decrease. At time 21 s we have applied a
complete cut-off, i.e. we have kept the injectors
closed in the whole injection cycle: pilot and rail
pressures rise because the fuel is no more sent to the
intake manifolds. In conclusion, we observe that the
accordance of the resulting dynamics with the
expected behavior shows the model validity.
A second set of tests investigates the GPC
performances. To this end, we consider a 100% set-
point variation, to evaluate the rail pressure
response. We have tuned all the tested controllers
referring to models linearized at the starting
equilibrium point. Figures 5 and 6 show the rail
pressure dynamics when the system is controlled by
a GPC with N = 5 (0.5s) and N = 15 (1.5s) prediction
horizons respectively, and a N
U
= 1 (0.1s) control
horizon for both cases. We have also compared the
linear and nonlinear model responses with the above
controllers. Clearly, increasing prediction horizon
results in a sluggish response, while considerably
decreases pressure overshoot, which is strongly
desirable. Further simulations may show that
increasing the control horizon does not result in a
better rail pressure behavior.
Figures 7 and 8 compare the GPC with a
standard PI controller, tuned according the Ziegler-
Nichols rules. To evaluate the controllers robustness
to model uncertainties, we have tuned them by
considering a 3 bar rail working pressure (Figure 7).
Then we have assumed a different operating
condition (Figure 8), holding the same parameters.
We have considered the linear system response for
the GPC, since it almost coincides with the nonlinear
one. Compared with the PI controller, the proposed
regulator grants lower pressure overshoot and
oscillation amplitude. PI parameters are tuned for a
narrow working range, while the fact that the
dynamic performances of the GPC are independent
from the set-point demonstrates the superiority and
robustness of such control approach.
5 CONCLUSIONS
In this paper we have presented a simple lumped
parameters control-oriented model of a CNG
injection system. The model equations describe the
main fluid-dynamic phenomena and require a
minimal set of geometric data. By using the model
equations, we have designed a linear Generalized
Predictive Controller to regulate the injection
pressure, and then we have compared its
performances with those obtained with a standard PI
controller. The proposed controller structure is
simple enough for on-line computation and
simulation results validate the control approach.
Future work will concern a narrow model validation
through lab tests and the implementation of a
nonlinear control strategy.
REFERENCES
Cantore, G., Mattarelli, E., Boretti, A., 1999. Experimental
and Theoretical analysis of a Diesel Fuel Injection
System. SAE Technical Paper 1999-01-0199.
Heywood, J., 1988. Internal Combustion Engine
Fundamentals, McGraw-Hill. New York, 1988.
Kouremenos, D. A., Hountalas, D.T., Kouremenos, A.D.,
1999. Development and Validation of a Detailed Fuel
Injection System Simulation Model for Diesel
Engines, SAE Technical Paper 1999-01-0527.
Maione, B., Lino, P., De Matthaeis, S., Amorese, C.,
Manodoro, D., Ricco, R., 2004a. Modeling and
Control of a Compressed Natural Gas Injection
System, WSEAS Transactions on Systems, Issue 5,
Vol.3, pp. 2164-2169.
Maione, B., Lino, P., Rizzo, A., 2004b. Neural Network
Nonlinear Modeling of a Common Rail Injection
System for a CNG Engine, WSEAS Transactions on
Systems, Issue 5, Vol.3, pp. 2282-2287.
Mulemane, A., Han, J.S., Lu, P.H., Yoon, S.J., Lai, M.C.,
2004. Modeling Dynamic Behavior of Diesel Fuel
Injection Systems, SAE Technical Paper 2004-01-
0536, 2004.
Rossiter, J.A., 2003. Model-Based Predictive Control: a
Practical Approach, CRC Press. New York.
Smith, C.A., Corripio, A.B., 1997. Principles and Practice
of Automatic Process Control, Wiley & Sons. New
York, 2
nd
Edition.
Weaver, C. S., 1989. Natural Gas Vehicles - A Review of
the State of the Art. In Gaseous Fuels: Technology,
Performance and Emissions SP-798, Society of
Automotive Engineers, Inc., Warrendale, PA.
Zucrow, M., Hoffman, J., 1976. Gas Dynamics, John
Wiley & Sons. New York.
ICINCO 2005 - ROBOTICS AND AUTOMATION
136