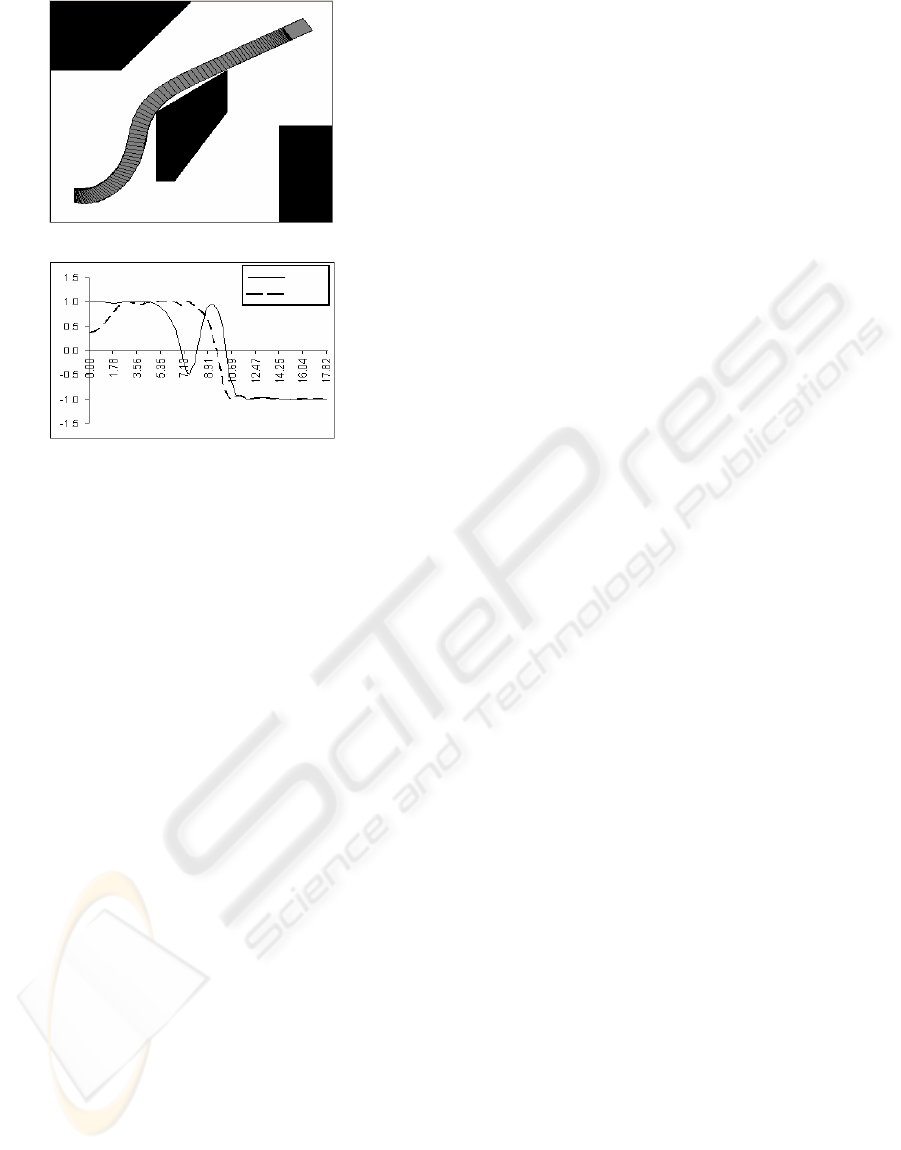
Figure 5b: Time evolution of joint torques
[Nm]
[1]
Time
ec
Figure 5a: Simulation result
= 17.82
ec.
8 CONCLUSION
We have demonstrated that a trajectory optimization
problem, that is an optimal control problem, can be
converted into a parametric optimization problem
using three different conversion modes. We shown
that using independent position parameters as
principle variables of the optimization problem
offers many facilities and leads to comparable
results to those obtained heavy and classical indirect
methods.
Furthermore, the simplicity and the efficiency of this
conversion mode allow us to use it to solve the
problem of optimal trajectory planning in complex
situations, in particular for holonomic and non-
holonomic systems.
ACKNOWLEDGMENTS
Authors would like to thank Prof. H. E. Lehtihet for
his suggestions and helpful discussions.
REFERENCES
Angeles J., 1997, Fundamentals of robotic mechanical
systems. Theory, methods, and algorithms, Springer
Edition.
Ascher U. M. & Petzold L. R., 1998, Computer Methods
for ordinary differential equations and differential-
algebraic equations, SIAM edition.
Bessonnet, G. 1992. Optimisation dynamique des
mouvements point à point de robots manipulateurs.
Thèse d’état, Université de Poitiers, France.
Betts, J. T. 1998. Survey of numerical methods for
trajectory optimization. Jour. Of Guidance, Cont. and
Dyn., 21(2), 193-207.
Bryson A. E., 1999, Dynamic Optimization, Addison
Wesley Longman, Inc.
Bicchi A., Pallottino L., Bray M., Perdomi P. , 2001,
Randomized parallel Simulation of constrained
multibody systems for VR/Haptic applications, Proc.
IEEE int. conf. on rob. & Aut., Korea.
Bobrow, J. E., Martin, B. J., Sohl, G., Wang, E. C., Park,
F. C., and Kim, J. 2001. Optimal robot motions for
physical criteria. Jour. Of Rob. Syst. 18 (12), 785-795.
Chen, Y., and Desrochers, A. 1990. A proof of the
structure of the minimum time control of robotic
manipulators using Hamiltonian formulation. IEEE
Trans. On Rob. and Aut. 6(3), pp388-393.
Chettibi T., H. E. Lehtihet, M. Haddad, S. Hanchi, 2004a,
Minimum cost trajectory planning for industrial
robots, European Journal of Mechanics/A, pp703-715.
Chettibi T., Haddad M., Rebai S., Hentout A., 2004b, A
Stochastic off line planner of optimal dynamic
motions for robotic manipulators, 1
st
Inter. Conf. on
Informatics, in Control, Automation and Robotics,
Portugal.
Dombre E. & Khalil W., 1999, Modélisation,
identification et commande des robots, second edition,
Hermes.
Geering, H. P., Guzzella, L., Hepner, S. A. R., and Onder,
C. H. 1986. Time-optimal motions of robots in
Assembly tasks. IEEE Trans. On Automatic control ,
Vol. AC-31, N°6.
Haddad M., Chettibi T., Lehtihet H. E. and Hanchi S.
2005. “A new approach for minimum time motion
planning problem of wheeled mobile robots”, accepted
at the 2005IFAC congress, Prague.
Hull, D. G. 1997. Conversion of optimal control problems
into parameter optimization problems, Jour. Of
Guidance, Cont. and Dyn., 20(1), 57-62.
Lazrak, M. 1996. Nouvelle approche de commande
optimale en temps final libre et construction
d’algorithmes de commande de systèmes articulés.
Thèse d’état, Université de Poitiers.
Steinbach M.C., 1995, Fast recursive SQP methods for
large scale optimal control problem. PhD thesis,
Universität Heidelberg.
Stryk, O. V. and Bulirsch R. 1993. Direct and indirect
methods for trajectory optimization. Annals of
Operations research, Vol 37, pp. 357-373.
Stryk, O. V. 1993, Numerical solution of optimal control
problems by direct collocation. Optimal control theory
and numerical methods, Int. series of Numerical
Mathematics, Vol 111, pp 129-143.
Yamamoto, M., Iwamura M. and Mohri A. (1999). Quasi-
time-Optimal Motion Planning of Mobile Platforms in
the presence of obstacles, Proc. Of 1999 IEEE ICRA,
2958-2962.
ICINCO 2005 - ROBOTICS AND AUTOMATION
10