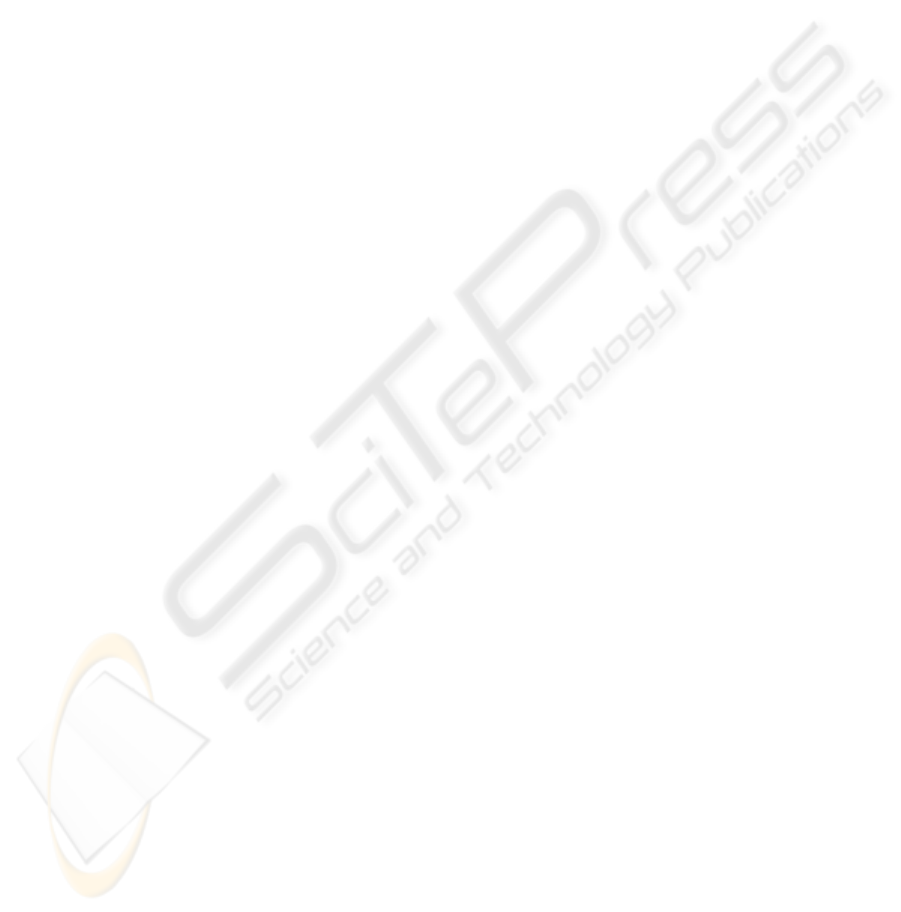
REAL-TIME MODELLING OF WOOD DRYING SYSTEMS
Learning from Experiment and Theory
Stanislaw Tarasiewicz
Department of Mechanical Engineering, Laval Université, Québec, Canada
Belkacem Kada
Department of Mechanical Engineering, Laval Université, Québec, Canada
Keywords: Mathematical modelling, numerical simulation, com
puter model, on-line identification, operating functions,
state variables.
Abstract: Predictive control in a wood drying systems is still at an early stage, because of the difficulties with the
estimating a temporal moisture distribution for the whole dried lumber. Therefore, based on the dry and
wet-bulb temperatures as the state variables the temporal moisture distribution in kiln-dried lumber is
determined from numerical solutions of mathematical model for the wood drying systems. This computer
model is represented by a set of several partial nonlinear differential equations coupled with the operating
functions and a set of several calculating algorithms. The accuracy of the model solutions in a real-time
calculation is evaluated by the on-line identification of the operating functions that represent both the
system parameters (heat transfer coefficients, thermal conductivity, heat capacity etc) and selected state
variables (air temperature, humidity, velocity etc).
1 INTRODUCTION
Though drying of lumber in the wood kiln is a
simultaneous heat and mass transfer process, the
temporal mass changes are less pronounced than the
heat (energy) changes because of high latent heat of
water and thus prevailing thermal effects during
evaporation and condensation. Therefore, the
classical approach to drying as water removal can
conveniently be regarded as a heat exchange process
between the drying gas (air) and the solid material
(lumber). Because the lumber boards for drying are
stacked into piles and several piles are placed in the
kiln, the kiln and its load is considered as a wood
drying system (WDS). Typically, the WDS is treated
as a lumped-parameter system, and thus its dynamic
behaviour can be described by the input-output
transfer functions. However, establishing a dynamic
mathematical model to be practical enough for
control applications requires so many simplifying
assumptions that the model hardly reflects the real
situation. A compromise between the complex but
adequate model and its simplification can be
obtained when taking advantage of the measured
temperature profiles in a given system, and solving
numerically the partial differential equations by
decomposing the solutions into the so-called
regulated variables at the defined boundary
conditions. The accuracy of these solutions has to be
evaluated by the on-line identification (OLI) system.
In return, the on-line identification, as a supporting
tool for computer modelling, allows determination
of the temperature profiles across the kiln as to avoid
conditions that may lead to lumber degradation.
2 MATHEMATICAL
FORMULATIONS
The model is based on the well established drying
mechanism for lumber. During the pre-heating
period, the temperature of stacked lumber is
equilibrated to the air temperature by heating at the
controlled rate to prevent condensation of water
vapour. At the end of this period, the moisture
content (MC) of lumber is assumed uniform. During
the constant rate period, the vapour pressure at the
lumber surface is equal to the saturated vapour
pressure, and the surface temperature approaches the
wet-bulb temperature.
132
Tarasiewicz S. and Kada B. (2005).
REAL-TIME MODELLING OF WOOD DRYING SYSTEMS - Learning from Experiment and Theory.
In Proceedings of the Second International Conference on Informatics in Control, Automation and Robotics - Signal Processing, Systems Modeling and
Control, pages 132-136
DOI: 10.5220/0001159601320136
Copyright
c
SciTePress